La sinterización en un horno de inducción se refiere al proceso de compactación y unión de partículas de polvo en una masa sólida mediante la aplicación de calor, normalmente por debajo del punto de fusión del material.Este proceso es crucial para formar el revestimiento del horno, que debe soportar altas temperaturas y tensiones mecánicas durante su funcionamiento.El proceso de sinterización en un horno de inducción consta de tres etapas clave: cocción, semisinterización y sinterización completa.Cada etapa se controla cuidadosamente para garantizar que el revestimiento alcance una microestructura uniforme, duradera y de alto rendimiento.Los hornos de inducción, con su control preciso de la temperatura y su capacidad de calentamiento uniforme, son idóneos para los procesos de sinterización, garantizando la integridad y longevidad del revestimiento.
Explicación de los puntos clave:
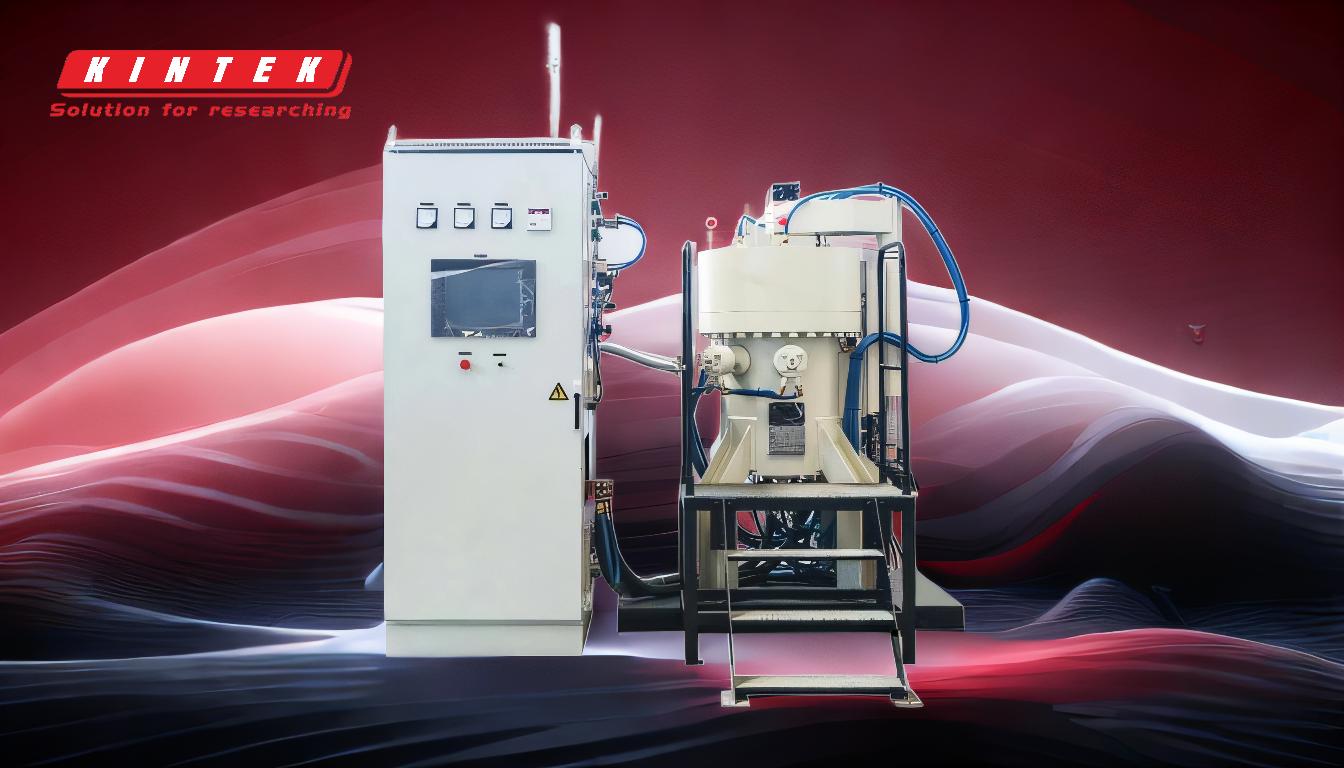
-
Definición de la sinterización en hornos de inducción:
- La sinterización es el proceso de compactación y unión de partículas de polvo en una masa sólida mediante calor, normalmente por debajo del punto de fusión del material.
- En los hornos de inducción, la sinterización se utiliza principalmente para formar el revestimiento refractario, que debe soportar altas temperaturas y tensiones mecánicas durante su funcionamiento.
