El depósito físico en fase vapor (PVD) se realiza a baja presión principalmente para crear un entorno controlado y limpio que garantice la transferencia eficaz del material de la fuente al sustrato.La baja presión minimiza las reacciones no deseadas en fase gaseosa, reduce la contaminación y aumenta la uniformidad del material depositado.También permite un recorrido libre medio más largo de los átomos, lo que posibilita una mayor transferencia de energía y una mejor adhesión del material al sustrato.Además, un entorno de vacío es crucial para aplicaciones que requieren gran precisión, como la fabricación de microchips, donde incluso los contaminantes más pequeños pueden causar defectos importantes.
Explicación de los puntos clave:
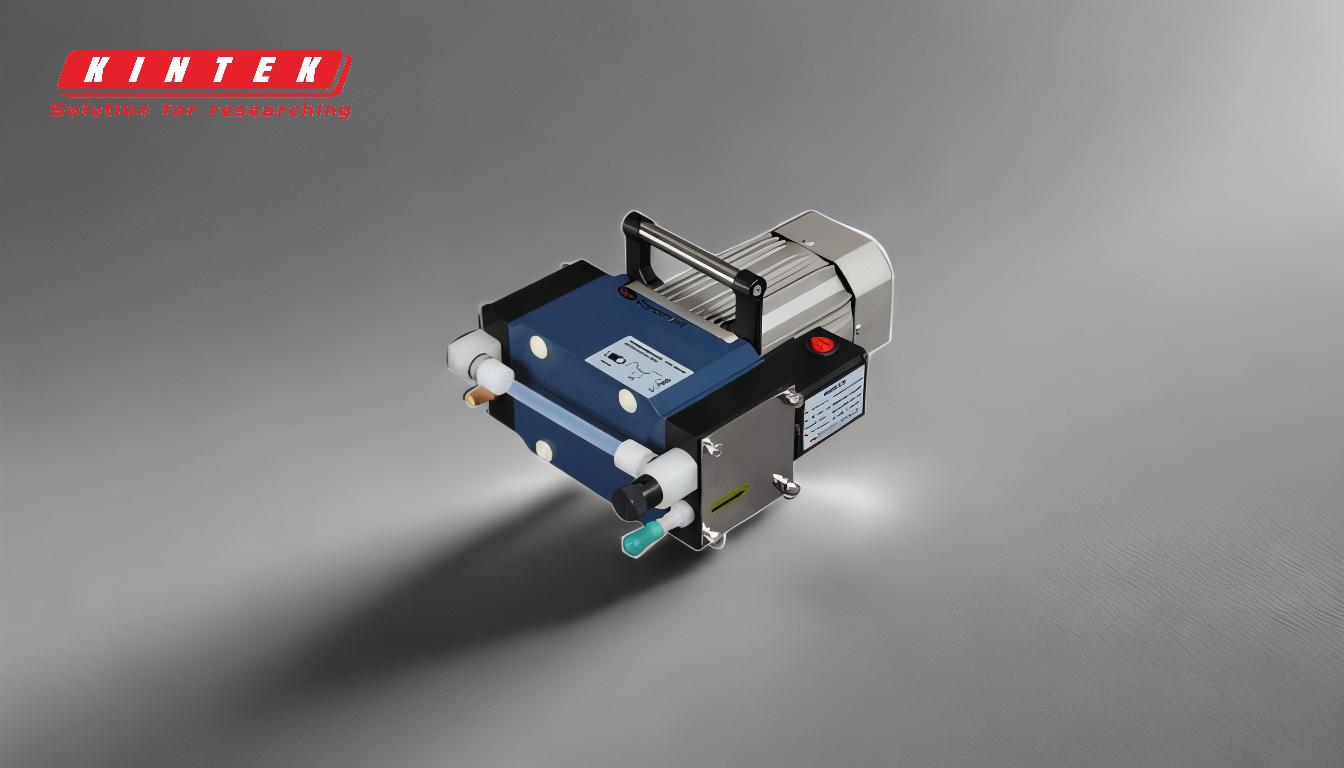
-
Minimización de las reacciones no deseadas en fase gaseosa:
- La baja presión reduce la probabilidad de reacciones químicas no deseadas entre el material vaporizado y los gases residuales de la cámara.
- Esto garantiza que el material depositado permanezca puro y se adhiera al sustrato sin formar compuestos no deseados.
