La sinterización en pulvimetalurgia es un proceso crítico de tratamiento térmico que transforma los polvos metálicos en componentes sólidos y duraderos.Consiste en calentar el polvo metálico compactado a una temperatura justo por debajo de su punto de fusión, lo que permite que las partículas se adhieran y densifiquen sin licuarse por completo.Este proceso aumenta la resistencia del material, reduce la porosidad y mejora la integridad estructural.El proceso de sinterización suele incluir pasos como la selección del polvo, la compactación, el calentamiento y el postratamiento, con atmósferas controladas y temperaturas específicas adaptadas al tipo de metal.El resultado es un producto cohesivo de alta calidad apto para diversas aplicaciones industriales.
Explicación de los puntos clave:
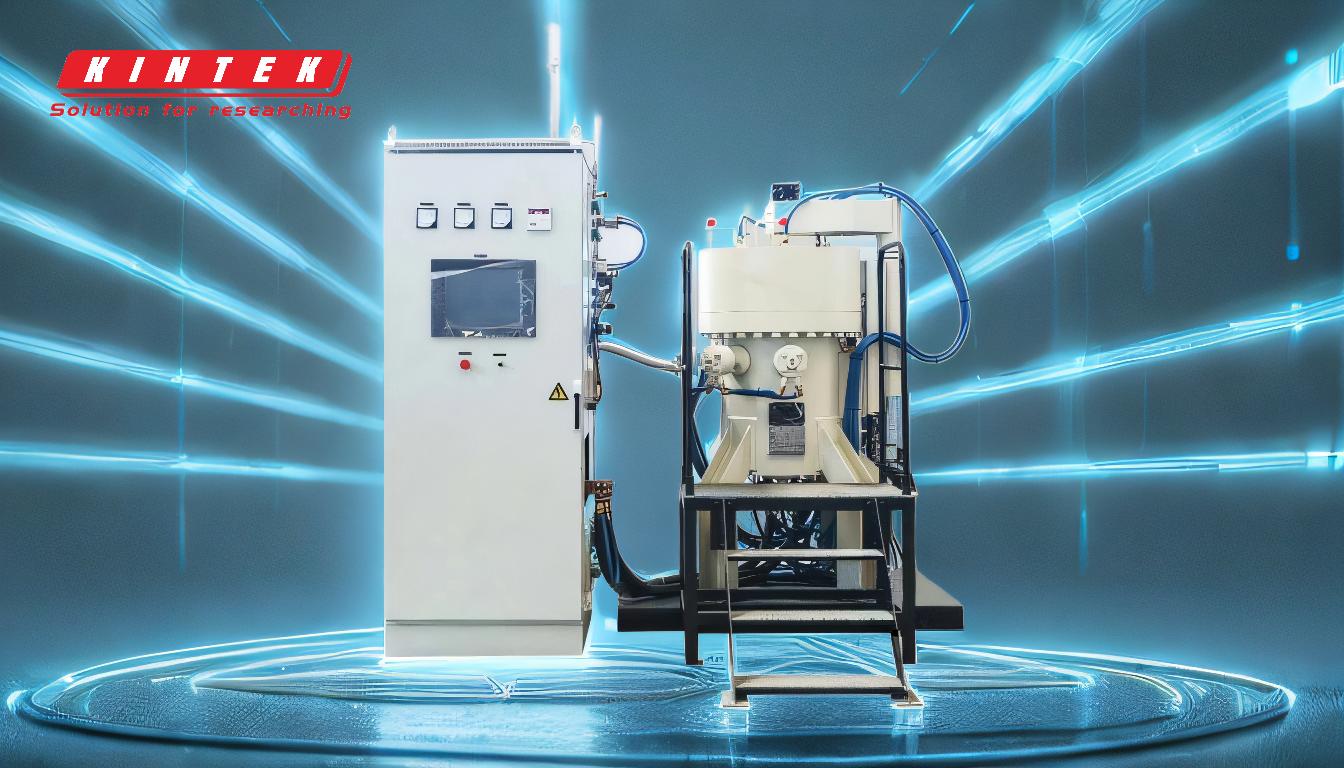
-
Definición y finalidad de la sinterización
- La sinterización es un proceso de tratamiento térmico utilizado en pulvimetalurgia para unir partículas metálicas, formando una estructura sólida y coherente.
