Introducción a los hornos de vacío para molibdeno
Los hornos de vacío de molibdenoson fundamentales en aplicaciones de alta temperatura, aprovechando las propiedades únicas del molibdeno para destacar en entornos exigentes. Estos avanzados sistemas no sólo son esenciales para la sinterización en atmósfera a alta temperatura, sino también para la sinterización al vacío de diversos materiales, lo que demuestra su versatilidad y su papel fundamental en los procesos industriales modernos. Este artículo profundiza en las intrincadas características, la construcción y las aplicaciones de los hornos de vacío de molibdeno, proporcionando información sobre sus avanzados sistemas de control y estrategias de mantenimiento, esenciales para garantizar un rendimiento óptimo y una larga vida útil.
Características clave y propósitos de los hornos de vacío de molibdeno
Los hornos de vacío de molibdeno son equipos especializados diseñados para el procesamiento a alta temperatura en un entorno de vacío controlado. Estos hornos son particularmente conocidos por su uso en la sinterización en atmósfera de alta temperatura y la sinterización al vacío de diversos materiales, que incluyen cerámica, metales y materiales compuestos. Las propiedades únicas del molibdeno, como su alto punto de fusión, su excelente conductividad térmica y su resistencia al choque térmico, lo convierten en un material ideal para los elementos calefactores de estos hornos.
Eficacia y estabilidad a altas temperaturas
Una de las principales características de los hornos de vacío de molibdeno es su capacidad para mantener la estabilidad a altas temperaturas. El molibdeno puede funcionar a temperaturas de hasta 1700°C, lo que resulta crucial para procesos como la sinterización, en los que es esencial un control preciso de la temperatura. La elevada conductividad térmica del molibdeno garantiza una transferencia de calor eficaz, lo que permite un calentamiento rápido y una distribución uniforme de la temperatura dentro de la cámara del horno. Esta eficacia es especialmente importante en aplicaciones industriales en las que el tiempo y los costes energéticos son factores significativos.
Rendimiento de vacío y control de la contaminación
Los hornos de vacío de molibdeno están diseñados para funcionar en vacío o en atmósfera controlada, lo que resulta esencial para evitar la contaminación de los materiales que se procesan. El entorno de vacío elimina la presencia de oxígeno y otros gases que podrían reaccionar con los materiales a altas temperaturas, preservando así su pureza e integridad. Esta característica es especialmente beneficiosa en el procesamiento de materiales de gran pureza y en aplicaciones en las que los niveles de contaminación de trazas deben mantenerse al mínimo.
Versatilidad en las aplicaciones
La versatilidad de los hornos de vacío de molibdeno se extiende a una amplia gama de aplicaciones más allá de la sinterización. Entre ellas se incluyen el tratamiento térmico, la soldadura fuerte, el recocido y el procesamiento de materiales avanzados como la cerámica transparente y los compuestos de matriz metálica. Cada una de estas aplicaciones se beneficia del control preciso de la temperatura y del entorno libre de contaminación que proporciona el horno.
Componentes estructurales y diseño
El diseño de un horno de molibdeno al vacío incorpora varios componentes clave que garantizan su funcionalidad y eficacia. Entre ellos se incluyen:
- Cuerpo y tapa del horno: Construidos en acero inoxidable de alta calidad, el cuerpo y la tapa del horno están diseñados para mantener un alto vacío y a menudo están refrigerados por agua para soportar las altas temperaturas.
- Elementos calefactores: Fabricados en molibdeno de gran pureza, estos elementos son cruciales para alcanzar y mantener las temperaturas requeridas.
- Pantallas aislantes: Se utilizan para minimizar la pérdida de calor y garantizar una distribución uniforme de la temperatura dentro de la cámara del horno.
- Sistema de vacío: Compuesto por bombas, válvulas y medidores, el sistema de vacío es esencial para mantener el entorno de vacío y controlar la atmósfera dentro del horno.
- Sistema de control: Los sistemas de control avanzados, que a menudo incluyen PLC e interfaces informáticas, permiten un control preciso de los parámetros del horno, garantizando la reproducibilidad y la seguridad de funcionamiento.
