Reducir la porosidad durante la sinterización es un objetivo fundamental en el procesamiento de materiales para conseguir productos más densos, resistentes y fiables.La porosidad de un material sinterizado depende de varios factores, como la porosidad inicial del compacto verde, la temperatura de sinterización, el tiempo de sinterización, la atmósfera, el tamaño de las partículas y la presión aplicada.La optimización de estas variables permite minimizar la porosidad y mejorar las propiedades mecánicas y físicas del material.Las estrategias clave incluyen el control de la porosidad inicial del compacto verde, la selección de temperaturas y tiempos de sinterización adecuados, el uso de partículas de menor tamaño y la aplicación de presión externa durante la sinterización.Además, la atmósfera de sinterización y la velocidad de calentamiento desempeñan un papel importante en la eliminación de poros y la densificación.
Explicación de los puntos clave:
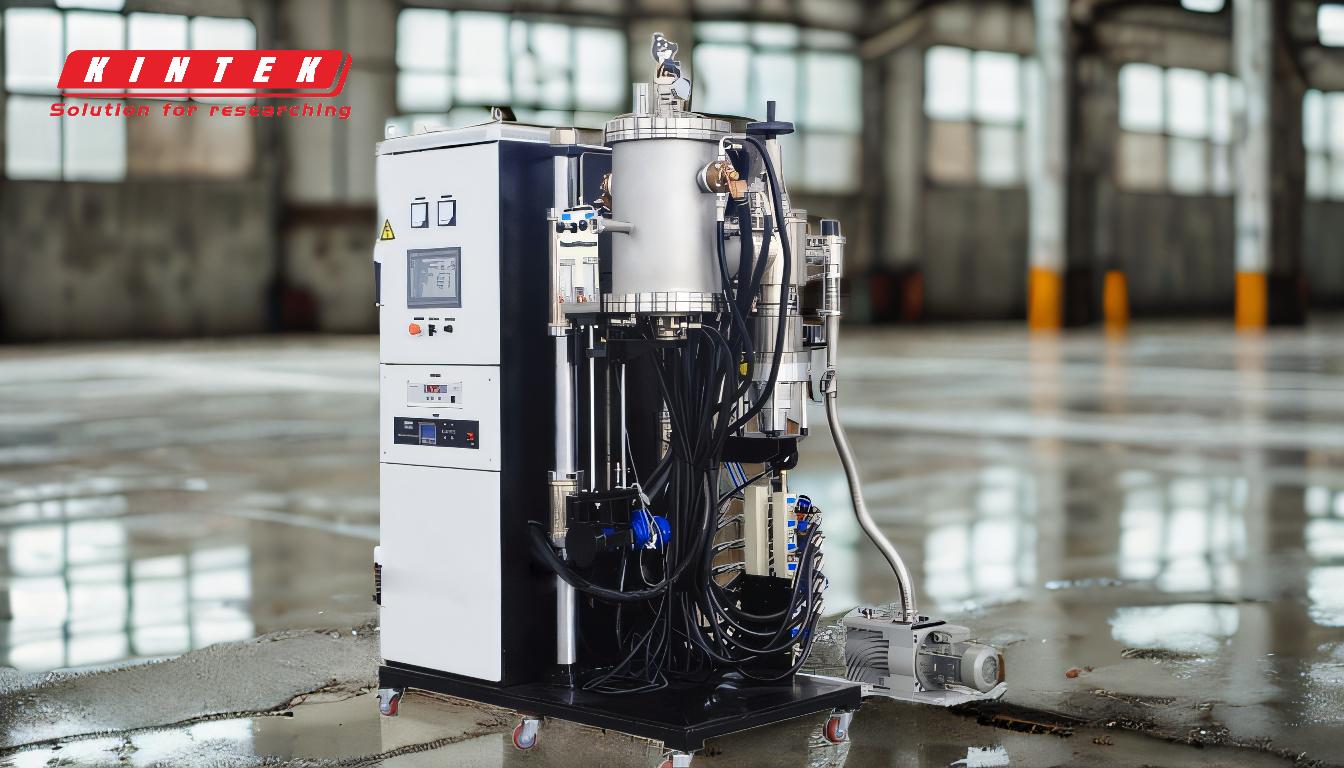
-
Controlar la Porosidad Inicial del Compacto Verde:
- La porosidad inicial del compacto verde (el material sin sinterizar) es un factor crítico para determinar la porosidad final tras la sinterización.Una porosidad inicial más baja conduce generalmente a un producto final más denso.
- Para reducir la porosidad inicial, hay que aplicar técnicas de compactación adecuadas, como el uso de presiones de compactación más altas o la optimización de la distribución del tamaño de las partículas en el compacto en verde.El empaquetamiento uniforme de las partículas minimiza los grandes huecos y favorece una mejor densificación durante la sinterización.
