Digestores de microondas y electrotérmicos
Instrumentos de digestión por microondas
Los instrumentos de digestión por microondas revolucionan la preparación de muestras aprovechando la potencia de las microondas para calentar reactivos y muestras dentro de un recipiente cerrado. Este método no sólo acelera el proceso de digestión, sino que también mejora la eficiencia general de los flujos de trabajo del laboratorio.
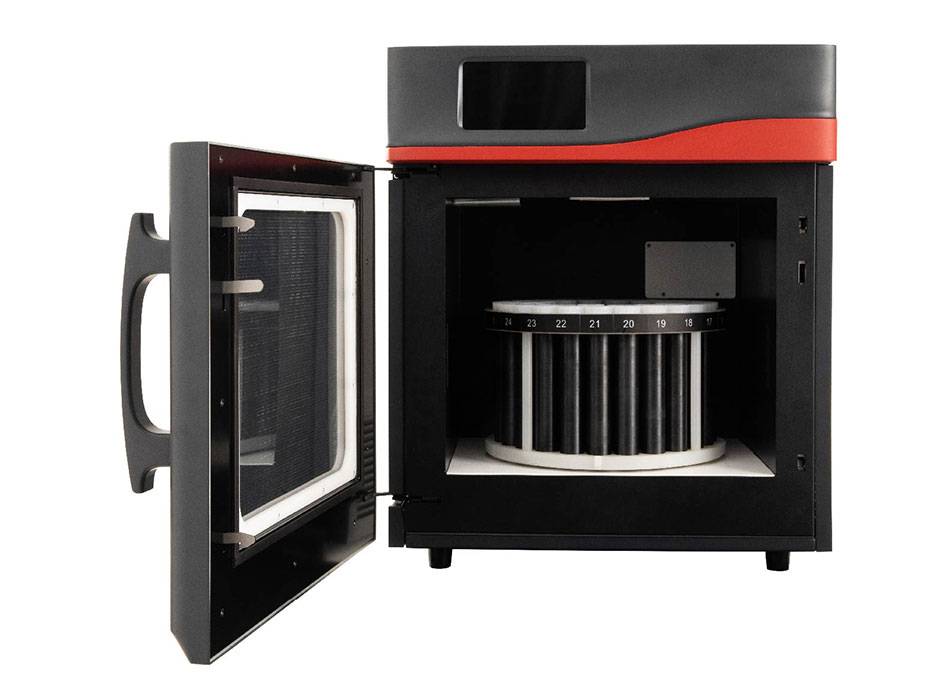
El sistema de contenedor cerrado empleado en los instrumentos de digestión por microondas es crucial por varias razones. En primer lugar, evita la pérdida de compuestos volátiles, garantizando la preservación de la integridad de la muestra. En segundo lugar, el entorno cerrado permite la acumulación de presión, lo que a su vez aumenta la temperatura de reacción. Esta temperatura elevada reduce significativamente el tiempo necesario para la digestión de la muestra, haciendo que el proceso sea más eficiente en términos de tiempo.
Además, el uso de microondas en este proceso introduce un mecanismo de calentamiento uniforme y rápido. A diferencia de los métodos de calentamiento tradicionales, las microondas penetran en la muestra, haciendo que las moléculas polares oscilen y generen calor internamente. Este calentamiento uniforme minimiza los puntos calientes y garantiza que toda la muestra se digiera uniformemente, lo que conduce a resultados más precisos y reproducibles.
En resumen, los instrumentos de digestión por microondas ofrecen un método superior para la preparación de muestras al combinar un calentamiento rápido, una mayor presión y un sistema de contenedor cerrado, todo lo cual contribuye a una digestión más rápida y eficaz de las muestras.
Instrumento de digestión electrotérmica
El instrumento de digestión electrotérmica es un sofisticado equipo de laboratorio diseñado para calentar muestras utilizando corriente alterna (CA). Este método aprovecha la interacción entre las moléculas polares y la frecuencia de microondas, un proceso que acelera significativamente el proceso de digestión.
