La temperatura de cocción de la alúmina, un parámetro clave en su procesamiento, suele rondar los 1350°C para conseguir estructuras de alta densidad y grano fino, como demuestra la referencia que afirma que los compactos de polvo de alúmina pura cocidos a esta temperatura durante 20 minutos alcanzan el 99% de la densidad teórica con un tamaño de grano de 1,2 μm.La alúmina, u óxido de aluminio (Al2O3), es un material cerámico versátil conocido por su resistencia a altas temperaturas, su resistencia mecánica y su estabilidad química, lo que lo hace adecuado para aplicaciones industriales exigentes.Aunque su punto de fusión ronda los 2.000 °C, la temperatura de cocción es inferior, ya que está optimizada para la sinterización y densificación durante el procesamiento.Esta temperatura garantiza la integridad estructural del material y las propiedades deseadas, como la resistencia al desgaste, la conductividad térmica y la resistencia a la corrosión, que son fundamentales para aplicaciones como crisoles, aislantes eléctricos y componentes de alta temperatura.
Explicación de los puntos clave:
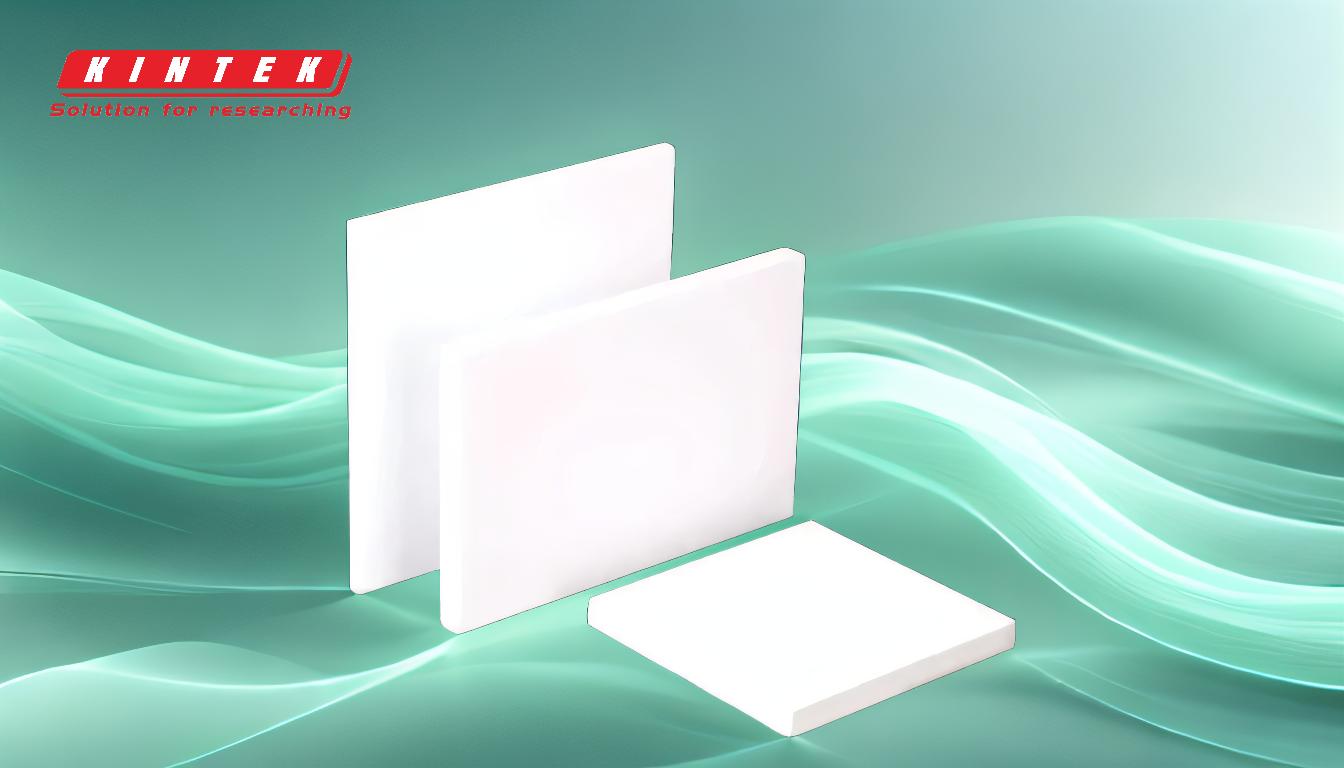
-
Temperatura de cocción de la alúmina:
- La temperatura de cocción de la alúmina suele ser 1350°C , como se demuestra en la referencia, donde los compactos de polvo de alúmina pura alcanzan el 99% de la densidad teórica y un tamaño de grano de 1,2 μm cuando se cuecen a esta temperatura durante 20 minutos.
- Esta temperatura es crucial para la sinterización, un proceso que densifica el material uniendo las partículas sin fundirlas por completo.
-
Propiedades de la alúmina a altas temperaturas:
- La alúmina es conocida por su estabilidad a altas temperaturas con un punto de fusión de aproximadamente 2000°C .Esto lo hace adecuado para aplicaciones que requieren resistencia al calor extremo.
- Su conductividad térmica (unos 3000 W/m-K) y su coeficiente de dilatación térmica le permiten soportar altas presiones internas y choques térmicos, por lo que es ideal para su uso en crisoles y otros entornos de alta temperatura.
-
Importancia de la temperatura de cocción en el procesamiento:
- La temperatura de cocción es inferior al punto de fusión para garantizar una sinterización y densificación adecuadas.A 1350 °C, la alúmina alcanza una densidad y una estructura de grano óptimas, que son fundamentales para sus propiedades mecánicas y térmicas.
- Un calentamiento excesivo o insuficiente durante la cocción puede provocar defectos como porosidad o densificación incompleta, comprometiendo el rendimiento del material.
-
Aplicaciones de la alúmina:
- La resistencia a altas temperaturas y la solidez mecánica de la alúmina la hacen adecuada para crisoles , aislantes eléctricos y componentes en hornos de alta temperatura .
- Su resistencia química y bioinercia también lo hacen ideal para su uso en entornos corrosivos y aplicaciones médicas.
-
Comparación con otros materiales:
- La alúmina es más dura que materiales como el hierro o el grafito, con una resistencia al desgaste y una conductividad térmica superiores.Esto la convierte en la opción preferida para aplicaciones industriales exigentes.
- Su elevado coeficiente de dilatación térmica le permite soportar las tensiones térmicas mejor que muchas otras cerámicas.
-
Origen natural y procesamiento:
- La alúmina se obtiene del óxido de aluminio, que constituye aproximadamente el 15% de la corteza terrestre.Se extrae de minerales naturales y se refina en materiales cerámicos mediante procesos como la sinterización a temperaturas controladas.
Al conocer la temperatura de cocción y su papel en el procesamiento de la alúmina, los fabricantes pueden optimizar las propiedades del material para aplicaciones específicas, garantizando su durabilidad y rendimiento en entornos corrosivos y de altas temperaturas.
Tabla resumen:
Aspecto clave | Detalles |
---|---|
Temperatura de cocción | 1350°C durante 20 minutos alcanza una densidad teórica del 99% y un tamaño de grano de 1,2 μm |
Punto de fusión | ~2000°C |
Propiedades principales | Estabilidad a altas temperaturas, resistencia al desgaste, conductividad térmica |
Aplicaciones | Crisoles, aislantes eléctricos, componentes de alta temperatura |
Importancia del procesamiento | Garantiza la sinterización, la densificación y la integridad estructural |
Optimice su procesamiento de alúmina contacte hoy mismo con nuestros expertos ¡!