La sinterización en estado sólido y la sinterización en fase líquida son dos procesos distintos utilizados en la densificación de cerámicas y otros materiales, que difieren principalmente en los mecanismos de unión de las partículas y en las temperaturas requeridas.La sinterización en estado sólido se basa en mecanismos de difusión para transportar el material y lograr la densificación, normalmente a temperaturas más altas, y es adecuada para materiales como la circonia y la alúmina.En cambio, la sinterización en fase líquida implica la introducción de una fase líquida de bajo punto de fusión, que facilita la reorganización y la unión de las partículas a temperaturas más bajas, lo que la hace ideal para materiales más difíciles de densificar, como el nitruro de silicio y el carburo de silicio.La presencia de la fase líquida acelera la densificación e influye en el cierre de poros, el tamaño de grano y las propiedades mecánicas.
Explicación de los puntos clave:
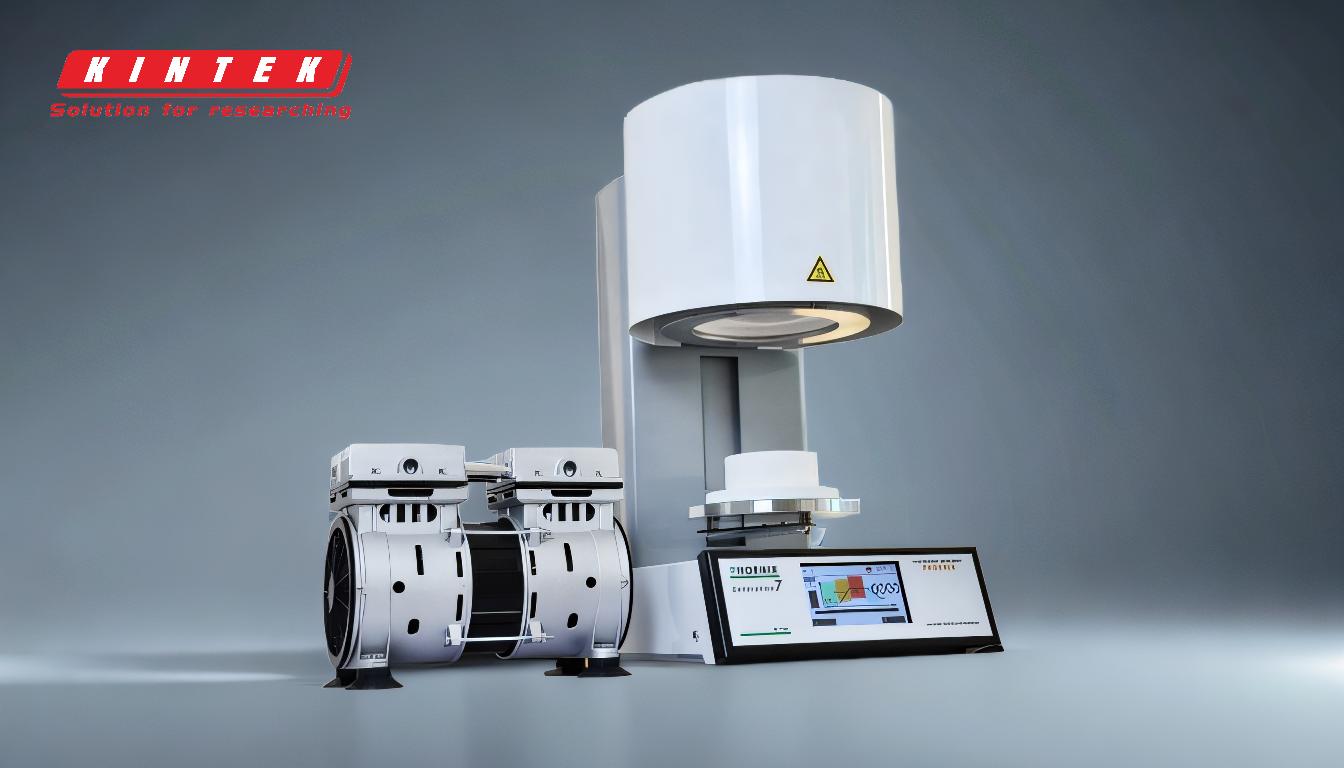
-
Temperatura de sinterización:
- Sinterización en estado sólido:Este proceso se produce a temperaturas relativamente altas, a menudo cercanas al punto de fusión del material primario.Por ejemplo, la zirconia y la alúmina se sinterizan a temperaturas en torno a los 1600°C.Las altas temperaturas son necesarias para activar los mecanismos de difusión, que son el principal medio de transporte y unión del material.
- Sinterización en fase líquida:Este método funciona a temperaturas más bajas que la sinterización en estado sólido.La adición de una fase líquida de bajo punto de fusión reduce la temperatura total de sinterización necesaria para la densificación.La fase líquida se forma a la temperatura de sinterización, lo que permite que las fuerzas capilares reorganicen las partículas con mayor eficacia.
-
Mecanismos de densificación:
- Sinterización en estado sólido:La densificación se consigue mediante la difusión en estado sólido.Los átomos se desplazan desde zonas de alto potencial químico (por ejemplo, las superficies de las partículas) a zonas de bajo potencial químico (por ejemplo, los cuellos entre partículas).Este proceso es más lento y requiere temperaturas más elevadas para superar las barreras de energía de activación de la difusión.