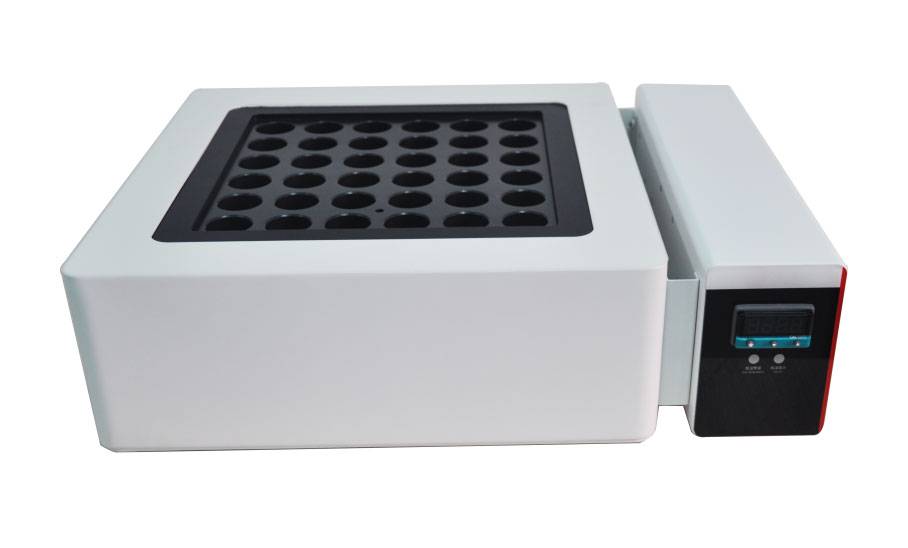
Cuando se aplica corriente alterna, las moléculas polares de la muestra cambian rápidamente su orientación en respuesta al campo eléctrico oscilante. Este rápido cambio de orientación aumenta la energía molecular de la muestra, lo que provoca el correspondiente aumento de la temperatura de la misma. La eficacia de este proceso se atribuye a los continuos y rápidos cambios de orientación molecular, que están sincronizados con la frecuencia de las microondas.
Este método de calentamiento ofrece varias ventajas con respecto a las técnicas de calentamiento tradicionales. En primer lugar, permite un calentamiento más uniforme, ya que la energía se distribuye uniformemente por la muestra. En segundo lugar, el rápido aumento de la energía molecular se traduce en tiempos de digestión de la muestra más rápidos, lo que lo convierte en una opción ideal para los laboratorios que requieren un alto rendimiento. Además, el entorno controlado que proporciona el instrumento de digestión electrotérmica minimiza el riesgo de contaminación de la muestra, lo que garantiza unos resultados más precisos y fiables.
En resumen, el instrumento de digestión electrotérmica aprovecha la potencia de la corriente alterna y la frecuencia de microondas para acelerar la digestión de muestras, ofreciendo una solución fiable y eficaz para los laboratorios que realizan procesos complejos de preparación de muestras.
Instrumentos de digestión UV y de horno
Instrumento de digestión UV
El instrumento de digestión UV emplea la fotocatálisis ultravioleta para generar radicales libres, que son especies altamente reactivas que pueden descomponer eficazmente la materia orgánica de las muestras líquidas. Este método es especialmente ventajoso en química analítica, donde la presencia de contaminantes orgánicos puede interferir en la medición precisa de metales pesados. Al utilizar luz UV, el instrumento desencadena una serie de reacciones fotoquímicas que degradan las moléculas orgánicas en compuestos más simples que no interfieren.