- El objetivo principal es aumentar la resistencia del material, reducir la porosidad y conseguir la forma y las propiedades deseadas.
- Se realiza a temperaturas ligeramente inferiores al punto de fusión del metal para evitar la licuefacción completa y permitir al mismo tiempo la unión de las partículas.
-
Pasos del proceso de sinterización
-
Selección y preparación del polvo:
- El proceso comienza con la selección de la composición adecuada del polvo metálico, que determina las propiedades del producto final.Los metales más comunes son el hierro, el níquel, el molibdeno y el cobre.
- Pueden añadirse lubricantes o agentes de acoplamiento para mejorar la compactación y la unión.
-
Compactación:
- El polvo metálico se prensa en una matriz para darle una forma específica, formando una pieza "verde" con una resistencia inicial.
- La compactación garantiza una densidad y una forma uniformes antes de la sinterización.
-
Sinterización:
- La pieza verde se calienta en un horno de atmósfera controlada a una temperatura justo por debajo del punto de fusión del metal.
- Durante el calentamiento, las partículas se unen por difusión, reduciendo la porosidad y aumentando la densidad.
- En algunos casos puede utilizarse la sinterización en fase líquida (LPS) para acelerar la fusión de las partículas.
-
Tratamiento posterior:
- Tras la sinterización, la pieza puede someterse a procesos adicionales como el mecanizado, el revestimiento o el tratamiento térmico para mejorar sus propiedades o alcanzar tolerancias específicas.
-
Selección y preparación del polvo:
-
Mecanismos clave de la sinterización
-
Unión de partículas:
- A altas temperaturas, las partículas metálicas forman enlaces mediante difusión en estado sólido, creando una estructura cohesiva.
-
Reducción de la porosidad:
- La sinterización reduce el número de huecos entre las partículas, mejorando la densidad y las propiedades mecánicas del material.
-
Cambios microestructurales:
- El proceso activa microestructuras cristalinas martensíticas, contribuyendo a la resistencia y dureza del material.
-
Unión de partículas:
-
Factores que influyen en la sinterización
-
Temperatura y tiempo:
- La temperatura de sinterización debe controlarse cuidadosamente para garantizar una unión adecuada sin fundir el material.
- Los tiempos de sinterización más largos pueden mejorar la unión, pero también pueden provocar el crecimiento del grano, lo que afecta a las propiedades del material.
-
Control de la atmósfera:
- Una atmósfera controlada (por ejemplo, hidrógeno, nitrógeno o vacío) evita la oxidación y garantiza unas condiciones óptimas de adhesión.
-
Características del polvo:
- El tamaño, la forma y la composición de las partículas influyen significativamente en el proceso de sinterización y en la calidad del producto final.
-
Temperatura y tiempo:
-
Aplicaciones y ventajas
- El sinterizado se utiliza ampliamente en industrias como la automoción, la aeroespacial y la electrónica para producir componentes complejos de alta resistencia.
- Sus ventajas son la rentabilidad, la capacidad de crear formas complejas y la producción de materiales con propiedades a medida.
- El proceso es especialmente valioso para fabricar piezas de baja porosidad, gran durabilidad y excelentes prestaciones mecánicas.
Al comprender el proceso de sinterización y sus pasos clave, los fabricantes pueden optimizar la producción de componentes pulvimetalúrgicos, garantizando resultados de alta calidad para una amplia gama de aplicaciones.
Tabla resumen:
Aspecto clave | Detalles |
---|---|
Definición | Proceso de tratamiento térmico que une partículas metálicas en una estructura sólida. |
Pasos | Selección del polvo, compactación, calentamiento y postratamiento. |
Mecanismos clave | Adhesión de partículas, reducción de la porosidad y cambios microestructurales. |
Factores que influyen | Temperatura, tiempo, control de la atmósfera y características del polvo. |
Aplicaciones | Automoción, aeroespacial, electrónica, etc. |
Ventajas | Rentabilidad, formas complejas, baja porosidad y alta durabilidad. |
Optimice su proceso pulvimetalúrgico con el asesoramiento de expertos. póngase en contacto con nosotros ¡!