La calcinación y la sinterización son procesos térmicos utilizados en la metalurgia y la ciencia de los materiales, pero tienen finalidades distintas. La calcinación consiste principalmente en calentar minerales metálicos u otros materiales a altas temperaturas para eliminar componentes volátiles, como agua, dióxido de carbono u otras impurezas, sin fundir el material. Este proceso suele utilizarse para descomponer carbonatos, hidróxidos u otros compuestos en óxidos. Por otro lado, la sinterización consiste en calentar materiales metálicos o cerámicos en polvo a una temperatura inferior a su punto de fusión para unir las partículas entre sí, creando una masa sólida con mejores propiedades mecánicas. Aunque ambos procesos implican calentamiento, la calcinación se centra en la purificación, mientras que la sinterización se centra en la consolidación y el fortalecimiento.
Explicación de los puntos clave:
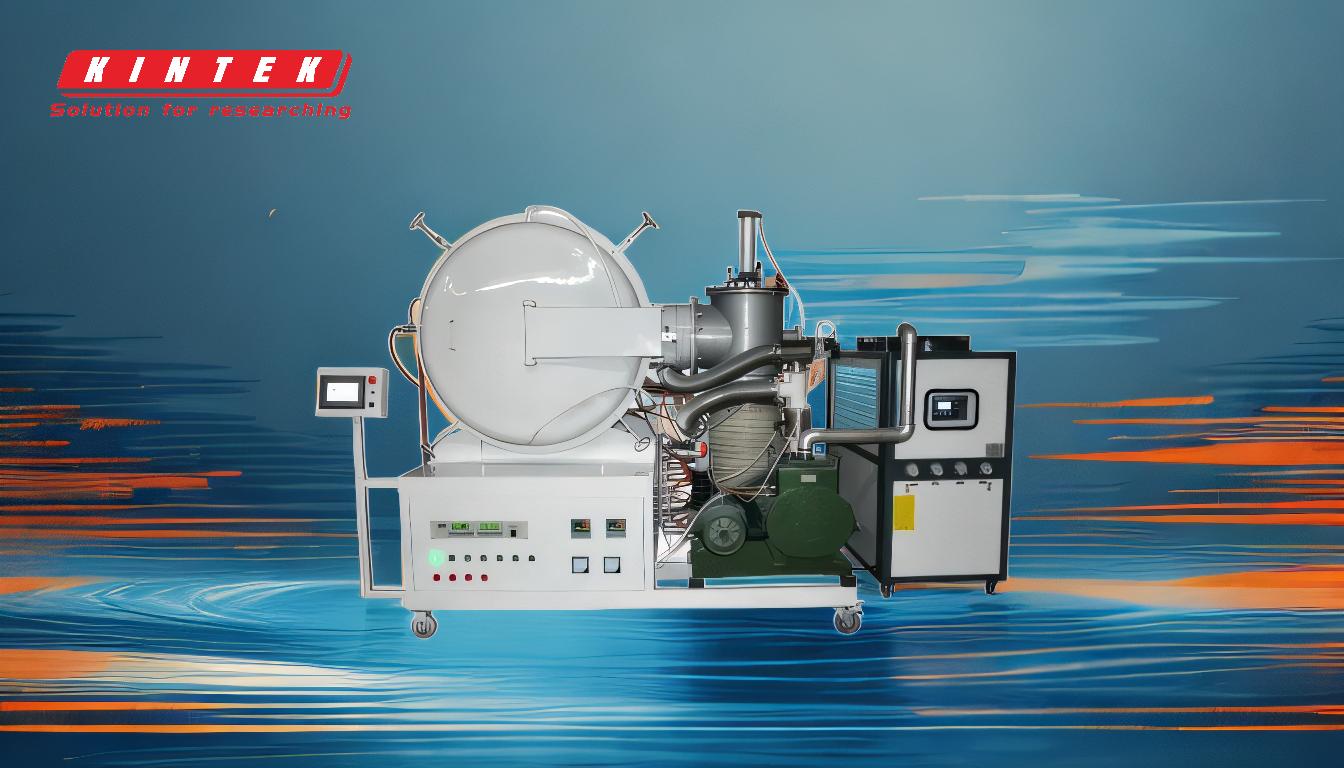
-
Definición y finalidad:
- Calcinación: Proceso térmico en el que los materiales, normalmente minerales metálicos, se calientan a altas temperaturas para eliminar sustancias volátiles como el agua, el dióxido de carbono o las impurezas. El objetivo es descomponer compuestos (por ejemplo, carbonatos en óxidos) y purificar el material.
