La calcinación y la sinterización son procesos térmicos utilizados en la metalurgia y la ciencia de los materiales, pero tienen finalidades distintas y funcionan en condiciones diferentes.La calcinación consiste en calentar un material, normalmente un mineral metálico, en presencia de aire u oxígeno para eliminar impurezas como el carbono, el agua u otras sustancias volátiles.La sinterización, por su parte, consiste en calentar materiales metálicos o cerámicos en polvo por debajo de su punto de fusión para fusionar las partículas y crear un objeto sólido con mejores propiedades mecánicas.Aunque ambos procesos se producen a temperaturas inferiores al punto de fusión del material, sus objetivos y resultados difieren significativamente.La calcinación es principalmente un proceso de purificación, mientras que la sinterización es un proceso de consolidación destinado a mejorar la resistencia y la integridad del material.
Explicación de los puntos clave:
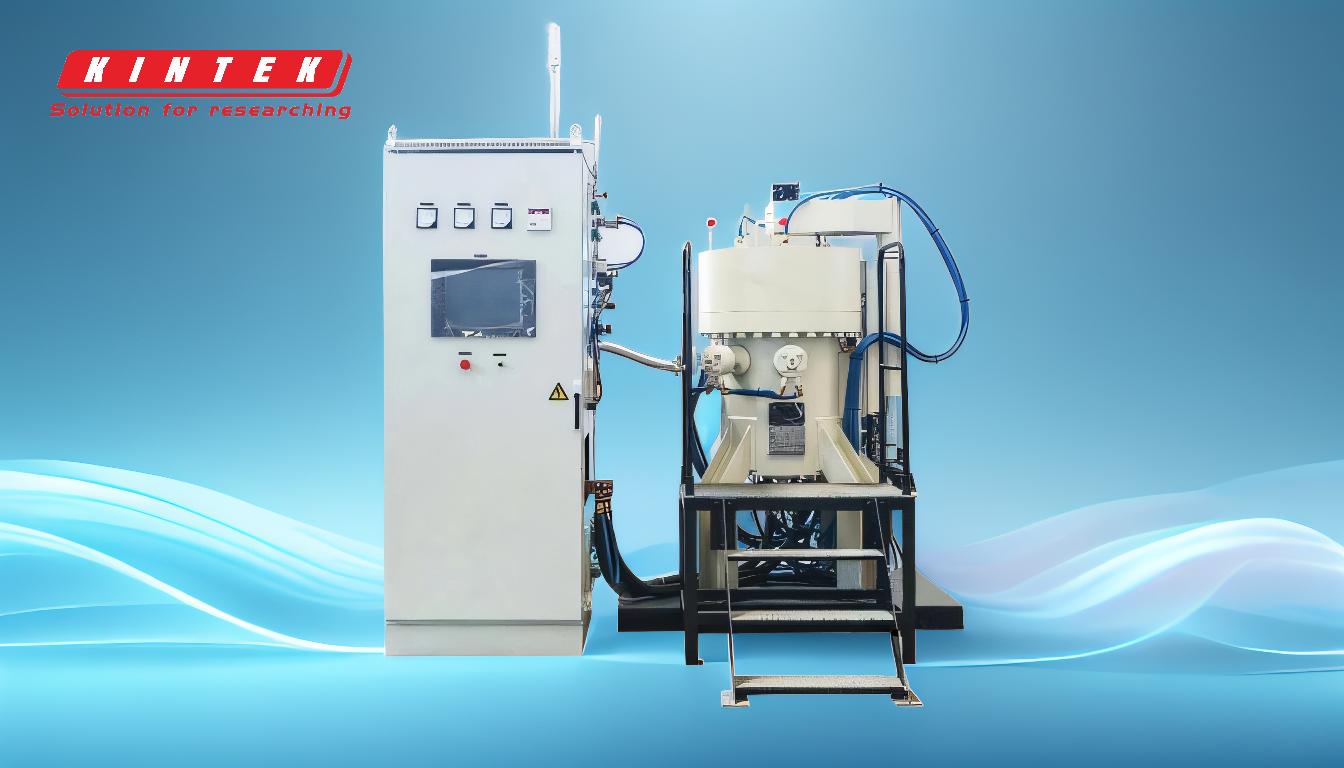
-
Definición y finalidad:
- Calcinación:Proceso térmico en el que se calienta un material (generalmente mineral metálico) en presencia de aire u oxígeno para eliminar impurezas como carbono, agua u otros compuestos volátiles.El objetivo es la purificación.
- Sinterización:Proceso térmico por el que se calientan materiales metálicos o cerámicos en polvo por debajo de su punto de fusión para fusionar las partículas y formar un objeto sólido.El objetivo es consolidar y mejorar las propiedades del material.
