La sinterización es un proceso crítico en la ciencia de los materiales, en el que los materiales en polvo se compactan y se calientan para formar una estructura sólida.La calidad y las propiedades del producto sinterizado dependen de varios factores clave, como la temperatura, el tiempo de sinterización, la presión, la atmósfera, el tamaño de las partículas y la composición.Cada uno de estos factores desempeña un papel importante en la determinación de la cinética de sinterización, la densificación y las propiedades finales del material.Por ejemplo, las temperaturas más altas pueden mejorar la resistencia a la tracción y la energía de impacto, mientras que los tamaños de partícula más pequeños y las composiciones homogéneas favorecen una mejor densificación.Además, la atmósfera de sinterización, ya sea aire, vacío o gases inertes, puede afectar significativamente al resultado.Comprender estos factores es esencial para optimizar el proceso de sinterización y conseguir las propiedades deseadas del material.
Explicación de los puntos clave:
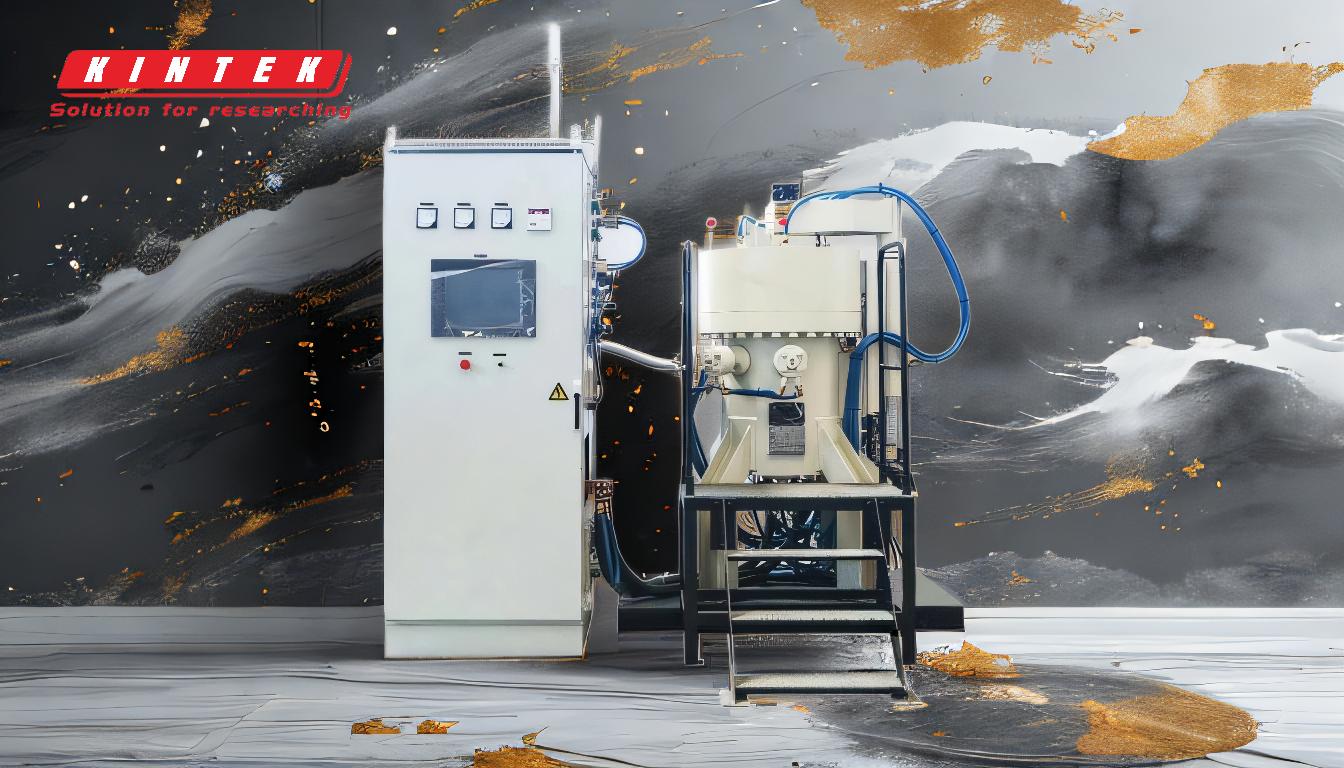
-
Temperatura:
- Papel en la sinterización:La temperatura es uno de los factores más críticos en la sinterización.Influye directamente en la cinética de sinterización, que rige la velocidad a la que las partículas se unen y densifican.En general, las temperaturas más altas aumentan la movilidad de los átomos, lo que provoca una difusión más rápida y una mejor unión de las partículas.