- Sinterización en fase líquida:La fase líquida mejora la densificación al proporcionar una vía de alta difusividad para los átomos.Las fuerzas capilares impulsan la reorganización de las partículas, y la fase líquida rellena los huecos entre las partículas, favoreciendo una unión y densificación más rápidas.Este proceso es especialmente eficaz en materiales difíciles de densificar mediante mecanismos de estado sólido.
-
Cierre de poros:
- Sinterización en estado sólido:El cierre de los poros en la sinterización en estado sólido es un proceso gradual que depende de la lenta difusión de los átomos.A medida que avanza la sinterización, los poros se encogen y acaban cerrándose, pero esto puede llevar mucho tiempo, especialmente a bajas temperaturas.Dependiendo de las condiciones de sinterización, la microestructura final puede seguir conteniendo cierta porosidad residual.
- Sinterización en fase líquida:La presencia de la fase líquida acelera el cierre de los poros.El líquido rellena los poros y los huecos entre las partículas, lo que acelera la densificación.La fase líquida también ayuda a redistribuir el material, reduciendo la porosidad global de forma más eficaz que en la sinterización en estado sólido.El resultado es un producto final más denso con menos poros residuales.
-
Tamaño de grano y microestructura:
- Sinterización en estado sólido:Este proceso puede dar lugar a un importante crecimiento del grano, especialmente a altas temperaturas.Los granos más grandes pueden afectar negativamente a las propiedades mecánicas, como la resistencia y la tenacidad.La microestructura suele caracterizarse por granos más grandes y uniformes.
- Sinterización en fase líquida:La sinterización en fase líquida tiende a producir tamaños de grano más pequeños debido a las temperaturas de sinterización más bajas y a la presencia de la fase líquida, que puede inhibir el crecimiento del grano.La microestructura resultante es más fina, lo que puede mejorar las propiedades mecánicas, como la resistencia a la flexión y la tenacidad a la fractura.Además, el modo de fractura puede pasar de transgranular (a través de los granos) a intergranular (a lo largo de los límites de los granos), lo que mejora aún más la tenacidad.
-
Idoneidad del material:
- Sinterización en estado sólido:Este método es adecuado para materiales que pueden densificarse mediante mecanismos de difusión, como la circonia y la alúmina.Estos materiales suelen tener puntos de fusión elevados y no requieren la adición de una fase líquida para la densificación.
- Sinterización en fase líquida:Este método es ideal para materiales difíciles de densificar mediante mecanismos de estado sólido, como el nitruro de silicio y el carburo de silicio.La adición de una fase líquida facilita la densificación a temperaturas más bajas y mejora la cinética general de sinterización.
-
Propiedades mecánicas:
- Sinterización en estado sólido:Las propiedades mecánicas de los materiales sinterizados mediante métodos de estado sólido suelen ser buenas, con una alta densidad y un excelente comportamiento a altas temperaturas.Sin embargo, el potencial de crecimiento de grano a altas temperaturas puede reducir la resistencia y la tenacidad.
- Sinterización en fase líquida:Los materiales sinterizados mediante métodos de fase líquida suelen presentar propiedades mecánicas mejoradas, como una mayor resistencia a la flexión y tenacidad a la fractura.El tamaño de grano más fino y el modo de fractura intergranular contribuyen a estas mejoras.Además, las temperaturas de sinterización más bajas pueden ayudar a preservar las propiedades intrínsecas del material.
En resumen, la elección entre la sinterización en estado sólido y en fase líquida depende de las propiedades del material, la microestructura deseada y el rendimiento mecánico.El sinterizado en estado sólido es adecuado para materiales que pueden densificarse por difusión, mientras que el sinterizado en fase líquida es ventajoso para materiales más difíciles de densificar, ya que ofrece temperaturas de sinterización más bajas, una densificación más rápida y mejores propiedades mecánicas.
Tabla resumen:
Aspecto | Sinterización en estado sólido | Sinterización en fase líquida |
---|---|---|
Temperatura | Altas temperaturas (por ejemplo, 1600°C para la circonia/alúmina) | Temperaturas más bajas debido a la presencia de una fase líquida de bajo punto de fusión |
Mecanismo de densificación | Se basa en la difusión en estado sólido, proceso más lento | La fase líquida mejora la difusión, reordenación y unión de partículas más rápida |
Cierre de poros | Gradual, depende de la difusión lenta; porosidad residual posible | Acelerado por fase líquida, menos poros residuales |
Tamaño del grano | Granos más grandes debido a las altas temperaturas | Granos más pequeños, microestructura más fina |
Idoneidad del material | Adecuado para óxido de circonio, alúmina y otros materiales favorables a la difusión | Ideal para nitruro de silicio, carburo de silicio y materiales más difíciles de densificar |
Propiedades mecánicas | Buena densidad y rendimiento a alta temperatura; el posible crecimiento de grano reduce la tenacidad | Mayor resistencia a la flexión, tenacidad a la fractura y microestructura más fina |
¿Necesita ayuda para elegir el método de sinterización adecuado para sus materiales? Póngase en contacto con nuestros expertos hoy mismo ¡!