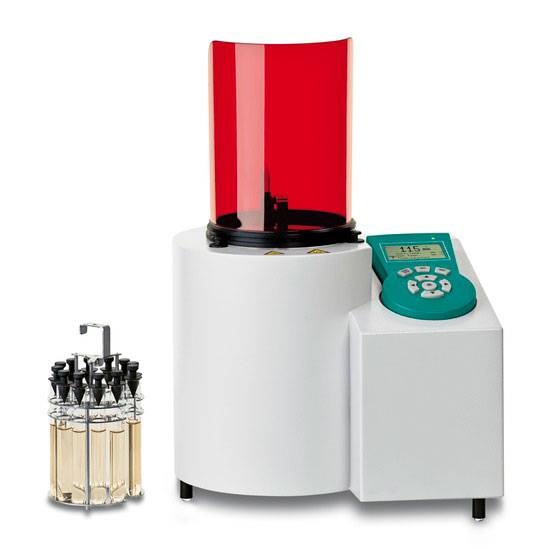
Este proceso no sólo garantiza la pureza de la muestra, sino que también mejora la precisión y fiabilidad de las pruebas analíticas posteriores. El instrumento de digestión UV es una herramienta fundamental en los laboratorios en los que el análisis de oligoelementos, como los metales pesados, es primordial. Proporciona un medio controlado y eficaz de preparación de muestras, minimizando el riesgo de contaminación y garantizando que los resultados reflejen la verdadera composición de la muestra.
Característica | Descripción |
---|---|
Tecnología | Fotocatálisis ultravioleta para generar radicales libres. |
Aplicación | Digestión de materia orgánica en muestras líquidas. |
Beneficio | Evita interferencias con las pruebas de metales pesados al descomponer los contaminantes orgánicos. |
Importancia | Mejora la precisión y fiabilidad en el análisis de oligoelementos. |
El instrumento de digestión UV es una piedra angular en los laboratorios analíticos modernos, ya que ofrece una solución sofisticada para la preparación de muestras que requieren la máxima precisión y limpieza.
Horno de digestión
El horno de digestión destaca como una pieza fundamental en la preparación de muestras de laboratorio, especialmente por su capacidad para gestionar el delicado equilibrio entre una digestión eficaz de las muestras y la seguridad medioambiental. Este instrumento emplea un mecanismo de calentamiento eléctrico de tipo pozo, que es decisivo para elevar rápidamente la temperatura de las muestras. Este método no sólo acelera el proceso de digestión, sino que también garantiza la gestión y contención eficaces de los gases nocivos generados durante la digestión.
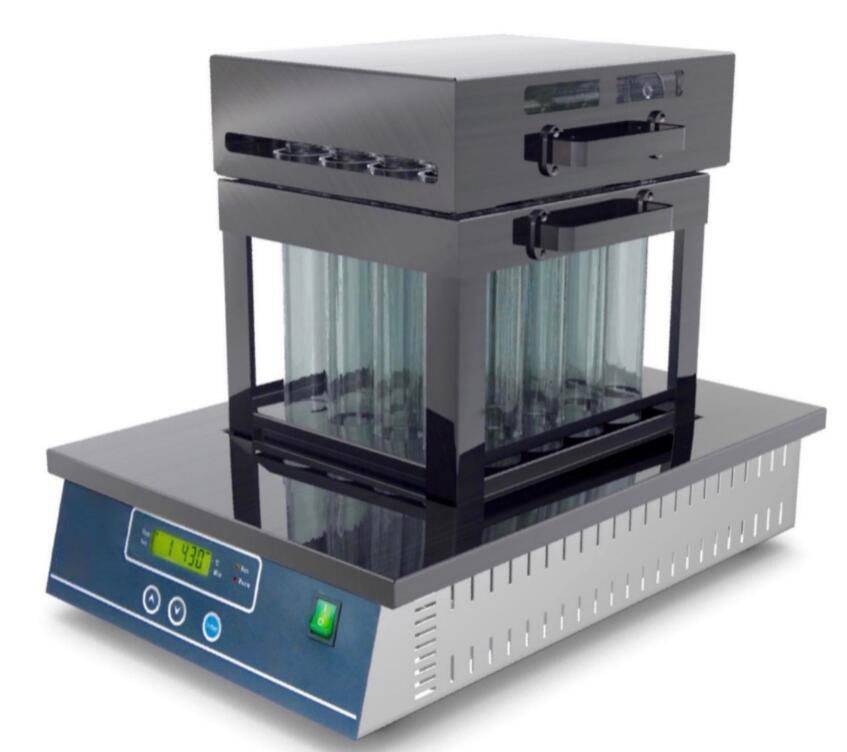
Una de las principales ventajas de utilizar un sistema de calentamiento eléctrico de tipo pozo es su precisión en el control de la temperatura. Esta precisión es crucial para mantener la integridad de las muestras y garantizar resultados reproducibles. El sistema de calentamiento eléctrico funciona aplicando directamente calor a la muestra, lo que minimiza la pérdida de energía y maximiza la eficacia del proceso de digestión. Este método de calentamiento directo contrasta con otras técnicas que pueden implicar un calentamiento indirecto, lo que puede dar lugar a una distribución desigual de la temperatura y comprometer potencialmente la calidad del análisis.