- Impacto en las propiedades de los materiales:Las temperaturas elevadas pueden mejorar las propiedades mecánicas del producto sinterizado, como la resistencia a la tracción, la resistencia a la fatiga por flexión y la energía de impacto.Sin embargo, las temperaturas excesivamente altas pueden provocar un crecimiento de grano indeseable o transformaciones de fase, que pueden degradar las propiedades del material.
-
Tiempo de sinterización:
- Efecto sobre la densificación:La duración del proceso de sinterización afecta al grado de densificación.Los tiempos de sinterización más largos permiten una unión más completa de las partículas y la eliminación de los poros, lo que da lugar a una mayor densidad y mejores propiedades mecánicas.
- Contrapartidas:Aunque los tiempos de sinterización más largos pueden mejorar la densificación, también aumentan el riesgo de crecimiento de granos y pueden provocar ineficiencia energética.Por lo tanto, el tiempo de sinterización debe optimizarse para equilibrar la densificación y el consumo de energía.
-
Presión:
- Papel en la reorganización de partículas:La presión aplicada durante la sinterización ayuda a la reordenación de las partículas, reduciendo la porosidad y mejorando la densificación.La presión también puede facilitar la eliminación de huecos y mejorar la uniformidad del producto sinterizado.
- Impacto en las propiedades finales:Las presiones más elevadas conducen generalmente a una mejor densificación y a una mejora de las propiedades mecánicas.Sin embargo, la aplicación de presión debe controlarse cuidadosamente para evitar la deformación o el agrietamiento del material.
-
Atmósfera:
- Tipos de atmósferas:La atmósfera de sinterización puede ser aire, vacío o gases inertes como el argón o el nitrógeno.Cada atmósfera tiene efectos diferentes en el proceso de sinterización.
- Influencia en la sinterización:La elección de la atmósfera puede afectar a la oxidación, reducción o contaminación del material.Por ejemplo, una atmósfera de vacío o inerte puede evitar la oxidación, lo que es crucial para los materiales sensibles al oxígeno.La atmósfera también influye en la conductividad térmica y la transferencia de calor durante la sinterización.
-
Tamaño de las partículas:
- Efecto sobre el comportamiento de sinterización:Las partículas de menor tamaño tienen una mayor relación superficie/volumen, lo que favorece una difusión más rápida y una mejor densificación.Las partículas más pequeñas también tienden a sinterizarse a temperaturas más bajas en comparación con las partículas más grandes.
- Impacto en las propiedades finales:Los polvos más finos suelen tener una microestructura más homogénea y mejores propiedades mecánicas.Sin embargo, las partículas muy finas pueden ser difíciles de manipular y requerir técnicas especiales de procesamiento.
-
Composición:
- Papel en la sinterización:La composición química de la mezcla de polvo afecta al comportamiento de sinterización.Las composiciones homogéneas tienden a sinterizarse más uniformemente, lo que conduce a una mejor densificación y a menos defectos.
- Impacto en las propiedades del material:La composición determina la fase final y la microestructura del producto sinterizado.Pueden utilizarse elementos de aleación o aditivos para adaptar las propiedades del material sinterizado, como la dureza, la tenacidad o la conductividad térmica.
-
Velocidad de calentamiento:
- Efecto sobre la densificación:La velocidad a la que se calienta el material puede influir en el proceso de sinterización.Una velocidad de calentamiento más lenta permite una distribución más uniforme del calor y puede reducir las tensiones térmicas, lo que conduce a una mejor densificación.
- Impacto en la microestructura:Las velocidades de calentamiento rápidas pueden provocar una sinterización desigual y causar defectos como grietas o huecos.Por lo tanto, la velocidad de calentamiento debe controlarse cuidadosamente para conseguir la microestructura y las propiedades deseadas.
-
Velocidad de enfriamiento:
- Efecto sobre las propiedades finales:La velocidad de enfriamiento del producto sinterizado puede afectar a la microestructura y las propiedades finales.Un enfriamiento lento puede provocar crecimiento de grano y transformaciones de fase, mientras que un enfriamiento rápido puede dar lugar a una microestructura más fina y mejores propiedades mecánicas.
