La frecuencia de trabajo de un horno de inducción varía significativamente en función de la aplicación, el material a fundir, la capacidad del horno y la velocidad de fusión deseada.Suele oscilar entre la frecuencia de servicio (50 ó 60 Hz) y 400 kHz o más.Las frecuencias más altas se utilizan para volúmenes de fusión más pequeños debido al efecto de profundidad de piel, que garantiza una penetración poco profunda de la corriente alterna, mientras que las frecuencias más bajas son adecuadas para volúmenes más grandes y pueden inducir agitación o turbulencias en el metal.La elección de la frecuencia es fundamental para lograr un calentamiento eficaz, una distribución uniforme de la temperatura y un rendimiento óptimo de la fusión.
Explicación de los puntos clave:
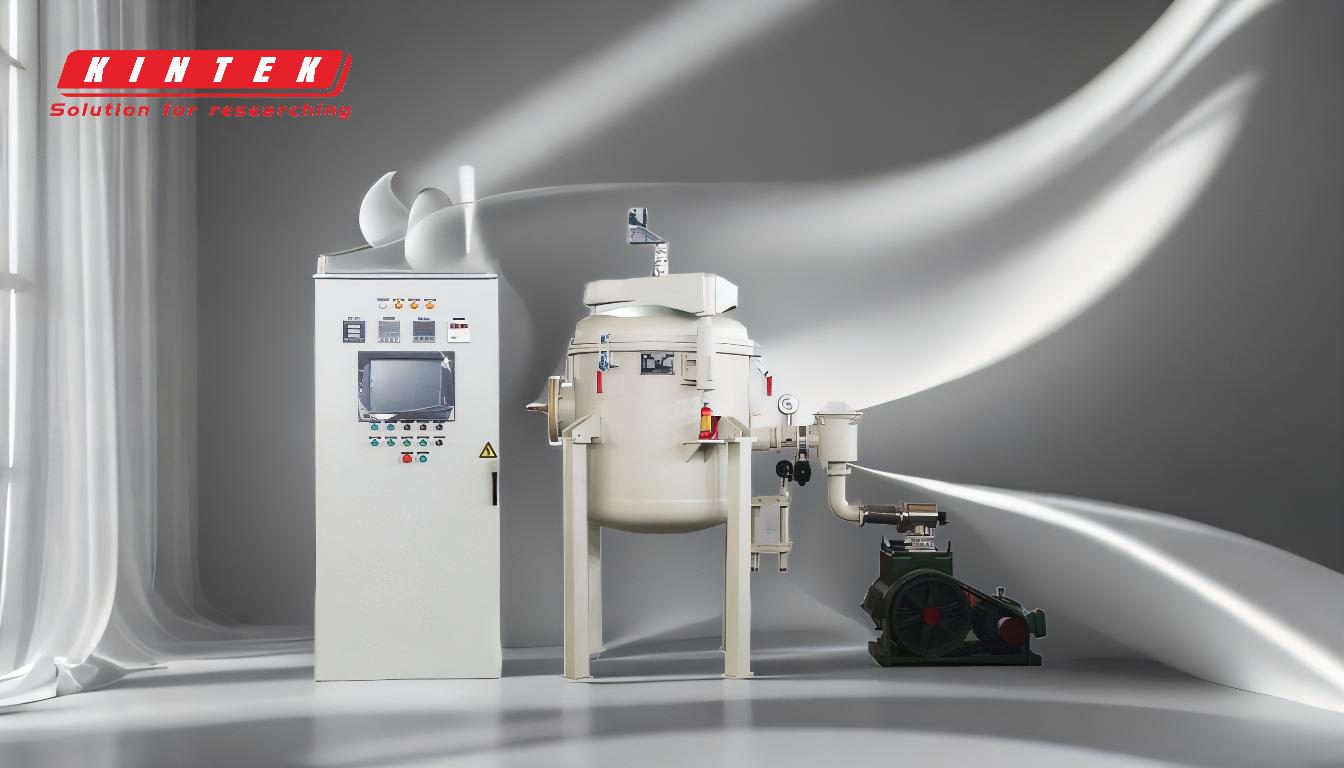
-
Gama de frecuencias de los hornos de inducción:
- Los hornos de inducción funcionan en una amplia gama de frecuencias, desde 50 ó 60 Hz (frecuencia de red) a 400 kHz o superior .
- La frecuencia específica elegida depende de factores como el material a fundir, la capacidad del horno y la velocidad de fusión requerida.
-
Papel de la frecuencia en la fusión:
- Frecuencias superiores:Se utiliza para pequeños volúmenes de fusión.Las frecuencias más altas dan lugar a una penetración menos profunda de la corriente alterna (efecto de profundidad de la piel), lo que resulta ideal para un calentamiento preciso y eficaz de pequeñas cantidades.