Además, el diseño tipo pozo del horno permite procesar varias muestras simultáneamente, lo que aumenta el rendimiento y reduce el tiempo necesario para la preparación de las muestras. Esta característica es especialmente beneficiosa en los laboratorios de alto rendimiento, donde la demanda de un análisis rápido y preciso de las muestras es primordial. Además, la gestión eficaz de las emisiones de gases nocivos es una característica de seguridad importante, ya que evita la liberación de humos tóxicos en el entorno del laboratorio, protegiendo así tanto al personal como al equipo.
En resumen, el horno de digestión, con su sistema de calentamiento eléctrico de tipo pozo, ofrece una solución robusta para acelerar la digestión de muestras al tiempo que garantiza la seguridad medioambiental y la eficiencia operativa. Su capacidad para manejar múltiples muestras simultáneamente y su preciso control de la temperatura lo convierten en una herramienta indispensable en los laboratorios analíticos modernos.
Otros equipos de preparación de muestras
Esparcidor de cola
El esparcidor de cola es un equipo especializado diseñado para aplicar con precisión y cubrir uniformemente líquidos de cola sobre diversos sustratos. Este proceso se consigue mediante la aplicación de fuerza centrífuga, que se controla meticulosamente ajustando la velocidad de rotación y la viscosidad de la solución de cola.
Aprovechando los principios de la fuerza centrífuga, el esparcidor de cola garantiza que la cola se distribuya uniformemente por la superficie del sustrato. La velocidad de rotación desempeña un papel crucial en este proceso, ya que influye directamente en el patrón de distribución y el grosor de la capa de cola. Las velocidades de rotación más altas suelen dar lugar a capas más finas y uniformemente distribuidas, mientras que las velocidades más bajas pueden dar lugar a recubrimientos más gruesos y menos uniformes.
La viscosidad de la solución de cola es otro factor crítico que el esparcidor de cola tiene en cuenta. Una cola más viscosa requerirá mayores velocidades de rotación para lograr el mismo nivel de uniformidad que una solución menos viscosa. Por el contrario, las colas menos viscosas pueden esparcirse eficazmente a velocidades más bajas, lo que hace que el proceso sea más eficiente y adaptable a diferentes tipos de colas y materiales de sustrato.
En resumen, la capacidad del esparcidor de cola para controlar tanto la velocidad de rotación como la viscosidad de la cola permite una aplicación precisa y uniforme de los líquidos de cola, lo que resulta esencial para garantizar la integridad y el rendimiento del producto final.
