La sinterización es un proceso de fabricación que implica la fusión de partículas para formar una masa sólida. Se suele utilizar para materiales con puntos de fusión elevados, como metales, cerámicas y polímeros.La elección del aglutinante en la sinterización depende del material que se procese y de las propiedades deseadas del producto final.Los aglutinantes son cruciales, ya que ayudan a dar forma al material antes de la sinterización y a menudo se queman o descomponen durante el proceso.Los aglutinantes más comunes son los compuestos orgánicos, los polímeros y, a veces, los materiales inorgánicos, dependiendo de la aplicación.En el caso de los metales, suelen utilizarse aglutinantes como la cera o los polímeros, mientras que las cerámicas pueden requerir aditivos orgánicos para mejorar su manipulación antes de la sinterización.La selección de un aglutinante es fundamental para garantizar la integridad y el rendimiento del producto sinterizado.
Explicación de los puntos clave:
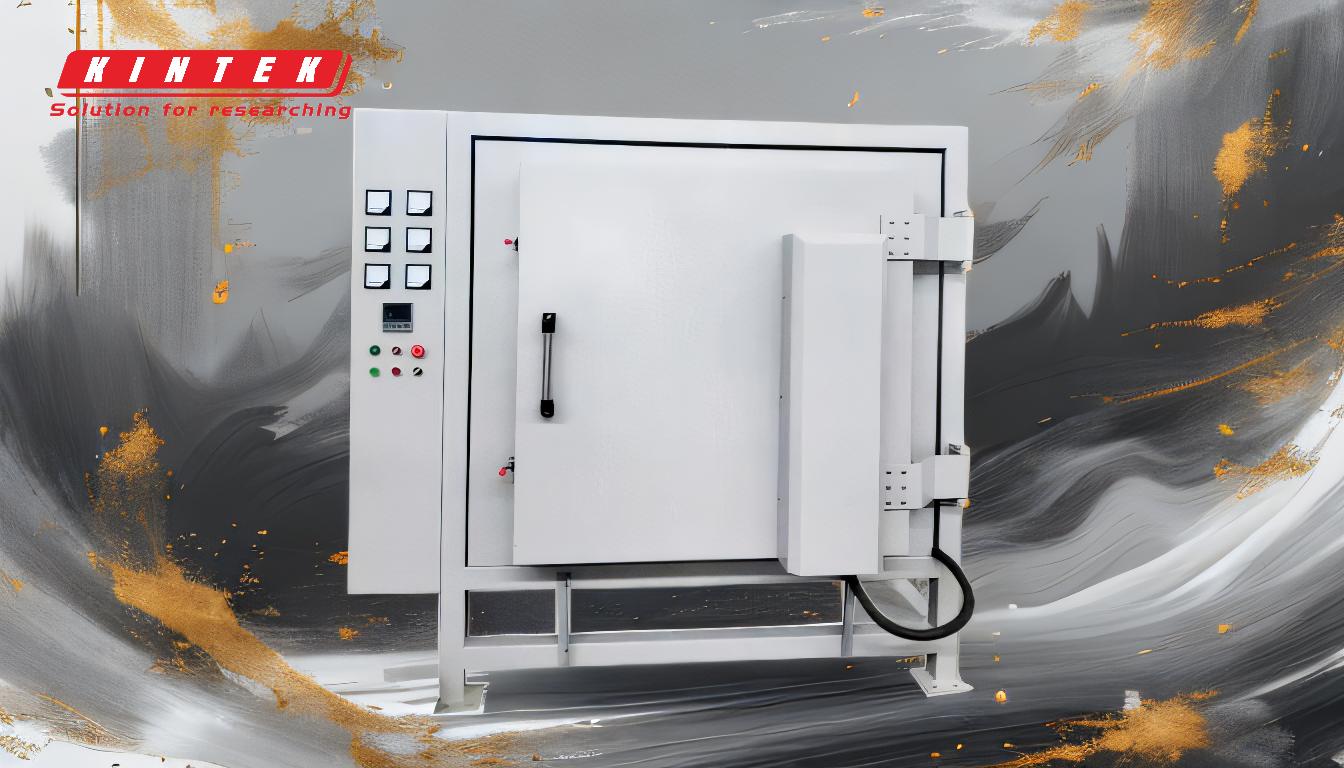
-
Papel de los aglutinantes en la sinterización:
- Los aglutinantes son esenciales en el proceso de sinterización, ya que ayudan a dar al material la forma deseada antes de que se produzca la sinterización propiamente dicha.
