El Spark Plasma Sintering (SPS) es una moderna técnica de sinterización que combina los principios del prensado en caliente con la aplicación de corrientes eléctricas pulsadas.Este método permite calentar y consolidar rápidamente los materiales, lo que se traduce en tiempos de procesamiento más cortos y en la posibilidad de crear materiales con microestructuras y propiedades únicas.La clave de su eficacia reside en el flujo directo de corriente eléctrica a través de la matriz de grafito y el material que se procesa, lo que genera un calentamiento localizado y facilita la densificación.Además, el "efecto plasma de chispa" desempeña un papel fundamental en la inhibición del crecimiento de partículas, lo que permite la producción de materiales de grano fino y alto rendimiento.
Explicación de los puntos clave:
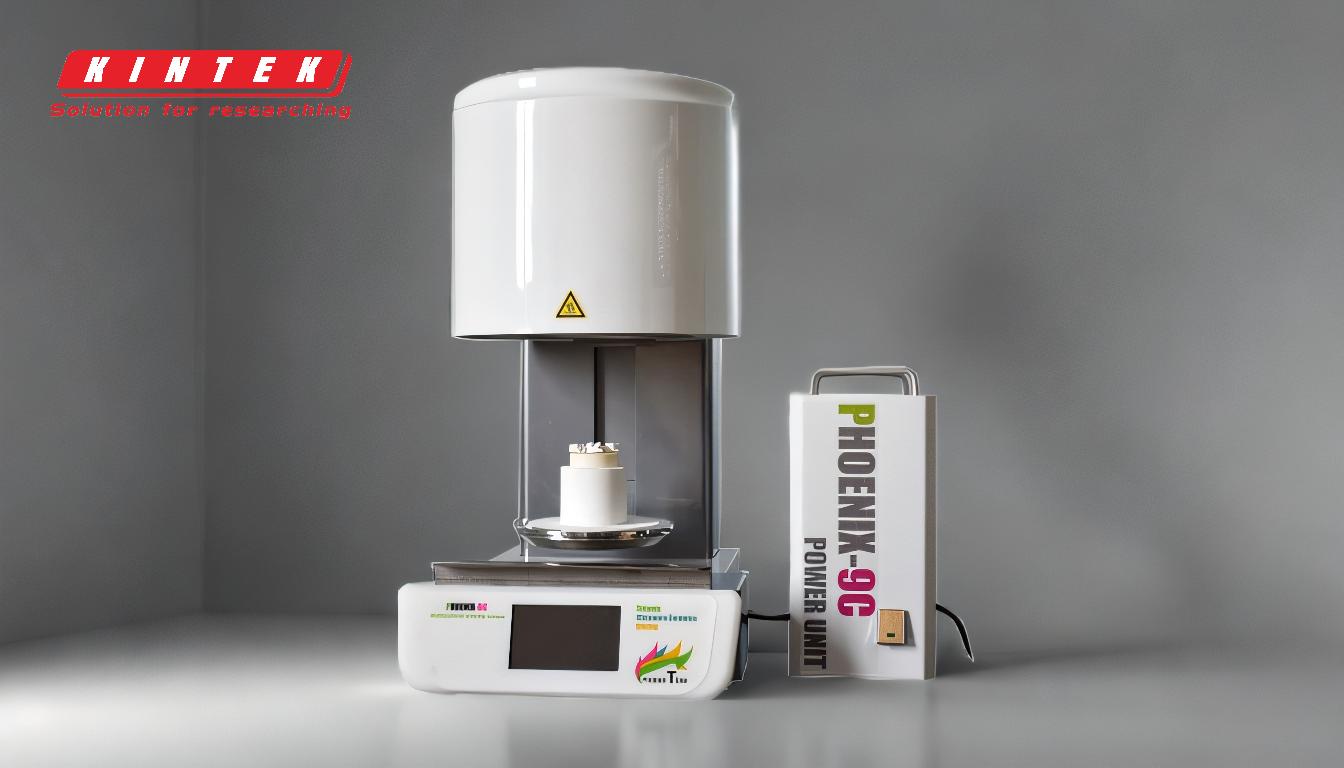
-
Configuración de prensado en caliente modificada:
- El SPS se basa en el método tradicional de prensado en caliente, pero introduce importantes modificaciones.En el prensado en caliente convencional, el calor se aplica externamente a la matriz, que a su vez lo transfiere al material.En el SPS, la corriente eléctrica fluye directamente a través de la matriz de grafito y el material, lo que permite un calentamiento más rápido y eficaz.
- Este mecanismo de calentamiento directo reduce la pérdida de energía y permite un control preciso de la temperatura, lo que es crucial para conseguir las propiedades deseadas del material.