Máquinas de corte
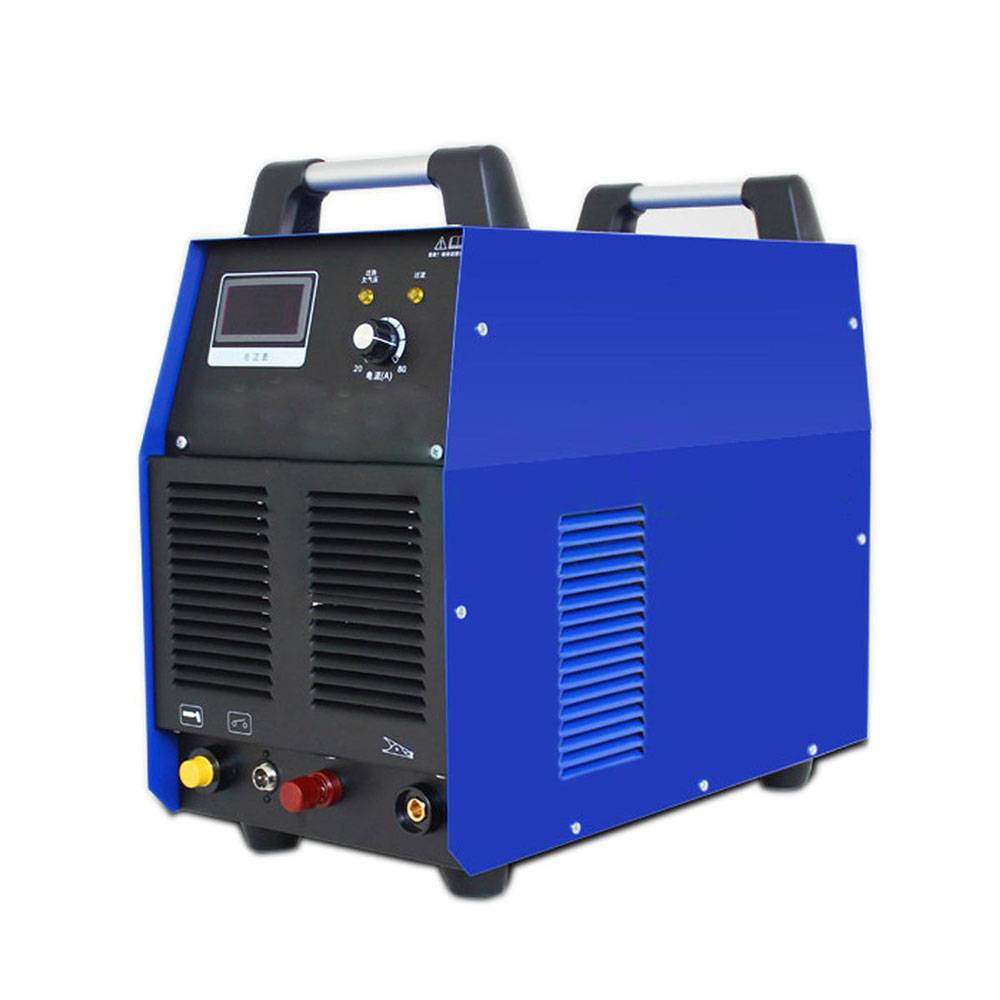
Las máquinas de corte son herramientas indispensables en la preparación de muestras de laboratorio, ya que ofrecen una variedad de métodos para cortar materiales con precisión. Estas máquinas incluyen:
- Máquinas de corte por llama: Utilizan una llama controlada para cortar materiales, ideales para muestras resistentes a altas temperaturas.
- Máquinas de corte por plasma: Utilizan gas ionizado para cortar materiales conductores de la electricidad con gran precisión.
- Máquinas de corte por láser: Utilizan rayos láser para cortes ultraprecisos, adecuados para geometrías de muestras delicadas e intrincadas.
- Máquinas de corte por agua: Utilizan chorros de agua a alta presión, a menudo mezclados con partículas abrasivas, para cortar materiales duros sin dañarlos con el calor.
Cada tipo de máquina de corte ofrece ventajas únicas en términos de eficacia y precisión de corte, y satisface las distintas necesidades de preparación de muestras en el laboratorio.