-
Optimización de la temperatura de sinterización:
- La temperatura de sinterización influye significativamente en la reducción de la porosidad.Las temperaturas más altas mejoran la difusión atómica, lo que ayuda a eliminar los poros al favorecer la unión de las partículas y el crecimiento de los granos.
- Sin embargo, las temperaturas excesivamente altas pueden provocar un crecimiento indeseado de los granos o la descomposición del material.Por lo tanto, es esencial identificar la temperatura de sinterización óptima para el material específico a fin de equilibrar la reducción de la porosidad y la integridad del material.
-
Ajustar el tiempo de sinterización:
- Los tiempos de sinterización más largos dejan más tiempo para la eliminación de poros mediante mecanismos como la difusión límite y la difusión reticular.Esto es especialmente importante para los materiales con una porosidad inicial elevada o los que requieren difusión en estado sólido, como las cerámicas de óxido puro.
- Sin embargo, los tiempos de sinterización excesivamente largos pueden provocar un exceso de sinterización, lo que puede degradar las propiedades del material.El tiempo de sinterización debe optimizarse en función del material y de la porosidad final deseada.
-
Utilizar tamaños de partícula más pequeños:
- Las partículas más pequeñas tienen una mayor relación superficie/volumen, lo que aumenta la fuerza motriz para la sinterización y mejora la densificación.Las partículas más pequeñas también reducen las distancias de difusión, lo que hace que la eliminación de poros sea más eficaz.
- Garantice una distribución uniforme del tamaño de las partículas para evitar problemas de densificación localizada y promover una sinterización homogénea.
-
Aplicar presión externa (prensado en caliente o prensado isostático en caliente):
- La aplicación de presión durante la sinterización (por ejemplo, prensado en caliente o prensado isostático en caliente) puede reducir significativamente la porosidad al potenciar la reordenación de las partículas y eliminar los huecos.La sinterización asistida por presión es especialmente eficaz para materiales difíciles de densificar mediante métodos de sinterización convencionales.
- Este método reduce el tiempo de sinterización y disminuye la temperatura de sinterización necesaria, lo que lo convierte en una potente herramienta para conseguir materiales de baja porosidad.
-
Control de la atmósfera de sinterización:
- La atmósfera de sinterización (por ejemplo, aire, vacío o gases inertes como el argón o el nitrógeno) afecta a la cinética de sinterización y a la porosidad final.Por ejemplo, una atmósfera de vacío o inerte puede evitar la oxidación y favorecer una mejor densificación en determinados materiales.
- La elección de la atmósfera depende de la reactividad del material y de las propiedades deseadas del producto final.
-
Optimizar la velocidad de calentamiento:
- La velocidad de calentamiento influye en el proceso de densificación.Una velocidad de calentamiento más lenta permite una distribución más uniforme de la temperatura y una mejor eliminación de los poros, mientras que una velocidad de calentamiento más rápida puede provocar gradientes térmicos y una densificación incompleta.
- La velocidad de calentamiento óptima depende del material y del equipo de sinterización utilizado.
-
Mejorar la composición y la homogeneidad:
- Una composición homogénea con un mínimo de impurezas favorece una mejor sinterización y reduce la porosidad.Las impurezas pueden actuar como barreras a la difusión y dificultar la eliminación de poros.
- A veces pueden utilizarse aditivos o dopantes para mejorar el comportamiento de sinterización y reducir la porosidad.
Controlando cuidadosamente estos factores, es posible minimizar la porosidad durante la sinterización y producir materiales con propiedades mecánicas, térmicas y eléctricas superiores.Cada sistema de materiales puede requerir ajustes específicos para lograr los resultados deseados, pero los principios descritos anteriormente proporcionan una base sólida para reducir la porosidad en los materiales sinterizados.
Tabla resumen:
Factor | Impacto en la reducción de la porosidad |
---|---|
Porosidad inicial | Una menor porosidad inicial en el compacto verde conduce a un producto final más denso. |
Temperatura de sinterización | Las temperaturas más elevadas favorecen la difusión atómica, pero deben evitar un crecimiento excesivo del grano. |
Tiempo de sinterización | Los tiempos más largos permiten la eliminación de poros pero evitan el exceso de sinterización. |
Tamaño de las partículas | Las partículas más pequeñas aumentan la densificación y reducen las distancias de difusión. |
Presión externa | La sinterización asistida por presión (por ejemplo, el prensado en caliente) reduce significativamente la porosidad. |
Atmósfera de sinterización | El vacío o los gases inertes evitan la oxidación y favorecen la densificación. |
Velocidad de calentamiento | Las velocidades más lentas garantizan una distribución uniforme de la temperatura y una mejor eliminación de los poros. |
Composición y homogeneidad | Los materiales homogéneos con impurezas mínimas mejoran la sinterización y reducen la porosidad. |
¿Está preparado para optimizar su proceso de sinterización y obtener materiales más densos y resistentes? Póngase en contacto con nuestros expertos para obtener soluciones a medida.