- Contrapartidas:La velocidad de enfriamiento debe optimizarse para equilibrar la microestructura y las propiedades deseadas.El enfriamiento rápido puede ser beneficioso para determinados materiales, pero también puede introducir tensiones residuales.
-
Espesor de capa y velocidad de la máquina:
- Papel en la sinterización industrial:En los procesos industriales de sinterización, factores como el grosor de la capa y la velocidad de la máquina se controlan para garantizar una calidad constante.El grosor de la capa afecta a la distribución del calor y a la cinética de sinterización, mientras que la velocidad de la máquina determina el tiempo de sinterización y el punto final.
- Impacto en la calidad de la sinterización:El control adecuado de estos parámetros es esencial para lograr una sinterización uniforme y evitar defectos.Por ejemplo, un espesor de capa de 250-500 mm y una velocidad de máquina de 1,5-4 m/min son valores típicos utilizados en los procesos industriales de sinterización.
-
Atmósfera gaseosa y vacío:
- Influencia en la sinterización:La atmósfera gaseosa y el nivel de vacío pueden afectar significativamente al proceso de sinterización.Una atmósfera de vacío o inerte puede evitar la oxidación y la contaminación, mientras que una atmósfera gaseosa controlada puede utilizarse para conseguir reacciones específicas o transformaciones de fase.
- Impacto en las propiedades de los materiales:La elección de la atmósfera puede influir en las propiedades finales del producto sinterizado, como la densidad, la porosidad y la resistencia mecánica.Por lo tanto, la atmósfera debe seleccionarse cuidadosamente en función del material y de las propiedades deseadas.
En resumen, el proceso de sinterización está influido por una compleja interacción de factores, cada uno de los cuales debe controlarse cuidadosamente para conseguir las propiedades deseadas del material.Comprender estos factores y sus interacciones es esencial para optimizar el proceso de sinterización y obtener productos sinterizados de alta calidad.
Tabla resumen:
Factor | Papel en la sinterización | Impacto en las propiedades del material |
---|---|---|
Temperatura | Regula la cinética de sinterización; las temperaturas más altas mejoran la difusión y la adhesión. | Mejora la resistencia a la tracción, la resistencia a la fatiga por flexión y la energía de impacto. |
Tiempo de sinterización | Los tiempos más largos mejoran la densificación pero corren el riesgo de crecimiento del grano. | Mejora la densidad y las propiedades mecánicas; contrapartida con la eficiencia energética. |
Presión | Facilita la reorganización de las partículas y la reducción de la porosidad. | Las presiones más altas conducen a una mejor densificación y uniformidad. |
Atmósfera | El aire, el vacío o los gases inertes afectan a la oxidación, la reducción y la contaminación. | Evita la oxidación; influye en la conductividad térmica y la integridad del material. |
Tamaño de las partículas | Las partículas más pequeñas sinterizan más rápido y a temperaturas más bajas; una mayor superficie mejora la adhesión. | Los polvos más finos producen microestructuras homogéneas y mejores propiedades mecánicas. |
Composición | Las mezclas homogéneas sinterizan uniformemente; los aditivos adaptan las propiedades. | Determina la fase final, la microestructura y propiedades como la dureza y la tenacidad. |
Velocidad de calentamiento | Las velocidades más lentas garantizan una distribución uniforme del calor y reducen el estrés térmico. | El calentamiento rápido puede causar defectos; los ritmos controlados mejoran la densificación. |
Velocidad de enfriamiento | Afecta a la microestructura; el enfriamiento lento puede provocar crecimiento de grano, mientras que el enfriamiento rápido lo refina. | El enfriamiento rápido mejora las propiedades mecánicas pero puede introducir tensiones residuales. |
Espesor de capa | Influye en la distribución del calor y la cinética de sinterización en los procesos industriales. | Un control adecuado garantiza una sinterización uniforme y evita defectos. |
Atmósfera gaseosa | El vacío o los gases inertes evitan la oxidación; las atmósferas controladas permiten reacciones específicas. | Influye en la densidad, porosidad y resistencia mecánica del producto sinterizado. |
¿Está listo para optimizar su proceso de sinterización? Póngase en contacto con nuestros expertos para obtener soluciones a medida.