Mantenimiento y precauciones
Aunque los hornos de vacío de molibdeno ofrecen numerosas ventajas, también requieren un mantenimiento y un funcionamiento cuidadosos para garantizar la longevidad y el rendimiento. El molibdeno es sensible a la oxidación y la contaminación, por lo que los hornos deben funcionar en condiciones estrictamente controladas. Un mantenimiento regular, que incluya la inspección y sustitución de los elementos calefactores y las juntas, es crucial para evitar fallos y garantizar que el horno funcione con la máxima eficiencia.
En conclusión, los hornos de vacío de molibdeno son herramientas indispensables en el procesamiento a alta temperatura, ya que ofrecen estabilidad a altas temperaturas, transferencia de calor eficaz y un entorno libre de contaminación. Su versatilidad y precisión los convierten en un componente clave en el avance de la ciencia de los materiales y las tecnologías de procesamiento industrial.
Construcción y composición de los hornos de vacío de molibdeno
Los hornos de vacío de molibdeno son equipos sofisticados diseñados para aplicaciones de alta temperatura al vacío o en atmósferas controladas. Estos hornos son cruciales para procesos como la sinterización, el tratamiento térmico y la soldadura fuerte, donde es esencial mantener un entorno prístino. En la construcción de estos hornos intervienen varios componentes clave, cada uno de ellos diseñado para funcionar a la perfección en condiciones extremas.
Componentes estructurales
Cuerpo y tapa del horno: El cuerpo del horno suele ser de acero inoxidable, conocido por su resistencia a la corrosión y a la deformación a altas temperaturas. Las carcasas interior y exterior suelen ser de acero inoxidable 304, con la superficie exterior pulida a espejo para mejorar la durabilidad y la estética. La tapa, que es desmontable, incluye un mecanismo de refrigeración por agua en su sección central para evitar el sobrecalentamiento y garantizar un cierre hermético cuando está cerrada.
Fondo y sistema de vacío: La parte inferior del horno, similar a la tapa, incorpora refrigeración por agua y puertos para electrodos, termopares y otros instrumentos de control. El sistema de vacío es esencial para el funcionamiento del horno y consiste en una combinación de bombas de vacío, válvulas y medidores. Estos componentes trabajan conjuntamente para alcanzar y mantener los niveles de vacío necesarios, cruciales para evitar la oxidación y la contaminación de los materiales que se procesan.
Elementos calefactores y pantalla aislante: El corazón del horno reside en sus elementos calefactores, a menudo fabricados con molibdeno de gran pureza. El molibdeno se elige por su excelente resistencia a las altas temperaturas y su capacidad para mantener la integridad estructural hasta 1700°C. Los elementos calefactores están diseñados para funcionar a altas densidades de potencia, lo que garantiza un calentamiento rápido y uniforme. La pantalla aislante, fabricada normalmente con materiales como el tungsteno y el acero inoxidable, ayuda a mantener la temperatura dentro del horno y a reducir la pérdida de calor.
Consideraciones operativas
Sistemas de manipulación y control de materiales: Los hornos de vacío de molibdeno están equipados con sistemas de control avanzados que permiten una gestión precisa de la temperatura y el control del proceso. Estos sistemas pueden automatizarse mediante PLC e interfaces de pantalla táctil, lo que permite a los operarios supervisar y ajustar los parámetros en tiempo real. La inclusión de un control informatizado no sólo mejora la eficacia, sino que también garantiza la repetibilidad y la seguridad en los procesos de alta temperatura.
Características de refrigeración y seguridad: Dadas las altas temperaturas de funcionamiento, los sistemas de refrigeración son cruciales para la longevidad de los componentes del horno. Las camisas refrigeradas por agua alrededor del cuerpo, la tapa y el fondo del horno ayudan a disipar el calor y evitan daños estructurales. También se integran funciones de seguridad como válvulas de alivio de presión y funciones de parada de emergencia para proteger tanto el equipo como a los operarios.