-
Mayor uniformidad en todo el sustrato:
- Un entorno de baja presión permite una distribución más uniforme del material vaporizado por el sustrato.
- Esta uniformidad es crítica para aplicaciones que requieren espesores y propiedades uniformes, como en la fabricación de semiconductores.
-
Transferencia de material y adhesión mejoradas:
- En el vacío, el material vaporizado encuentra menos resistencia del aire u otros gases, lo que le permite desplazarse con mayor eficacia hasta el sustrato.
- La mayor energía de las partículas se traduce en una mayor adherencia al sustrato, lo que mejora la durabilidad y la calidad del revestimiento.
-
Reducción de la contaminación:
- Un entorno de alto vacío minimiza la presencia de contaminantes, como el polvo o la humedad, que pueden afectar negativamente a la calidad de la deposición.
- Esto es especialmente importante en sectores como el de la microelectrónica, en el que incluso las partículas más pequeñas pueden provocar defectos importantes.
-
Proceso de deposición controlado y repetible:
- La baja presión proporciona un entorno estable y predecible, lo que permite un control preciso del proceso de deposición.
- Esta repetibilidad es esencial para producir resultados consistentes en aplicaciones de alta precisión.
-
Mayor recorrido libre medio de los átomos:
- En el vacío, el recorrido libre medio de los átomos (la distancia media que recorre un átomo antes de colisionar con otro) aumenta considerablemente.
- Esto permite que los átomos viajen directamente al sustrato sin dispersarse, lo que garantiza un proceso de deposición más eficaz y dirigido.
-
Alta tasa de evaporación térmica:
- La baja presión facilita una mayor tasa de evaporación térmica, necesaria para vaporizar el material de partida.
- Esto garantiza que el material se transfiera eficazmente al sustrato en el momento oportuno.
-
Prevención de la contaminación gaseosa:
- Al mantener un entorno de baja presión, se minimiza la densidad de átomos o moléculas indeseables.
- Esto reduce el riesgo de incorporar impurezas al material depositado, garantizando un revestimiento más limpio y de mayor calidad.
-
Flexibilidad para iniciar reacciones químicas:
- Aunque el PVD suele evitar las reacciones químicas, la introducción de gases reactivos (como el oxígeno) de forma controlada puede utilizarse para crear revestimientos específicos, como los óxidos.
- Esta flexibilidad permite personalizar las propiedades de los materiales para satisfacer requisitos de aplicación específicos.
-
Fundamental para aplicaciones de alta precisión:
- Industrias como la microelectrónica, la óptica y el almacenamiento de datos (por ejemplo, CD y DVD) requieren entornos extremadamente limpios y controlados para fabricar productos sin defectos.
- Las condiciones de baja presión en PVD son esenciales para cumplir las estrictas normas de calidad de estas industrias.
Al comprender estos puntos clave, queda claro por qué la baja presión es un requisito fundamental para el éxito de los procesos de PVD.Garantiza revestimientos de alta calidad, uniformes y libres de contaminación, esenciales para una amplia gama de aplicaciones industriales.
Tabla resumen:
Beneficio clave | Explicación |
---|---|
Reacciones en fase gaseosa minimizadas | Reduce las reacciones químicas no deseadas, garantizando una deposición pura del material. |
Distribución uniforme del revestimiento | Garantiza un espesor y unas propiedades uniformes en todo el sustrato. |
Adhesión mejorada del material | Aumenta la energía de las partículas para obtener revestimientos más resistentes y duraderos. |
Contaminación reducida | Minimiza el polvo, la humedad y las impurezas para obtener revestimientos más limpios. |
Proceso de deposición controlado | Proporciona un entorno estable para obtener resultados repetibles y de alta precisión. |
Mayor recorrido libre medio de los átomos | Permite una transferencia eficaz y directa del material al sustrato. |
Alto índice de evaporación térmica | Facilita una vaporización y transferencia de material más rápidas. |
Prevención de la contaminación gaseosa | Reduce las impurezas, garantizando revestimientos de alta calidad. |
Flexibilidad en las reacciones químicas | Permite la personalización de revestimientos con gases reactivos. |
Crítico para aplicaciones de alta precisión | Esencial para industrias como la microelectrónica y la óptica que requieren productos sin defectos. |
¿Necesita una solución de PVD adaptada a sus necesidades? Póngase en contacto con nuestros expertos para obtener más información.