El recocido total es un proceso de tratamiento térmico utilizado para ablandar metales, normalmente el acero, calentándolos por encima de la temperatura a la que se forma la austenita, seguido de un enfriamiento lento. Este proceso permite que la austenita se transforme en ferrita y perlita, lo que da como resultado un material de baja dureza y tensiones internas mínimas. La temperatura específica necesaria para el recocido completo depende del tipo de acero y de su composición, pero generalmente se produce a temperaturas superiores a la temperatura crítica superior (A3 para los aceros hipoeutectoides y Acm para los hipereutectoides). El proceso es largo y costoso, pero resulta esencial para conseguir las propiedades mecánicas deseadas en determinadas aplicaciones.
Explicación de los puntos clave:
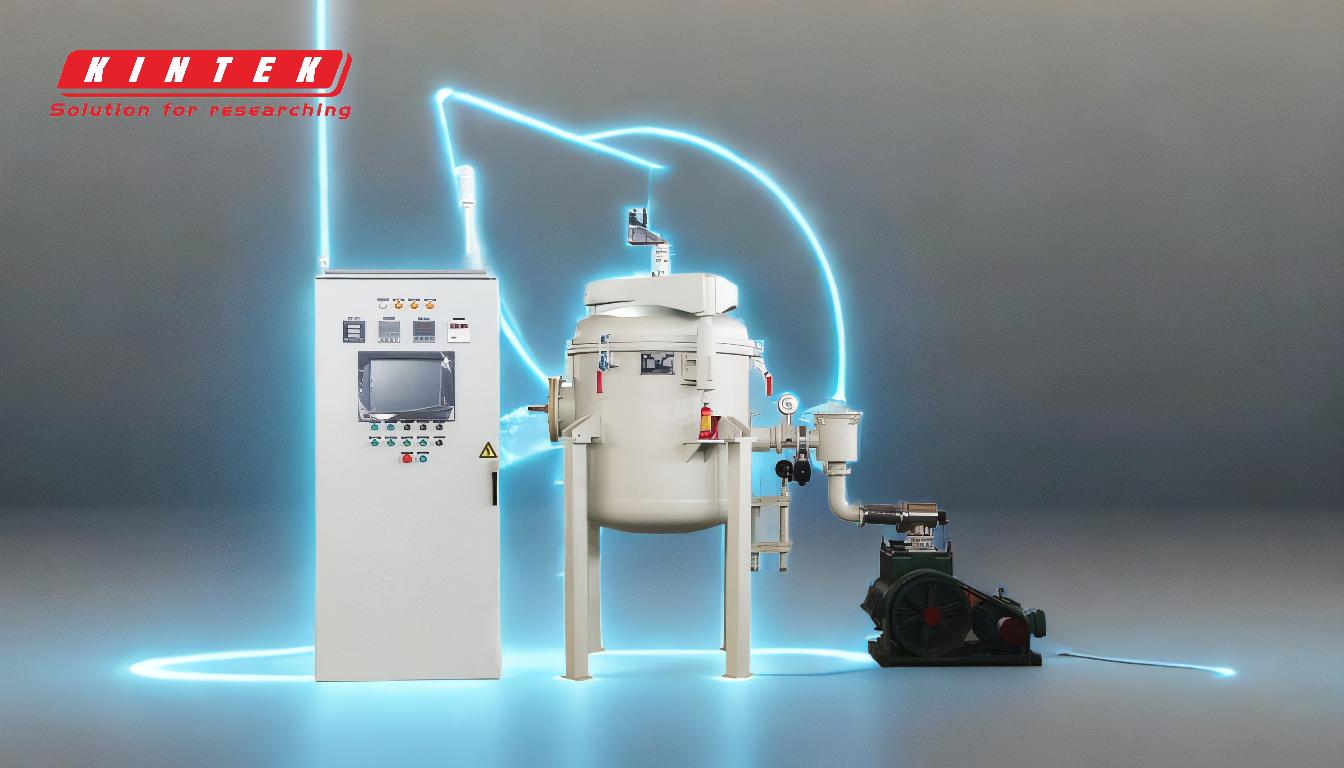
-
Definición de recocido completo:
- El recocido total es un proceso de tratamiento térmico diseñado para ablandar los metales, especialmente el acero, alterando su microestructura. Esto se consigue calentando el material por encima de la temperatura a la que se forma la austenita y dejándolo enfriar lentamente.