Máquina de fusión
La máquina de fusión es una herramienta indispensable en los laboratorios, diseñada específicamente para preparar muestras de vidrio para un análisis detallado. Este equipo emplea una variedad de métodos de calentamiento para alcanzar la temperatura necesaria para fundir el vidrio, garantizando que las muestras se encuentren en un estado consistente y analizable.
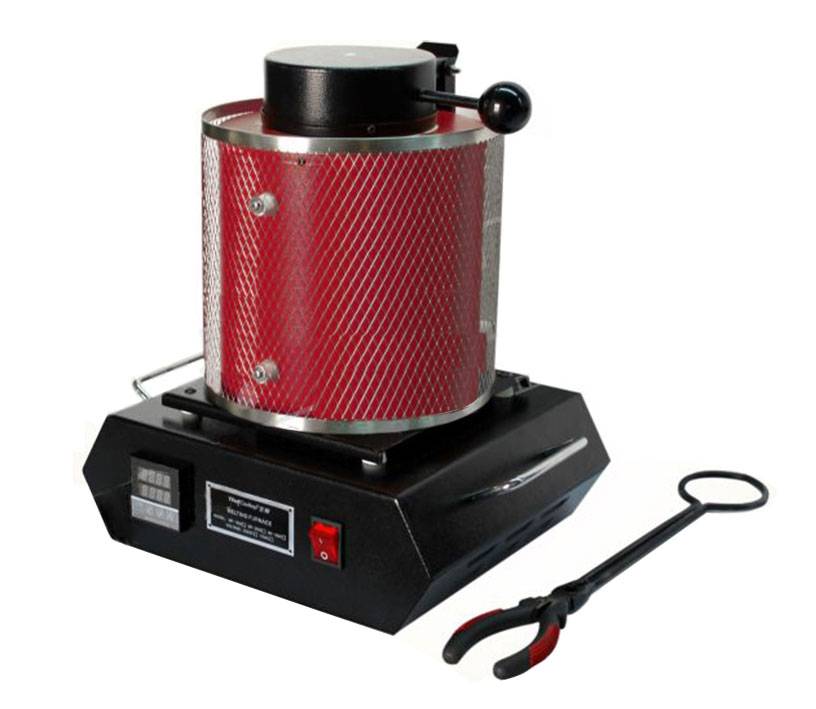
Uno de los principales métodos utilizados por las máquinas de fusión escalentamiento por gas. Esta técnica implica la combustión controlada de gases como el propano o el gas natural para generar calor. El gas suele introducirse a través de un sistema de quemadores que dirige la llama hacia la muestra, facilitando una fusión rápida y uniforme.
Otro método habitual es elcalentamiento por radiación de resistencia. En este proceso, la muestra se coloca dentro de una cámara donde se expone a una intensa radiación de elementos de alta resistencia. Estos elementos emiten calor en forma de radiación infrarroja, que penetra en la muestra de vidrio, provocando su fusión uniforme.
El calentamiento por inducción de alta frecuencia también es un método muy utilizado para fundir vidrio. Esta técnica utiliza campos electromagnéticos para inducir corrientes dentro de la muestra, que a su vez generan calor debido a la resistencia del vidrio a estas corrientes. La ventaja de este método es su capacidad para controlar con precisión la temperatura y la velocidad de calentamiento, garantizando que el vidrio se funda sin degradación ni contaminación.
Cada uno de estos métodos de calentamiento ofrece ventajas únicas en términos de control, eficacia y precisión, lo que convierte a la máquina de fusión en un equipo versátil y esencial en cualquier laboratorio centrado en el análisis del vidrio.
Prensa de pastillas
La prensa de comprimidos es una pieza de maquinaria esencial en la industria farmacéutica, diseñada para automatizar la producción de comprimidos mediante la compresión del polvo en formas y tamaños uniformes. Este proceso, conocido como compresión, se basa en la interacción de dos punzones y una matriz, denominados colectivamente estación. Los punzones superior e inferior colaboran para comprimir el polvo dentro de la matriz, dando lugar a la formulación de comprimidos.