Aplicaciones y ventajas
Los hornos de vacío de molibdeno son herramientas versátiles que se utilizan en una gran variedad de industrias, como la metalúrgica, la cerámica y la electrónica. Su capacidad para funcionar al vacío o en atmósferas controladas los hace ideales para procesos que requieren una gran pureza y una contaminación mínima. El uso de elementos calefactores de molibdeno garantiza un calentamiento eficaz y fiable, lo que contribuye a la calidad y consistencia generales de los productos finales.
En conclusión, la construcción y composición de los hornos de vacío de molibdeno están meticulosamente diseñadas para satisfacer las exigencias de las aplicaciones de alta temperatura y gran pureza. Cada componente, desde el cuerpo del horno hasta los elementos calefactores, desempeña un papel fundamental para garantizar el funcionamiento eficaz y seguro del horno, convirtiéndolo en una herramienta indispensable en entornos avanzados de fabricación e investigación.
Sistemas de control en hornos de vacío de molibdeno
Los hornos de vacío de molibdeno forman parte integral del procesamiento a alta temperatura y la síntesis de materiales, y emplean sistemas de control avanzados para garantizar la precisión y la eficacia. Estos sistemas de control, que incluyen sistemas de control automático por ordenador y controladores lógicos programables (PLC), son fundamentales para gestionar procesos complejos y mantener un funcionamiento óptimo de los hornos.
Sistemas de control automático por ordenador
Los sistemas de control automático por ordenador de los hornos de vacío de molibdeno están diseñados para gestionar funciones complejas de control lógico, supervisión continua de los parámetros del proceso y gestión de datos. Estos sistemas utilizan hardware y software informáticos específicos para supervisar operaciones como los índices de refundición, el control de la separación del arco y la adquisición de datos. Un PC de interfaz de operador (OIP) sirve de interfaz principal entre el operador y el proceso del horno, proporcionando visualización del proceso en tiempo real, ajustes de parámetros y gestión de recetas. El OIP también puede equiparse con una interfaz de red Ethernet para la transferencia de datos sin interrupciones a otros ordenadores conectados en red, lo que mejora la integración del sistema y la accesibilidad de los datos.
Controladores lógicos programables (PLC)
Los PLC han revolucionado el control de los hornos de vacío al sustituir los sistemas tradicionales basados en relés por controles digitales más fiables y eficaces. Introducidos originalmente para simplificar la gestión de múltiples instrumentos de control, los PLC son ahora indispensables en los modernos sistemas de hornos de vacío. Reducen la intervención del operario, garantizan una calidad constante del producto y minimizan el tiempo de inactividad del horno. En los hornos de vacío de molibdeno actuales, los PLC suelen estar integrados con interfaces de panel táctil, lo que permite a los operarios cargar y descargar el horno, seleccionar recetas de proceso e iniciar operaciones con sólo pulsar un botón.
Características y ventajas del sistema de control
La integración de sistemas de control avanzados en los hornos de vacío de molibdeno ofrece varias ventajas clave:
-
Precisión y consistencia: Los sistemas de control avanzados permiten realizar ajustes precisos de los parámetros del horno, garantizando una distribución uniforme del calor y unos resultados de procesamiento uniformes. Esta precisión es crucial para aplicaciones de alto valor en las que las propiedades del material deben controlarse estrictamente.
-
Eficiencia energética: Los modernos sistemas de control optimizan el uso de la energía ajustando dinámicamente los ciclos de calentamiento y las velocidades de enfriamiento en función de los datos en tiempo real. Esto no sólo reduce los costes operativos, sino que también minimiza el impacto medioambiental.
-
Supervisión y control remotos: Con la capacidad de funcionar desde ubicaciones remotas, estos sistemas mejoran la flexibilidad y la seguridad operativas. El acceso remoto permite la supervisión y los ajustes en tiempo real, reduciendo la necesidad de personal in situ durante las fases críticas del funcionamiento.
-
Gestión y análisis de datos: Los sistemas de control avanzados facilitan el registro y análisis exhaustivo de datos, lo que resulta esencial para la mejora de los procesos y el cumplimiento de las normas de calidad. Los datos históricos pueden utilizarse para perfeccionar los procesos y solucionar problemas de forma proactiva.