-
Corrientes eléctricas pulsadas:
- El uso de corrientes eléctricas pulsadas es una característica definitoria del SPS.Estas corrientes generan un calentamiento rápido y localizado, lo que reduce significativamente el tiempo necesario para la sinterización en comparación con los métodos convencionales.
- La naturaleza pulsante de la corriente también ayuda a mantener una distribución uniforme de la temperatura dentro del material, minimizando los gradientes térmicos que podrían provocar defectos.
-
Efecto de chispa de plasma:
- El "efecto de chispa de plasma" es un fenómeno exclusivo del SPS, en el que la corriente eléctrica induce la formación de plasma entre las partículas.Este plasma facilita la eliminación de óxidos superficiales y contaminantes, favoreciendo una mejor unión de las partículas.
- El efecto del plasma de chispa también inhibe el crecimiento de partículas durante la sinterización, lo que es esencial para producir materiales con microestructuras de grano fino.Los materiales de grano fino suelen presentar propiedades mecánicas, térmicas y eléctricas superiores.
-
Calentamiento rápido y ciclos de proceso cortos:
- Una de las ventajas más significativas del SPS es su capacidad para alcanzar velocidades de calentamiento muy rápidas, llegando a menudo a temperaturas del orden de 1000-2000°C en sólo unos minutos.Este calentamiento rápido minimiza el tiempo que el material pasa a altas temperaturas, reduciendo el riesgo de transformaciones de fase no deseadas o de crecimiento de grano.
- Los ciclos de proceso cortos no sólo mejoran la eficiencia, sino que también hacen que el SPS sea adecuado para procesar materiales sensibles a la temperatura que se degradarían bajo una exposición prolongada a altas temperaturas.
-
Creación de composiciones y propiedades de materiales únicas:
- El SPS permite sinterizar materiales difíciles o imposibles de procesar con métodos convencionales.Esto incluye materiales con altos puntos de fusión, nanomateriales y materiales compuestos.
- El mecanismo de calentamiento único y el efecto de plasma de chispa permiten crear materiales con microestructuras a medida, como materiales nanocristalinos o gradientes, que pueden presentar propiedades mejoradas como mayor resistencia, resistencia al desgaste o conductividad térmica.
-
La matriz de grafito como componente clave:
- La matriz de grafito utilizada en el SPS cumple múltiples funciones.Actúa como molde para el material que se sinteriza, conduce la corriente eléctrica y proporciona aislamiento térmico.El grafito se elige por su alta conductividad eléctrica, estabilidad térmica y resistencia al choque térmico.
- El diseño de la matriz es fundamental para garantizar una distribución uniforme de la corriente y el control de la temperatura, que son esenciales para conseguir propiedades constantes del material.
-
Aplicaciones y ventajas:
- El SPS se utiliza ampliamente en la producción de cerámicas avanzadas, metales, materiales compuestos y materiales de gradación funcional.Su capacidad para producir materiales densos y de grano fino con defectos mínimos lo hace ideal para aplicaciones en las industrias aeroespacial, automovilística, electrónica y biomédica.
- El proceso también es respetuoso con el medio ambiente, ya que consume menos energía y produce menos emisiones en comparación con los métodos tradicionales de sinterización.
Al combinar los principios del prensado en caliente con innovadores efectos eléctricos y de plasma, el SPS ofrece una poderosa herramienta para que los científicos e ingenieros de materiales creen materiales avanzados con propiedades a medida y mayor rendimiento.
Tabla resumen:
Aspecto clave | Descripción |
---|---|
Prensado en caliente modificado | El flujo directo de corriente eléctrica permite un calentamiento más rápido y eficaz. |
Corrientes eléctricas pulsadas | El calentamiento rápido y localizado reduce el tiempo de sinterización y garantiza una temperatura uniforme. |
Efecto de chispa de plasma | Inhibe el crecimiento de partículas, produciendo materiales de grano fino y alto rendimiento. |
Calentamiento rápido | Alcanza 1000-2000°C en minutos, ideal para materiales sensibles a la temperatura. |
Creación única de materiales | Permite la sinterización de materiales de alto punto de fusión, compuestos y nanomateriales. |
Matriz de grafito | Conduce la corriente, proporciona aislamiento y garantiza un control uniforme de la temperatura. |
Aplicaciones | Las industrias aeroespacial, automovilística, electrónica y biomédica se benefician del SPS. |
Ventajas | Eficiente energéticamente, respetuoso con el medio ambiente y produce defectos mínimos. |
Descubra el potencial del Spark Plasma Sintering para sus necesidades de material. contacte hoy con nuestros expertos ¡!