- Proporcionan resistencia temporal a la pieza verde (sin sinterizar), lo que permite manipularla y transportarla sin que se rompa.
- Durante la sinterización, los aglutinantes suelen quemarse o descomponerse, dejando el material sinterizado con las propiedades deseadas.
-
Tipos de ligantes utilizados:
- Aglutinantes orgánicos:Se utilizan habitualmente en la sinterización de metales.Algunos ejemplos son las ceras, los polímeros y otros compuestos orgánicos que pueden eliminarse fácilmente durante el proceso de sinterización.
- Ligantes inorgánicos:Son menos comunes pero pueden utilizarse en aplicaciones específicas, especialmente en la sinterización de cerámica, donde pueden mejorar ciertas propiedades del producto final.
- Ligantes poliméricos:Se utilizan ampliamente en la sinterización de metales y cerámicas.Ofrecen una buena adherencia y pueden adaptarse para descomponerse a temperaturas específicas, lo que es crucial para el proceso de sinterización.
-
Ligantes para aplicaciones específicas:
- Para metales:A menudo se utilizan aglutinantes como el polietilenglicol (PEG) o el alcohol polivinílico (PVA).Estos aglutinantes se eligen por su capacidad para proporcionar una buena resistencia en verde y su facilidad de eliminación durante la sinterización.
- Para cerámica:Los aditivos orgánicos, como el butiral de polivinilo (PVB) o las resinas acrílicas, se utilizan para mejorar la manipulación y la conformación de los polvos cerámicos antes de la sinterización.Estos aglutinantes también ayudan a reducir la afinidad al agua de las materias primas cerámicas, lo que facilita su procesamiento.
- Para polímeros:En la sinterización de polímeros, los aglutinantes no suelen ser necesarios, ya que el propio polímero actúa como material y como aglutinante.Sin embargo, en algunos casos, pueden utilizarse plastificantes u otros aditivos para mejorar el proceso de sinterización.
-
Consideraciones para la selección del aglutinante:
- Compatibilidad:El aglutinante debe ser compatible con el material a sinterizar.No debe reaccionar negativamente con el material ni degradar sus propiedades.
- Temperatura de descomposición:El aglutinante debe descomponerse a una temperatura inferior a la temperatura de sinterización del material.Esto garantiza que el aglutinante se elimine completamente durante el proceso de sinterización, sin dejar residuos que puedan afectar al producto final.
- Impacto medioambiental:La elección del aglutinante también puede verse influida por consideraciones medioambientales.Por ejemplo, algunos aglutinantes pueden liberar gases nocivos durante su descomposición, lo que podría ser motivo de preocupación en determinados entornos de fabricación.
-
Avances en la tecnología de aglutinantes:
- Con el avance de las tecnologías de sinterización, especialmente en la fabricación aditiva, ha habido un impulso hacia el desarrollo de aglutinantes que ofrecen un mejor rendimiento y beneficios medioambientales.
- Los aglutinantes más recientes se están diseñando para descomponerse de forma más limpia, reduciendo el impacto medioambiental del proceso de sinterización.
- También se están investigando aglutinantes que puedan reciclarse o reutilizarse, mejorando aún más la sostenibilidad del proceso de sinterización.
En resumen, la elección del aglutinante en la sinterización es un factor crítico que influye en el éxito del proceso.El aglutinante debe seleccionarse cuidadosamente en función del material sinterizado, las propiedades deseadas del producto final y las consideraciones medioambientales.A medida que las tecnologías de sinterización sigan evolucionando, también lo harán los aglutinantes utilizados en el proceso, dando lugar a métodos de fabricación más eficientes y sostenibles.
Cuadro sinóptico:
Aspecto | Detalles |
---|---|
Papel de los aglutinantes | Dan forma a los materiales, proporcionan resistencia en verde y se descomponen durante la sinterización. |
Tipos de aglutinantes | Ligantes orgánicos (ceras, polímeros), inorgánicos y poliméricos. |
Aplicaciones específicas | Metales:PEG, PVA; Cerámicas:PVB, resinas acrílicas; Polímeros:Raramente necesarios. |
Criterios de selección | Compatibilidad, temperatura de descomposición, impacto medioambiental. |
Avances | Descomposición más limpia, ligantes reciclables y fabricación sostenible. |
Optimice su proceso de sinterización con el aglutinante adecuado. póngase en contacto con nuestros expertos para obtener soluciones a medida.