-
Seguridad mejorada: Los sistemas de control automatizados incluyen protocolos de seguridad que evitan los errores de los operarios y protegen contra las averías de los equipos. Esto es especialmente importante en entornos de alta temperatura y vacío, donde los riesgos de seguridad son elevados.
Aplicaciones y tendencias futuras
Los hornos de vacío de molibdeno equipados con sistemas de control avanzados se utilizan en diversas aplicaciones de alta temperatura, como la sinterización, el tratamiento térmico y la síntesis de materiales. A medida que avanza la tecnología, es probable que las tendencias futuras en los sistemas de control se centren en una mayor integración con la inteligencia artificial y los algoritmos de aprendizaje automático para predecir y optimizar el rendimiento del horno, mejorar el mantenimiento predictivo y mejorar la eficiencia general del proceso.
En conclusión, los avanzados sistemas de control de los hornos de vacío de molibdeno representan un importante salto adelante en precisión, eficiencia y seguridad. Estos sistemas son esenciales para cumplir los estrictos requisitos del procesamiento moderno a alta temperatura y la síntesis de materiales, garantizando que los hornos de vacío de molibdeno permanezcan a la vanguardia de las tecnologías de fabricación avanzadas.
Propiedades del material y rendimiento de los elementos calefactores de molibdeno
El molibdeno, un metal refractario conocido por su resistencia a altas temperaturas y su excelente conductividad eléctrica, se utiliza ampliamente en diversos elementos calefactores de entornos industriales y de laboratorio. Su capacidad para mantener la integridad estructural y el rendimiento a temperaturas extremas lo convierte en la opción preferida para aplicaciones que requieren durabilidad y fiabilidad.
Propiedades del molibdeno
El molibdeno presenta varias propiedades clave que lo hacen adecuado para elementos calefactores:
- Alto punto de fusión: El molibdeno tiene un punto de fusión de aproximadamente 2623°C (4753°F), que es significativamente más alto que el de muchos otros metales. Este elevado punto de fusión permite que los elementos calefactores de molibdeno funcionen a temperaturas de hasta 1700°C (3100°F) sin fallos estructurales.
- Buena conductividad eléctrica: El molibdeno es un buen conductor de la electricidad, lo que resulta crucial para la generación eficaz de calor en los elementos calefactores.
- Resistencia a la fluencia: A altas temperaturas, el molibdeno muestra una deformación mínima con el paso del tiempo, lo que se conoce como resistencia a la fluencia. Esta propiedad garantiza que los elementos calefactores mantengan su forma y rendimiento bajo una exposición prolongada a altas temperaturas.
- Baja expansión térmica: El molibdeno tiene un coeficiente de expansión térmica relativamente bajo, lo que ayuda a reducir la tensión y la deformación durante los ciclos rápidos de calentamiento y enfriamiento.
Rendimiento en entornos de alta temperatura
En entornos de altas temperaturas, los elementos calefactores de molibdeno demuestran un rendimiento excepcional:
- Resistencia a la oxidación: El molibdeno forma una capa protectora de trióxido de molibdeno (MoO3) cuando se expone a altas temperaturas en atmósferas oxidantes. Esta capa ayuda a evitar una mayor oxidación y prolonga la vida útil de los elementos calefactores.
- Resistencia y durabilidad: A pesar de su funcionamiento a altas temperaturas, el molibdeno conserva su resistencia y no se vuelve quebradizo a menos que se exponga a temperaturas superiores a 1700 °C (3100 °F). Esto garantiza que los elementos calefactores puedan soportar tensiones mecánicas y choques térmicos.
- Distribución eficaz del calor: La buena conductividad térmica del molibdeno garantiza una distribución uniforme del calor, esencial para un calentamiento uniforme en hornos industriales y de laboratorio.
Efectos de la aleación en el molibdeno
La aleación del molibdeno con otros elementos mejora sus propiedades y amplía su rango operativo:
- Aleación TZM: La adición de titanio y circonio al molibdeno forma la aleación TZM, que tiene mayor resistencia, mayor temperatura de recristalización y mejor resistencia a la fluencia. El TZM puede funcionar a temperaturas de elemento de hasta 1400°C (2552°F).