-
Gama de temperaturas:
- Ambos procesos tienen lugar a temperaturas inferiores al punto de fusión del material procesado.
- La calcinación suele implicar temperaturas más bajas que la sinterización, ya que su objetivo principal es expulsar las impurezas en lugar de fundir las partículas.
-
Cambios químicos frente a cambios físicos:
- Calcinación:Principalmente implica cambios químicos, como la descomposición de carbonatos o la oxidación de impurezas.
- Sinterización:Principalmente implica cambios físicos, en los que las partículas se unen mediante difusión y crecimiento del grano sin fundirse.
-
Aplicaciones:
- Calcinación:Comúnmente utilizado en la producción de cemento, cal y alúmina, donde es necesario eliminar las impurezas para lograr la composición química deseada.
- Sinterización:Ampliamente utilizado en pulvimetalurgia y cerámica para producir componentes de alta resistencia, densidad y precisión dimensional.
-
Equipo:
- Horno de calcinación:Diseñado para proporcionar un calentamiento controlado en una atmósfera oxidante, a menudo con características para gestionar los gases de escape y las impurezas.
- Horno de sinterización:Diseñado para proporcionar un calentamiento uniforme y un enfriamiento controlado, a menudo con características para mantener una atmósfera específica (por ejemplo, gas inerte) para evitar la oxidación o la contaminación.
-
Resultado:
- Calcinación:Da como resultado un material purificado con un contenido reducido de impurezas, a menudo en un estado más friable o poroso.
- Sinterización:El resultado es un objeto denso y sólido con propiedades mecánicas mejoradas, como resistencia, dureza y resistencia al desgaste.
-
Estado del material:
- Calcinación:Normalmente se parte de un material a granel o mineral, que puede triturarse o molerse antes del calentamiento.
- Sinterización:Se parte de material en polvo, que se compacta en la forma deseada antes de calentarlo.
-
Control de la atmósfera:
- Calcinación:A menudo requiere una atmósfera oxidante para facilitar la eliminación de impurezas.
- Sinterización:Puede requerir una atmósfera controlada (por ejemplo, gas inerte o vacío) para evitar la oxidación o la contaminación durante el proceso de adhesión.
-
Tratamiento posterior:
- Calcinación:El material resultante puede requerir un tratamiento adicional, como la molienda o el refinado, dependiendo de la aplicación.
- Sinterización:El producto sinterizado suele tener una forma próxima a la red y puede requerir un tratamiento posterior mínimo, como mecanizado o acabado superficial.
-
Importancia para la industria:
- Calcinación:Fundamental en industrias como la producción de cemento, el refinado de metales y la fabricación de productos químicos.
- Sinterización:Esencial en industrias como la automovilística, la aeroespacial y la electrónica para producir componentes de alto rendimiento.
Comprender estas diferencias clave ayuda a seleccionar el proceso y el equipo adecuados para las necesidades específicas de procesamiento de materiales, garantizando resultados óptimos en términos de pureza, resistencia y funcionalidad.
Cuadro recapitulativo:
Aspecto | Calcinación | Sinterización |
---|---|---|
Finalidad | Purificación de materiales mediante la eliminación de impurezas. | Consolidación de materiales en polvo para mejorar su resistencia e integridad. |
Temperatura | Temperaturas más bajas, por debajo del punto de fusión del material. | Temperaturas más altas, aún por debajo del punto de fusión del material. |
Cambios | Cambios principalmente químicos (por ejemplo, descomposición, oxidación). | Cambios principalmente físicos (por ejemplo, unión de partículas por difusión). |
Aplicaciones | Producción de cemento, cal y alúmina. | Pulvimetalurgia, cerámica, automoción, aeroespacial y electrónica. |
Equipos | Horno de calcinación con atmósfera oxidante. | Horno de sinterización con atmósfera controlada (por ejemplo, gas inerte o vacío). |
Resultado | Material purificado con impurezas reducidas, a menudo poroso. | Objeto sólido y denso con propiedades mecánicas mejoradas. |
Estado del material | Comienza con material a granel o mineral. | Comienza con material en polvo, compactado antes del calentamiento. |
Control de la atmósfera | Atmósfera oxidante para eliminar impurezas. | Atmósfera controlada para evitar la oxidación o la contaminación. |
Tratamiento posterior | Puede requerir esmerilado o refinado adicional. | Suele tener una forma próxima a la red, por lo que requiere un tratamiento posterior mínimo. |
Importancia para la industria | Producción de cemento, refinado de metales, fabricación de productos químicos. | Automoción, aeroespacial, electrónica para componentes de alto rendimiento. |
¿Necesita ayuda para elegir el proceso o equipo adecuado para el procesamiento de sus materiales? Póngase en contacto hoy mismo con nuestros expertos para recibir asesoramiento personalizado.