- Sinterización: Proceso en el que materiales en polvo, como metales o cerámicas, se calientan a una temperatura inferior a su punto de fusión para unir las partículas entre sí. El objetivo es crear una estructura sólida y cohesiva con mejores propiedades mecánicas.
-
Temperatura:
- Calcinación: Suele producirse a temperaturas lo suficientemente altas como para descomponer los compuestos, pero por debajo del punto de fusión del material. Por ejemplo, el carbonato de calcio se descompone en óxido de calcio a unos 825°C.
- Sinterización: Se produce a temperaturas inferiores al punto de fusión del material, pero lo suficientemente altas como para permitir la unión de las partículas por difusión. La temperatura exacta depende del material, pero suele ser inferior a la de calcinación.
-
Cambios químicos frente a cambios físicos:
- Calcinación: Principalmente implica cambios químicos, como la descomposición de carbonatos o hidróxidos en óxidos, liberando gases como CO₂ o H₂O.
- Sinterización: Principalmente implica cambios físicos, como la unión de partículas por difusión, que conducen a la densificación y a la mejora de la resistencia mecánica.
-
Aplicaciones:
- Calcinación: Se utiliza en industrias como la producción de cemento (para producir cal a partir de piedra caliza), el refinado de metales (para eliminar las impurezas de los minerales) y la preparación de catalizadores (para activar materiales eliminando los componentes volátiles).
- Sinterización: Ampliamente utilizado en pulvimetalurgia para producir piezas metálicas, en fabricación de cerámica para crear componentes fuertes y densos, y en fabricación aditiva (impresión 3D) para fusionar materiales en polvo.
-
Resultado:
- Calcinación: Da lugar a un material purificado, a menudo en forma de óxido, con masa reducida debido a la eliminación de componentes volátiles.
- Sinterización: El resultado es un material más denso y resistente con mejores propiedades mecánicas, como dureza, resistencia y resistencia al desgaste.
-
Estado material:
- Calcinación: Normalmente comienza con un material sólido (por ejemplo, mineral o compuesto) y termina con un producto sólido tras la eliminación de impurezas.
- Sinterización: Comienza con materiales en polvo y termina con una estructura sólida y cohesiva tras la unión de las partículas.
-
Importancia industrial:
- Calcinación: Fundamental para producir materiales de gran pureza necesarios en diversos procesos industriales, como la siderurgia, la producción de vidrio y la fabricación de productos químicos.
- Sinterización: Esencial para la fabricación de componentes con formas y propiedades precisas, como engranajes, cojinetes y herramientas de corte, especialmente en industrias como la automovilística, la aeroespacial y la electrónica.
En resumen, aunque tanto la calcinación como la sinterización implican calentar materiales a altas temperaturas, difieren en sus objetivos, mecanismos y resultados. La calcinación es un proceso de purificación centrado en la eliminación de impurezas y la descomposición de compuestos, mientras que la sinterización es un proceso de consolidación destinado a unir partículas para crear materiales fuertes y densos. Comprender estas diferencias es crucial para seleccionar el proceso adecuado para aplicaciones industriales específicas.
Cuadro recapitulativo:
Aspecto | Calcinación | Sinterización |
---|---|---|
Propósito | Purificación mediante la eliminación de componentes volátiles (por ejemplo, agua, CO₂) | Consolidación y refuerzo mediante partículas aglomerantes |
Temperatura | Suficientemente alta para descomponer los compuestos (por ejemplo, 825°C para el CaCO₃) | Por debajo del punto de fusión para permitir la unión de las partículas |
Cambios | Química (descomposición de compuestos) | Físico (unión de partículas y densificación) |
Aplicaciones | Producción de cemento, refinado de metales, preparación de catalizadores | Pulvimetalurgia, fabricación cerámica, fabricación aditiva (impresión 3D) |
Resultado | Material purificado (por ejemplo, óxidos) con masa reducida | Material más denso y resistente con mejores propiedades mecánicas |
Estado material | Empieza y termina como sólido | Comienza como polvo y termina como una estructura cohesiva sólida |
Uso industrial | Siderurgia, producción de vidrio, fabricación de productos químicos | Industria automovilística, aeroespacial y electrónica |
¿Necesita ayuda para elegir el proceso térmico adecuado para su aplicación? Póngase en contacto con nuestros expertos