- Molibdeno lantanado (MoLa): La incorporación de trióxido de lantano al molibdeno da como resultado una estructura de grano fino de "fibra apilada" que mejora significativamente la resistencia a la recristalización y al alabeo a alta temperatura. El MoLa puede utilizarse a temperaturas de elemento de hasta 2000°C (3632°F).
- Disiliciuro de molibdeno (MoSi2): Este compuesto ofrece baja resistividad, características positivas de resistencia-temperatura y excelente resistencia a la oxidación a alta temperatura. Los elementos calefactores de MoSi2 pueden funcionar con cargas de vatios muy elevadas y mantener un rendimiento constante durante toda su vida útil.
Aplicaciones de los elementos calefactores de molibdeno
Los elementos calefactores de molibdeno se utilizan ampliamente en diversas aplicaciones, entre las que se incluyen:
- Hornos de vacío: Debido a su resistencia a la oxidación y a su alto punto de fusión, el molibdeno es ideal para hornos de vacío utilizados en procesos de tratamiento térmico como el temple y la soldadura fuerte.
- Hornos industriales y de laboratorio: La capacidad del molibdeno para soportar altas temperaturas y una distribución uniforme del calor lo hacen adecuado para una amplia gama de hornos industriales y de laboratorio.
- Entornos de oxidación a alta temperatura: La formación de una capa protectora de óxido en los elementos calefactores de molibdeno garantiza su longevidad y fiabilidad en atmósferas oxidantes de alta temperatura.
En conclusión, el molibdeno y sus aleaciones son materiales cruciales para los elementos calefactores debido a su excepcional rendimiento a altas temperaturas, resistencia y durabilidad. Mediante una cuidadosa selección y aleación, estos materiales pueden adaptarse para satisfacer los requisitos específicos de diversas aplicaciones industriales y de laboratorio, garantizando procesos de calentamiento eficaces y fiables.
Mantenimiento y rendimiento a largo plazo de los hornos de vacío de molibdeno
El mantenimiento del rendimiento a largo plazo de los hornos de vacío de molibdeno es crucial para garantizar un funcionamiento constante y fiable. Estos hornos están diseñados para funcionar en condiciones extremas, y un mantenimiento adecuado puede evitar problemas como el endurecimiento, el colapso y la pérdida de resistencia de los elementos calefactores a altas temperaturas. A continuación se detallan las directrices para ayudar a preservar la integridad y la eficiencia de su horno de vacío de molibdeno.
Mantenimiento de los elementos calefactores
Los elementos calefactores de molibdeno son componentes críticos de los hornos de vacío. Deben mantenerse cuidadosamente para evitar daños y garantizar su longevidad. Después de cada uso, inspeccione los elementos calefactores para detectar cualquier signo de daño. Compruebe la estanqueidad de las conexiones para evitar problemas eléctricos. Si un elemento calefactor está dañado, es posible repararlo. Los elementos de molibdeno pueden repararse normalmente hasta tres veces por banda de elemento, pero esto requiere precauciones especiales debido a la fragilidad del molibdeno y a la posible liberación de vapores tóxicos de dióxido de molibdeno durante el proceso de reparación.
Acondicionamiento de elementos calefactores nuevos
Los elementos calefactores de molibdeno nuevos deben acondicionarse para mejorar su rendimiento y longevidad. Esto implica calentar el horno vacío a 1550°C y mantenerlo a esa temperatura durante una hora. Este proceso ayuda a aplicar una fina capa protectora de vidrio a los elementos, lo que puede evitar su degradación prematura. Si el horno debe funcionar durante periodos prolongados a temperaturas inferiores a 800°C, reacondicione las superficies utilizando el procedimiento de cocción inicial para mantener su integridad.