-
Gama de temperaturas para el recocido completo:
- La temperatura a la que se realiza el recocido completo depende del tipo de acero tratado. Para los aceros hipoeutectoides (aceros con menos del 0,8% de carbono), el proceso implica un calentamiento por encima de la temperatura crítica superior (A3), normalmente entre 700°C y 900°C. Para los aceros hipereutectoides (aceros con más del 0,8% de carbono), el proceso implica un calentamiento por encima de la línea Acm, que puede ser superior a 900°C.
-
Formación de austenita:
- La austenita es una fase cúbica centrada en la cara (FCC) del hierro que se forma cuando el acero se calienta por encima de su temperatura crítica. Esta fase es crucial para el proceso de recocido porque permite la redistribución del carbono y otros elementos de aleación dentro del metal.
-
Proceso de enfriamiento lento:
- Tras el calentamiento, el acero se enfría lentamente, normalmente en un horno, para permitir que la austenita se transforme en ferrita y perlita. Esta lenta velocidad de enfriamiento es esencial para conseguir la microestructura y las propiedades mecánicas deseadas, como baja dureza y tensiones internas mínimas.
-
Microestructura resultante:
- La microestructura final tras el recocido completo consiste en ferrita (una fase blanda y dúctil) y perlita (una estructura laminar de ferrita y cementita). Esta combinación proporciona un equilibrio entre resistencia y ductilidad, lo que facilita el mecanizado o conformado del material.
-
Aplicaciones y ventajas:
- El recocido total se utiliza habitualmente en industrias en las que es necesario ablandar los materiales para su posterior procesamiento, como el mecanizado, el trabajo en frío o el conformado. El proceso es especialmente beneficioso para reducir las tensiones internas y mejorar la mecanizabilidad del material.
-
Coste y plazos:
- El proceso de recocido completo es largo y costoso debido a la necesidad de un control preciso de la temperatura y a las lentas velocidades de enfriamiento. Sin embargo, las ventajas de conseguir una microestructura uniforme y reducir las tensiones internas suelen compensar estos inconvenientes en aplicaciones críticas.
-
Comparación con otros procesos de recocido:
- El recocido total es distinto de otros procesos de recocido, como el recocido de alivio de tensiones o el recocido de proceso, que se realizan a temperaturas más bajas y no implican la formación de austenita. El recocido completo proporciona una reducción más significativa de la dureza y las tensiones internas en comparación con estos otros métodos.
Al comprender estos puntos clave, un comprador de equipos o consumibles puede tomar decisiones informadas sobre los procesos de tratamiento térmico necesarios para sus aplicaciones específicas, garantizando que los materiales cumplan las propiedades mecánicas y los criterios de rendimiento deseados.
Cuadro recapitulativo:
Aspecto | Detalles |
---|---|
Definición | Proceso de tratamiento térmico para ablandar metales alterando su microestructura. |
Temperatura | 700°C-900°C para aceros hipoeutectoides; por encima de 900°C para aceros hipereutectoides. |
Fase clave | Formación de austenita durante el calentamiento. |
Proceso de enfriamiento | Enfriamiento lento para transformar la austenita en ferrita y perlita. |
**Microestructura resultante | Ferrita y perlita, que ofrecen baja dureza y tensiones internas mínimas. |
Aplicaciones | Se utiliza en las industrias de mecanizado, trabajo en frío y conformado. |
Coste y tiempo | Larga y costosa, pero esencial para aplicaciones críticas. |
Comparación | Más eficaz que el alivio de tensiones o el recocido de proceso para la reducción de la dureza. |
¿Necesita ayuda para elegir el proceso de tratamiento térmico adecuado? Contacte hoy mismo con nuestros expertos ¡!