El sinterizado por plasma de chispa (SPS) es una moderna técnica de sinterización que combina presión uniaxial y corriente continua pulsada (CC) para consolidar rápidamente polvos y convertirlos en materiales densos y homogéneos.El proceso se caracteriza por su rapidez, eficacia y capacidad para lograr una alta densificación a temperaturas más bajas en comparación con los métodos de sinterización convencionales.Las principales etapas del SPS incluyen la eliminación de gases y la creación de vacío, la aplicación de presión, el calentamiento por resistencia y el enfriamiento.Cada etapa desempeña un papel fundamental para garantizar el éxito de la densificación y la unión de las partículas de polvo.El proceso aprovecha la descarga de plasma, el calentamiento por joule y la deformación plástica para lograr un calentamiento rápido, la unión de las partículas y la consolidación del material.
Explicación de los puntos clave:
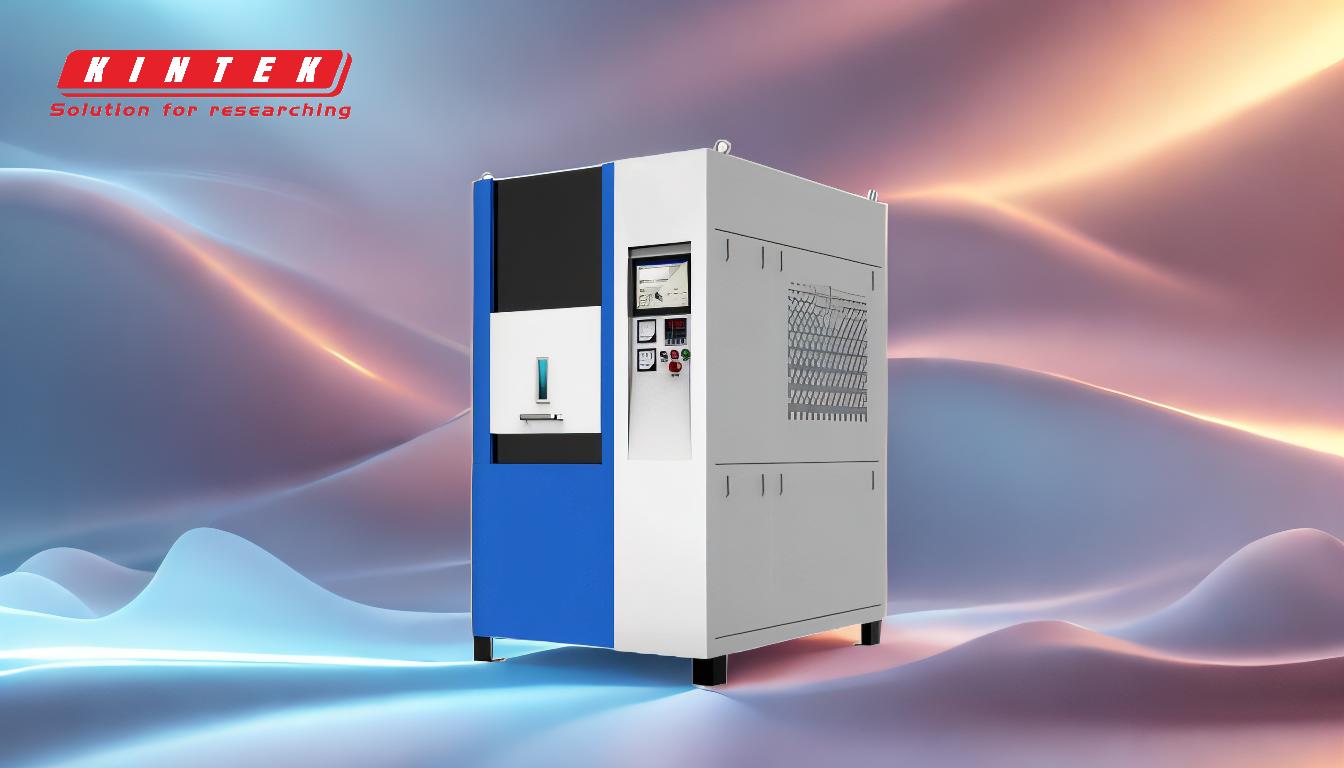
-
Eliminación de gases y creación de vacío
- El primer paso del SPS consiste en eliminar los gases de la cámara de sinterización y crear un vacío o una atmósfera controlada.