Control de la velocidad de calentamiento
La velocidad de calentamiento es un factor crítico para mantener la integridad estructural de los elementos calefactores. Un calentamiento rápido puede provocar dilataciones térmicas y deformaciones de la pantalla térmica. Se recomienda utilizar una velocidad de calentamiento lenta, especialmente en la fase de alta temperatura. Por ejemplo, reducir la velocidad de rampa para temperaturas de 100-200°C por debajo de la temperatura nominal máxima del horno a 60-100°C por hora puede evitar tensiones indebidas en los elementos calefactores.
Comprobaciones de vacío y fugas
Antes de iniciar el proceso de calentamiento, es esencial comprobar la tasa de fuga de vacío y el grado de vacío final. Garantizar un entorno de vacío adecuado es crucial para el funcionamiento eficaz del horno. Cuando el equipo no esté en uso, guárdelo en estado de vacío. Si hay sustancias volátiles en el interior del horno, debe secarse para evitar la contaminación y posibles daños en los elementos calefactores.
Manipulación de productos y control de impurezas
Al manipular los productos, tenga cuidado de evitar que caigan sobre la superficie de los elementos calefactores de molibdeno, ya que podrían resultar dañados. Los productos que contengan elementos de hierro con puntos de fusión más bajos no deben volatilizarse sobre la cinta de molibdeno del horno, ya que esto puede provocar la fusión con el tiempo. Sujete los productos firmemente con ambas manos o utilice objetos mecánicos para evitar caídas accidentales. Además, controle estrictamente el contenido de impurezas de los productos para evitar la contaminación de los elementos calefactores.
Conexiones eléctricas y sistemas de refrigeración
La conexión eléctrica a los elementos calefactores se realiza normalmente a través de un pasamuros refrigerado por agua. Esta conexión sellada contiene el conductor que lleva la corriente al elemento calefactor. Los pasamuros están disponibles en varios rangos de corriente, incluyendo diseños de alta capacidad. La refrigeración por agua evita el sobrecalentamiento, y es esencial utilizar un sistema de refrigeración de circuito cerrado conectado a tierra con refrigerantes no conductores, como agua desionizada o etilenglicol. Los conductos de refrigeración deben construirse con materiales no conductores, como tubos de polipropileno, para evitar que el refrigerante se convierta en parte del circuito.
Diseño de elementos calefactores resistentes
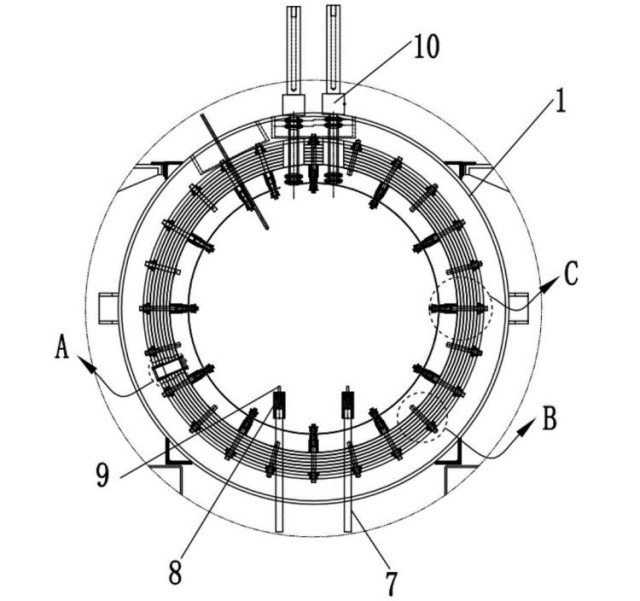
Para garantizar que el cable calefactor del horno de vacío mantiene la resistencia necesaria a altas temperaturas y evita el endurecimiento, el colapso o el pandeo, el tamaño de construcción del cable calefactor debe diseñarse cuidadosamente. Esto incluye el uso de alambre de resistencia en espiral y prestar atención al diámetro de curvatura, el paso y el diámetro medio del elemento calefactor. El cuerpo calefactor debe fijarse contra el revestimiento aislante del horno de vacío, con 95 piezas cerámicas colocadas en el revestimiento aislante para proporcionar un espacio de expansión adecuado. Durante el uso, coloque los elementos calefactores de forma adecuada, generalmente a intervalos de 100-200 mm, y engánchelos firmemente para evitar que el cable de resistencia quede plano. Además, evite el contacto directo entre los hilos del horno para evitar cortocircuitos, normalmente utilizando chapas aislantes.