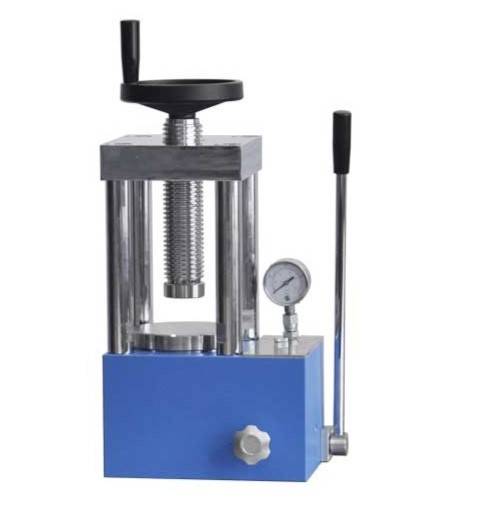
Las prensas de comprimidos son versátiles, capaces de fabricar comprimidos de diversos tamaños y formas para multitud de industrias, como cosmética, nutracéutica, medicina ayurvédica, suplementos de fitness, hierbas, confitería, pellets industriales, productos de limpieza e incluso aplicaciones mineras. La evolución de las comprimidoras se ha visto impulsada por la creciente demanda de comprimidos por parte de la población y las estrictas normativas, como las CGMP (Current Good Manufacturing Process), que garantizan la calidad y seguridad de los productos farmacéuticos.
Principio de funcionamiento
El funcionamiento de una comprimidora implica un proceso de dos pasos. En primer lugar, el punzón inferior desciende hasta la matriz, creando una cavidad que se llena de polvo. El polvo sobrante se raspa y el punzón superior desciende para comprimir el polvo. Se aplica una gran fuerza mediante rodillos de compresión, uniendo el material granulado y dándole forma de pastilla dura. Tras la compresión, el punzón inferior se eleva y expulsa la pastilla de la matriz. El mecanismo de presión hidráulica garantiza una distribución uniforme de la presión, con la posibilidad de ajustar la fuerza aplicada para diferentes formulaciones de comprimidos.
Características destacadas
Las prensas para comprimidos pequeños, en particular, cuentan con varias características dignas de mención:
- Modelo GMP compacto: Diseñada para cumplir las normas de buenas prácticas de fabricación.
- Sistemas motorizados y de volante manual: Ofrecen flexibilidad de funcionamiento.
- Revestimientos SS: Todas las piezas móviles están cubiertas de acero inoxidable para mayor seguridad.
- Estructura resistente: Construido a partir de material MS pintado para evitar vibraciones durante el funcionamiento.
- Tolva exterior: Facilita la alimentación de polvo.
- Piezas fácilmente desmontables: Todas las piezas de contacto pueden desmontarse rápidamente para una limpieza a fondo.
- Punzón cromado duro: Garantiza un funcionamiento sin óxido.
- Tamaño reducido: Hace que la máquina sea fácilmente movible y adaptable a diversas configuraciones de laboratorio.
Todas estas características garantizan que las prensas para comprimidos no sólo sean eficaces, sino que también cumplan las normas del sector, lo que las hace indispensables en la fabricación de productos farmacéuticos modernos.
Trituradora
Las trituradoras son herramientas esenciales en la preparación de muestras de laboratorio, diseñadas para reducir eficazmente las materias primas sólidas a los tamaños requeridos. A diferencia de los métodos tradicionales, que se basan en procesos de cribado, las trituradoras aprovechan el impacto a alta velocidad y la energía eólica para lograr esta reducción. Este enfoque innovador no sólo acelera el proceso, sino que también garantiza una distribución más uniforme del tamaño de las partículas, lo que es crucial para un análisis preciso.
