El endurecimiento del acero, si bien es beneficioso para aumentar su resistencia y resistencia al desgaste, presenta varias desventajas. Estos incluyen mayor fragilidad, ductilidad reducida y potencial de agrietamiento durante el proceso de endurecimiento. Además, el proceso puede provocar cambios dimensionales y tensiones residuales, que pueden requerir tratamientos adicionales como el templado para mitigarlos. La complejidad y el costo del proceso de endurecimiento, incluida la necesidad de un control preciso de la temperatura y tratamientos posteriores al endurecimiento, también plantean desafíos. A continuación, exploramos estas desventajas en detalle, brindando una comprensión integral de las ventajas y desventajas involucradas en el endurecimiento del acero.
Puntos clave explicados:
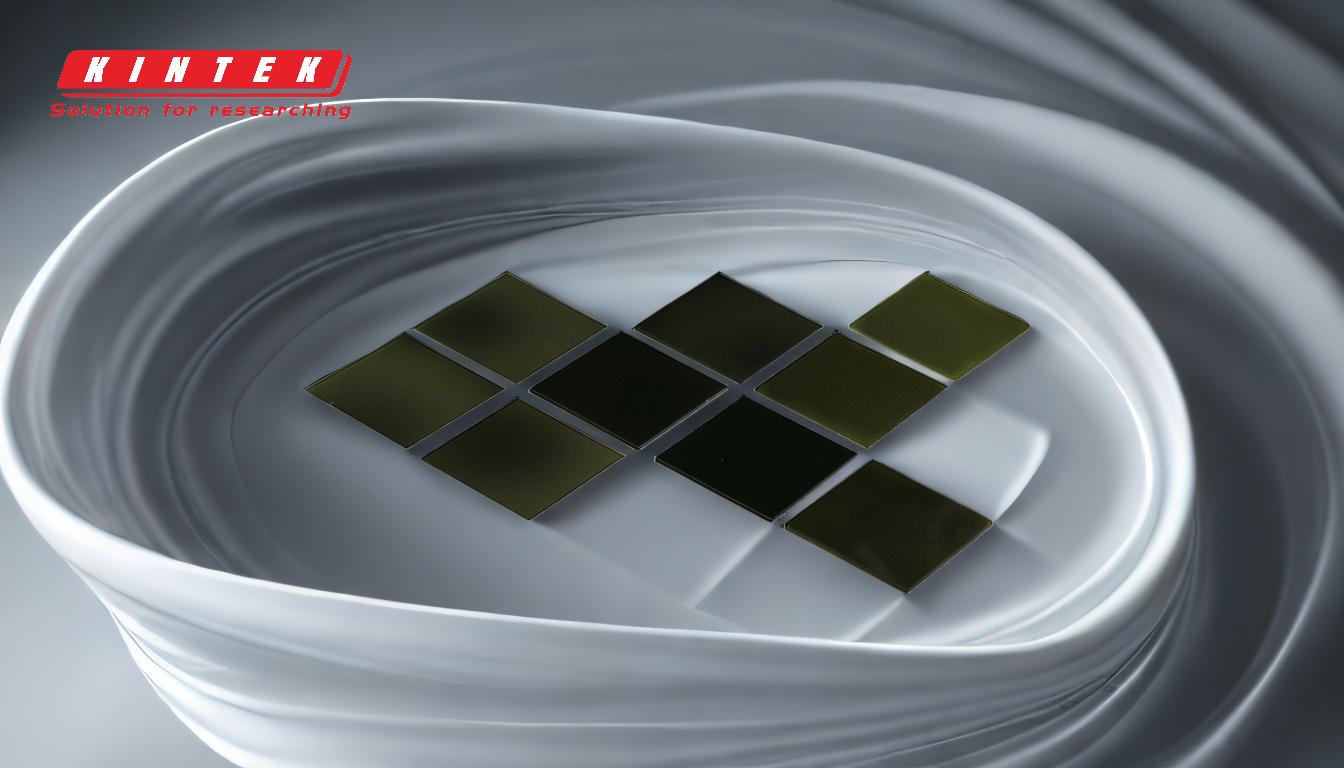
-
Mayor fragilidad:
- El acero endurecido aumenta significativamente su dureza pero también lo hace más quebradizo. Esta fragilidad puede conducir a un mayor riesgo de fractura bajo impacto o tensión, especialmente en aplicaciones donde se requiere tenacidad.