-
Etapas del proceso de sinterización:
-
Etapa de cocción:
- El revestimiento del horno se calienta a unos 600°C a un ritmo controlado.
- En esta etapa se elimina la humedad del material refractario, lo que evita la aparición de grietas y garantiza la integridad estructural.
-
Etapa de semi-sinterización:
- Se aumenta la temperatura hasta 900°C y se mantiene durante un tiempo.
- Posteriormente, la temperatura se eleva a 1200°C a un ritmo más rápido y se mantiene de nuevo.
- Esta etapa inicia la unión de las partículas, formando una estructura semisólida.
-
Etapa de sinterización completa:
- La temperatura final se ajusta en función de las propiedades del material y las características deseadas del revestimiento.
- Esta etapa garantiza que el revestimiento logre una microestructura totalmente adherida, densa y duradera.
-
Etapa de cocción:
-
Importancia de la sinterización para revestimientos de hornos:
- Un revestimiento bien sinterizado tiene una estructura de tres capas que le confiere unas propiedades térmicas y mecánicas óptimas.
- Una sinterización adecuada mejora la resistencia del revestimiento a los choques térmicos, la erosión y las reacciones químicas con los metales fundidos.
- El proceso de sinterización influye directamente en la vida útil del revestimiento y en el rendimiento general del horno.
-
Papel de los hornos de inducción en la sinterización:
- Los hornos de inducción proporcionan un control preciso de la temperatura y un calentamiento uniforme, esenciales para obtener unos resultados de sinterización uniformes.
- El campo electromagnético de los hornos de inducción genera corrientes parásitas que garantizan una composición y una distribución de la temperatura uniformes en el material de revestimiento.
- Los hornos de inducción pueden alcanzar temperaturas de hasta 1650°C, adecuadas para sinterizar una amplia gama de materiales refractarios.
-
Ventajas de los hornos de inducción para sinterización:
- Calefacción uniforme:Garantiza una sinterización uniforme en todo el revestimiento, reduciendo el riesgo de puntos débiles.
- Eficiencia energética:Los hornos de inducción son altamente eficientes, con una potencia de salida efectiva superior al 95%.
- Automatización y control:Los avanzados sistemas de control permiten regular con precisión las velocidades de calentamiento, las temperaturas y los tiempos de mantenimiento.
- Durabilidad:Los hornos de inducción están diseñados para un funcionamiento continuo de 24 horas, lo que los hace ideales para procesos industriales de sinterización.
-
Parámetros clave del proceso:
- Control de temperatura:La regulación precisa de las velocidades de calentamiento y los tiempos de mantenimiento es fundamental para conseguir las propiedades de revestimiento deseadas.
- Composición del material:La composición química del material refractario, especialmente los elementos con alta afinidad por el oxígeno, debe gestionarse cuidadosamente.
- Propiedades físicas:Factores como el punto de fusión, la humectabilidad y la tensión superficial influyen en el proceso de sinterización.
- Pureza y fluidez:Garantizar la pureza y fluidez del material fundido durante la sinterización mejora el rendimiento del revestimiento.
-
Consideraciones prácticas para la sinterización en hornos de inducción:
- Diseño de hornos:El horno debe estar equipado con un inductor, una fuente de alimentación y un sistema de control de alta calidad para soportar el proceso de sinterización.
- Materiales de revestimiento:La elección de los materiales refractarios y su compatibilidad con el proceso de sinterización es crucial.
- Mantenimiento:La inspección y el mantenimiento periódicos del revestimiento del horno son necesarios para garantizar un rendimiento a largo plazo.
Al comprender estos puntos clave, los compradores de equipos y consumibles pueden tomar decisiones informadas sobre el proceso de sinterización en hornos de inducción, garantizando un rendimiento óptimo y la longevidad del revestimiento del horno.
Tabla resumen:
Aspecto | Detalles |
---|---|
Definición | Compactación y unión de partículas de polvo utilizando calor por debajo del punto de fusión. |
Etapas clave | Cocción (600°C), Semisinterización (900°C-1200°C), Sinterización completa. |
Importancia | Mejora la durabilidad del revestimiento, la resistencia al choque térmico y la vida útil del horno. |
Ventajas | Calentamiento uniforme, eficiencia energética, control preciso y durabilidad. |
Parámetros clave | Control de la temperatura, composición del material, propiedades físicas, pureza. |
Consideraciones prácticas | Diseño del horno, materiales de revestimiento y mantenimiento periódico. |
¿Está listo para optimizar su proceso de sinterización? Póngase en contacto con nuestros expertos para obtener soluciones a medida.