Siguiendo estas exhaustivas directrices de mantenimiento y diseño, podrá garantizar el rendimiento y la fiabilidad a largo plazo de su horno de molibdeno al vacío, prolongando su vida útil y manteniendo una eficiencia operativa óptima.
Aplicaciones de los hornos de vacío de molibdeno en la industria
Los hornos de vacío de molibdeno desempeñan un papel crucial en diversos sectores industriales debido a su capacidad para funcionar a altas temperaturas y en condiciones de vacío, garantizando un control preciso del proceso de calentamiento sin oxidación ni contaminación. Esta sección explora las diversas aplicaciones de los hornos de vacío de molibdeno en industrias como la cerámica, la metalurgia, la electrónica y los tratamientos de materiales especiales.
Industria cerámica
En la industria cerámica, los hornos de vacío de molibdeno son esenciales para producir cerámicas densas de alta calidad con propiedades uniformes. Estos hornos permiten la sinterización de cerámicas avanzadas a temperaturas de hasta 2400°C, lo que es crucial para conseguir las propiedades mecánicas, eléctricas y térmicas deseadas. El entorno de vacío evita la oxidación de los polvos cerámicos, lo que permite obtener productos de mayor pureza y rendimiento. Las aplicaciones incluyen la producción de cerámicas técnicas utilizadas en electrónica, aeroespacial y dispositivos médicos.
Metalurgia
El sector metalúrgico utiliza ampliamente hornos de vacío de molibdeno para la fusión y el tratamiento térmico de metales. Estos hornos son ideales para procesar metales refractarios como el tungsteno, el molibdeno y el tántalo, que requieren altos puntos de fusión y resisten la oxidación. La fusión en vacío ayuda a eliminar las impurezas volátiles y los gases, lo que da como resultado metales con una pureza y unas propiedades mecánicas superiores. Además, estos hornos se utilizan para el tratamiento térmico de aceros de alta resistencia, aceros inoxidables y aceros para herramientas con el fin de conseguir la dureza, tenacidad y resistencia al desgaste deseadas.
Electrónica
En la industria electrónica, los hornos de vacío de molibdeno se emplean para la producción de dispositivos semiconductores y circuitos integrados. Los hornos se utilizan para procesos como la sinterización, el recocido y la difusión, que requieren un control preciso de la temperatura y un entorno libre de contaminación. Las capacidades de alta temperatura de los hornos de molibdeno permiten procesar materiales avanzados como el carburo de silicio y el nitruro de galio, que son fundamentales para los dispositivos electrónicos de próxima generación.
Tratamientos especiales de materiales
Los hornos de vacío de molibdeno también se utilizan para tratamientos especializados de materiales en diversas industrias. Entre ellos se incluyen:
- Soldadura fuerte y blanda: Los hornos de vacío proporcionan un entorno ideal para las operaciones de soldadura fuerte y blanda, garantizando uniones de alta calidad con un mínimo de oxidación y porosidad. Esto es especialmente importante en las industrias aeroespacial y del automóvil, donde la fiabilidad y el rendimiento son fundamentales.
- Procesamiento de combustible nuclear: Los hornos de molibdeno se utilizan para la fabricación de pastillas de combustible nuclear, garantizando una alta pureza y densidad. El entorno de vacío ayuda a eliminar impurezas y gases volátiles, lo que es esencial para la seguridad y el rendimiento nuclear.
- Fundición de vidrio: En la industria del vidrio, los hornos de vacío de molibdeno se utilizan para fundir vidrios de gran pureza y crear cerámicas técnicas. Las altas temperaturas y la atmósfera controlada permiten la producción de vidrios especiales con propiedades ópticas y mecánicas únicas.
Ventajas de los hornos de vacío de molibdeno
El uso de hornos de vacío de molibdeno ofrece varias ventajas, entre las que se incluyen:
- Capacidades de alta temperatura: Los elementos calefactores de molibdeno pueden soportar temperaturas de hasta 2400°C, lo que los hace adecuados para el procesamiento de materiales a alta temperatura.