- Esto es crucial para evitar la oxidación y contaminación del material en polvo, garantizando la pureza y calidad del producto final.
- A entorno de vacío también facilita una mejor transferencia de calor y generación de plasma durante las etapas posteriores.
-
Aplicación de presión
- Se aplica presión uniaxial al material en polvo dentro de una matriz, normalmente de grafito .
- La presión ayuda a compactar las partículas de polvo, reduciendo los espacios entre ellas y favoreciendo un mejor contacto para la sinterización.
- La presión aplicada también ayuda a la deformación plástica de las partículas, que es esencial para lograr una alta densificación.
-
Calentamiento por resistencia
- Se hace pasar corriente continua pulsada a través de la matriz de grafito y, si es conductora, a través del propio material en polvo.
- Esto genera altas temperaturas localizadas y descargas de plasma entre las partículas, provocando un calentamiento rápido.
-
En el proceso intervienen tres mecanismos de calentamiento:
- Calentamiento por plasma:La descarga entre partículas crea plasma, lo que facilita la difusión y la unión en la superficie.
- Calentamiento Joule:La resistencia eléctrica dentro del material genera calor, lo que contribuye aún más a la sinterización.
- Deformación plástica:La combinación de calor y presión hace que las partículas se deformen y se unan en sus interfaces.
- Estos mecanismos permiten sinterizar a temperaturas mucho más bajas y en tiempos más cortos que con los métodos convencionales.
-
Etapa de enfriamiento
- Tras el proceso de sinterización, el material se enfría rápidamente hasta alcanzar la temperatura ambiente.
- El enfriamiento rápido ayuda a preservar la microestructura y las propiedades del material sinterizado.
- La velocidad de enfriamiento se controla para evitar tensiones térmicas o grietas en el producto final.
-
Ventajas del SPS
- Velocidad:SPS completa el proceso de sinterización en una fracción del tiempo requerido por los métodos convencionales.
- Temperaturas más bajas:SPS consigue la densificación a temperaturas varios cientos de grados inferiores a las del sinterizado tradicional.
- Propiedades mejoradas del material:Las rápidas velocidades de calentamiento y enfriamiento dan como resultado microestructuras más finas y propiedades mecánicas mejoradas.
- Versatilidad:Los SPS pueden utilizarse en una amplia gama de materiales, como cerámicas, metales y materiales compuestos.
-
Aplicaciones de la SPS
- La SPS se utiliza ampliamente en la fabricación de materiales avanzados, como cerámicas nanoestructuradas, materiales con gradientes funcionales y materiales compuestos.
- Es especialmente valioso en industrias que requieren materiales de alto rendimiento con un control preciso de la microestructura y las propiedades, como la aeroespacial, la automovilística y la electrónica.
Siguiendo estos pasos sinterización por plasma permite la producción de materiales densos de alta calidad con propiedades superiores, lo que lo convierte en la opción preferida para la fabricación de materiales avanzados.
Cuadro sinóptico:
Etapa | Detalles clave |
---|---|
Eliminación de gases y vacío | Elimina gases, evita la oxidación y garantiza una atmósfera controlada. |
Aplicación de presión | Compacta las partículas de polvo, reduce los huecos y ayuda a la deformación plástica. |
Calentamiento por resistencia | Utiliza CC pulsada para descarga de plasma, calentamiento por joule y unión rápida de partículas. |
Etapa de enfriamiento | El enfriamiento rápido preserva la microestructura y evita las tensiones térmicas. |
Ventajas | Velocidad, temperaturas más bajas, propiedades mejoradas y versatilidad de materiales. |
Aplicaciones | Aeroespacial, automoción, electrónica y fabricación de materiales avanzados. |
Descubra cómo el Spark Plasma Sintering puede revolucionar su proceso de fabricación de materiales. póngase en contacto con nosotros ¡!