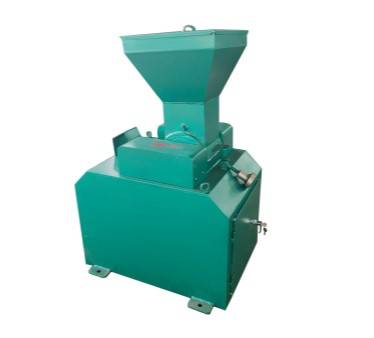
El funcionamiento de una trituradora implica someter las materias primas a intensas fuerzas mecánicas. Los mecanismos de impacto de alta velocidad, a menudo accionados por motores eléctricos, generan la energía necesaria para romper los materiales. Simultáneamente, la incorporación de energía eólica ayuda a la dispersión y posterior fragmentación de las partículas. Este método de doble acción minimiza la necesidad de un cribado posterior, agilizando el flujo de trabajo de preparación de muestras.
Además, la eliminación de los procesos de cribado tradicionales en las trituradoras aumenta la eficacia y precisión generales de las operaciones de laboratorio. Al reducir el tiempo y la mano de obra necesarios para la preparación de las muestras, las trituradoras contribuyen a agilizar los plazos de entrega y a obtener resultados analíticos más fiables. Esto las hace indispensables en entornos en los que el procesamiento rápido y preciso de las muestras es primordial, como en la investigación farmacéutica, los ensayos medioambientales y la ciencia de materiales.
Rectificadoras
Las esmeriladoras son herramientas esenciales en la preparación de muestras de laboratorio, diseñadas para lograr un esmerilado y pulido de alta precisión de diversas superficies de las piezas de trabajo. Estas máquinas utilizan herramientas abrasivas, como muelas o bandas abrasivas, para eliminar material de la superficie de la pieza de trabajo, lo que da como resultado un acabado más suave y preciso.
La función principal de una rectificadora es refinar la superficie de una pieza de trabajo, ya sea de metal, vidrio u otros materiales, para cumplir unos requisitos específicos de calidad dimensional y superficial. Este proceso es crucial en la preparación de muestras para su posterior análisis o para conseguir un aspecto pulido en los productos acabados.
Las rectificadoras funcionan mediante abrasión controlada, en la que las herramientas abrasivas interactúan con la pieza para eliminar pequeñas partículas de material. El nivel de precisión alcanzado depende de factores como el tipo de abrasivo utilizado, la presión aplicada y la velocidad de rotación de la herramienta de rectificado. Por ejemplo, los abrasivos más finos suelen utilizarse para pulir, mientras que los más gruesos se emplean para eliminar material de forma más agresiva.
En los laboratorios, las esmeriladoras se utilizan a menudo junto con otros equipos de preparación de muestras, como trituradoras y cortadoras, para crear un flujo de trabajo completo en la preparación de muestras para el análisis. Este enfoque integrado garantiza que cada paso del proceso de preparación de muestras esté optimizado para ofrecer precisión y eficacia.
La versatilidad de las máquinas trituradoras las hace indispensables en diversas industrias, como la metalúrgica, la electrónica y la farmacéutica. Son especialmente útiles en aplicaciones en las que el acabado superficial y la precisión dimensional son fundamentales, como en la producción de componentes de precisión o en la preparación de muestras para microscopía y espectroscopia.
En resumen, las rectificadoras desempeñan un papel fundamental en la preparación de muestras de laboratorio, ya que proporcionan los medios para lograr un rectificado y pulido de alta precisión, esenciales para garantizar la calidad y precisión de los procesos analíticos posteriores.
CONTÁCTANOS PARA UNA CONSULTA GRATUITA
Los productos y servicios de KINTEK LAB SOLUTION han sido reconocidos por clientes de todo el mundo. Nuestro personal estará encantado de ayudarle con cualquier consulta que pueda tener. ¡Contáctenos para una consulta gratuita y hable con un especialista del producto para encontrar la solución más adecuada para sus necesidades de aplicación!