- Frecuencias más bajas:Adecuado para volúmenes mayores.Las frecuencias más bajas pueden generar agitación o turbulencia en el metal, garantizando una composición y distribución de la temperatura uniformes.
-
Efecto de profundidad de la piel:
- El efecto de profundidad de la piel se refiere a la profundidad a la que una corriente alterna puede penetrar en un conductor.
- Las frecuencias más altas conducen a penetración más superficial por lo que son ideales para fusiones más pequeñas y aplicaciones que requieren un calentamiento preciso.
- Las frecuencias más bajas permiten una penetración más profunda lo que es beneficioso para fusiones más grandes y procesos que requieren agitación o turbulencia.
-
Factores que influyen en la selección de la frecuencia:
- Material que se funde:Los distintos materiales tienen propiedades eléctricas y térmicas diferentes, lo que influye en la elección de la frecuencia.
- Capacidad del horno:Los hornos más pequeños suelen utilizar frecuencias más altas, mientras que los hornos más grandes funcionan con frecuencias más bajas.
- Velocidad de fusión:Las frecuencias más altas permiten un calentamiento y una fusión más rápidos, lo que resulta ventajoso para operaciones a pequeña escala o de alta velocidad.
-
Aplicaciones de las distintas frecuencias:
- Frecuencia de red (50 ó 60 Hz):Comúnmente utilizadas para procesos de fusión industrial a gran escala, como la producción de acero o hierro.
- Frecuencias medias (1-10 kHz):Ideal para hornos de tamaño medio y aplicaciones que requieran un equilibrio entre profundidad de penetración y eficacia de calentamiento.
- Altas frecuencias (10-400 kHz o superior):Se utiliza para la fusión a pequeña escala, el calentamiento de precisión y las aplicaciones que requieren cambios rápidos de temperatura.
-
Ventajas del funcionamiento a frecuencia variable:
- Flexibilidad:La fuente de alimentación de un horno de inducción puede ajustarse para trabajar a diferentes frecuencias, lo que le permite manipular diversos materiales y tamaños de masa fundida.
- Eficiencia:La selección adecuada de la frecuencia garantiza un uso óptimo de la energía, reduciendo el consumo eléctrico y los costes operativos.
- Calentamiento uniforme:La capacidad de controlar la frecuencia ayuda a conseguir una distribución y composición uniformes de la temperatura en el material fundido.
-
Consideraciones técnicas:
- Fuente de alimentación:Los hornos de inducción utilizan sistemas de conversión de frecuencia y regulación de potencia IGBT de estado sólido, lo que permite un funcionamiento suave y estable en una amplia gama de frecuencias.
- Sistemas de protección:Las completas funciones de protección, como la protección contra sobrecorriente, sobretensión y sobrecalentamiento, garantizan un funcionamiento seguro y fiable en todas las frecuencias.
- Sistemas de control:Los avanzados sistemas de control permiten la exploración y el ajuste automáticos de frecuencias, lo que garantiza un rendimiento óptimo para las distintas aplicaciones.
-
Implicaciones prácticas para los compradores:
- Requisitos específicos de los materiales:Al seleccionar un horno de inducción, tenga en cuenta los materiales que pretende fundir y sus requisitos específicos de frecuencia.
- Capacidad del horno:Elija un horno con una gama de frecuencias que se adapte a sus necesidades de producción, ya sea para trabajos de precisión a pequeña escala o para fusión industrial a gran escala.
- Eficiencia energética:Opte por un horno con regulación de frecuencia y potencia ajustables para maximizar la eficiencia energética y reducir los costes operativos.
- Mantenimiento y funcionamiento:Asegúrese de que el horno dispone de controles fáciles de usar y sistemas de protección completos para facilitar el mantenimiento y garantizar un funcionamiento fiable.
Al comprender la relación entre la frecuencia, las propiedades del material y la capacidad del horno, los compradores pueden tomar decisiones informadas para seleccionar el horno de inducción más adecuado para sus necesidades específicas.
Tabla resumen:
Gama de frecuencias | Aplicaciones | Principales ventajas |
---|---|---|
50-60 Hz | Fusión industrial a gran escala (acero, hierro) | Penetración profunda, efecto de agitación |
1-10 kHz | Hornos de tamaño medio | Penetración y eficacia equilibradas |
10-400 kHz | Calentamiento de precisión a pequeña escala | Penetración superficial, calentamiento rápido |
¿Necesita ayuda para seleccionar la frecuencia de horno de inducción adecuada para su aplicación? Póngase en contacto con nuestros expertos para recibir asesoramiento personalizado.