- El equilibrio entre dureza y tenacidad es una consideración crítica, ya que el acero demasiado frágil puede fallar catastróficamente en servicio.
-
Ductilidad reducida:
- La ductilidad, la capacidad de un material para deformarse bajo tensión de tracción, se reduce después del endurecimiento. Esto hace que el acero sea menos capaz de resistir el estiramiento o la flexión sin romperse.
- Las aplicaciones que requieren una deformación o flexibilidad significativas pueden encontrar que el acero endurecido no es adecuado debido a esta ductilidad reducida.
-
Potencial de agrietamiento:
- El rápido enfriamiento involucrado en el proceso de endurecimiento puede inducir tensiones térmicas que provoquen grietas en el acero. Esto es particularmente problemático en geometrías complejas o secciones gruesas donde las velocidades de enfriamiento son desiguales.
- El agrietamiento no sólo compromete la integridad estructural del acero sino que también aumenta la probabilidad de falla durante el uso.
-
Cambios dimensionales y deformaciones:
- El endurecimiento puede causar cambios dimensionales y deformaciones debido a las velocidades de enfriamiento desiguales y las transformaciones de fase que ocurren dentro del acero.
- Estos cambios pueden requerir procesos adicionales de mecanizado o enderezamiento, lo que aumenta el costo general y la complejidad de la fabricación.
-
Tensiones residuales:
- El proceso de endurecimiento introduce tensiones residuales dentro del acero, que pueden provocar distorsión o falla prematura bajo carga.
- Para mitigar estas tensiones, a menudo se requieren tratamientos adicionales, como el templado, lo que aumenta el tiempo y el costo de producción.
-
Complejidad y Costo del Proceso:
- El endurecimiento del acero requiere un control preciso de las velocidades de calentamiento y enfriamiento, lo que a menudo requiere equipos y experiencia especializados.
- La necesidad de tratamientos posteriores al endurecimiento, como el revenido, aumenta aún más la complejidad y el costo, haciendo que el proceso sea menos económico para algunas aplicaciones.
-
Aplicabilidad limitada a ciertos grados de acero:
- No todos los grados de acero son aptos para el endurecimiento. La eficacia del endurecimiento depende del contenido de carbono del acero y de los elementos de aleación.
- Esta limitación restringe la gama de materiales que pueden endurecerse eficazmente, lo que potencialmente requiere el uso de grados de acero más caros o menos disponibles.
-
Preocupaciones ambientales y de seguridad:
- El proceso de endurecimiento a menudo implica el uso de aceites de enfriamiento u otros medios de enfriamiento, que pueden presentar riesgos ambientales y de seguridad.
- Es necesario un manejo y eliminación adecuados de estos materiales, lo que se suma a los desafíos operativos y los requisitos de cumplimiento normativo.
En resumen, si bien el endurecimiento del acero ofrece importantes beneficios en términos de resistencia y resistencia al desgaste, también introduce varias desventajas que deben gestionarse con cuidado. Estos incluyen mayor fragilidad, ductilidad reducida, potencial de agrietamiento, cambios dimensionales, tensiones residuales y la complejidad y costo del proceso. Comprender estas compensaciones es esencial para tomar decisiones informadas en la selección y el tratamiento del acero para diversas aplicaciones.
Tabla resumen:
Desventaja | Descripción |
---|---|
Mayor fragilidad | Mayor dureza pero mayor riesgo de fractura bajo tensión. |
Ductilidad reducida | Menos capacidad de deformarse bajo tensión de tracción, lo que lo hace propenso a romperse. |
Potencial de agrietamiento | Las tensiones térmicas durante el enfriamiento rápido pueden provocar grietas. |
Cambios dimensionales | El enfriamiento desigual provoca deformaciones, lo que requiere mecanizado adicional. |
Tensiones residuales | Las tensiones internas pueden causar distorsión o falla, lo que requerirá un templado. |
Complejidad y costo | Requiere un control preciso de la temperatura y tratamientos de posendurecimiento. |
Aplicabilidad limitada | No todos los grados de acero son aptos para el endurecimiento. |
Riesgos ambientales y de seguridad | Los aceites de enfriamiento y los medios de enfriamiento presentan riesgos y requieren un manejo cuidadoso. |
¿Necesita ayuda para elegir el tratamiento de acero adecuado? Póngase en contacto con nuestros expertos hoy ¡Para soluciones personalizadas!