- Atmósfera controlada: El entorno de vacío evita la oxidación y la contaminación, garantizando productos de alta calidad con propiedades constantes.
- Eficiencia energética: Los hornos de vacío están diseñados para ser eficientes energéticamente, reduciendo los costes operativos y el impacto medioambiental.
- Versatilidad: Los hornos de vacío de molibdeno pueden configurarse para diversas aplicaciones, lo que los convierte en una herramienta versátil en múltiples industrias.
En conclusión, los hornos de vacío de molibdeno son indispensables en la industria moderna, ya que permiten producir materiales y componentes de alta calidad con un control preciso y una contaminación mínima. Sus aplicaciones abarcan la cerámica, la metalurgia, la electrónica y los tratamientos de materiales especiales, lo que pone de relieve su papel fundamental en el avance de los procesos tecnológicos e industriales.
Futuras tendencias e innovaciones en la tecnología de hornos de vacío de molibdeno
El campo de la tecnología de hornos de vacío de molibdeno está preparado para importantes avances e innovaciones que mejorarán la eficiencia y ampliarán las aplicaciones en diversas industrias. A medida que aumenta la demanda de materiales de alta calidad y procesos de tratamiento térmico precisos, el desarrollo de hornos de vacío de molibdeno avanzados se vuelve crucial.
Mejoras en la eficiencia
Uno de los principales focos de atención en la evolución de la tecnología de los hornos de molibdeno al vacío es la mejora de la eficiencia operativa. Se espera que las innovaciones en elementos calefactores, materiales aislantes y sistemas de control reduzcan el consumo de energía y mejoren la uniformidad de la temperatura. Por ejemplo, la integración de materiales aislantes avanzados como las fibras cerámicas y el aislamiento multicapa puede reducir significativamente las pérdidas de calor, mejorando así la eficiencia energética global del horno.
Además, el desarrollo de sistemas de control inteligentes que utilizan inteligencia artificial y algoritmos de aprendizaje automático puede optimizar los ciclos de calentamiento, predecir las necesidades de mantenimiento y ajustar los parámetros operativos en tiempo real. Estos sistemas pueden analizar grandes cantidades de datos recogidos de sensores dentro del horno para garantizar un rendimiento óptimo y un tiempo de inactividad mínimo.
Nuevas aplicaciones
La versatilidad de los hornos de vacío de molibdeno está abriendo nuevas vías de aplicación en campos emergentes como la fabricación aditiva, la cerámica avanzada y el procesamiento de semiconductores. La capacidad de controlar la atmósfera y la temperatura con gran precisión hace que estos hornos sean ideales para procesar materiales avanzados que requieren condiciones ambientales específicas.
En el campo de la fabricación aditiva, los hornos de vacío de molibdeno pueden utilizarse para el postprocesado de piezas metálicas, garantizando que estén libres de impurezas y tengan las propiedades mecánicas deseadas. Del mismo modo, en la producción de cerámica avanzada, estos hornos pueden facilitar la sinterización de formas y composiciones complejas que no son posibles con los métodos convencionales.
Innovaciones en materiales
El desarrollo de nuevas aleaciones y compuestos de molibdeno es otra área de innovación. Mediante la incorporación de elementos como titanio, circonio y metales de tierras raras, los investigadores están creando aleaciones de molibdeno con mayor resistencia a altas temperaturas, resistencia a la corrosión y conductividad térmica. Estos materiales avanzados pueden ampliar el rango de temperaturas de funcionamiento de los elementos calefactores de molibdeno y mejorar su durabilidad.
Además, el uso de la nanotecnología en la producción de elementos calefactores de molibdeno puede dar lugar a mejoras significativas en su rendimiento. Los revestimientos nanoestructurados pueden mejorar la emisividad de los elementos, lo que permite una transferencia de calor más eficiente y un menor consumo de energía.
Consideraciones medioambientales
A medida que la normativa medioambiental se hace más estricta, el diseño de los hornos de vacío de molibdeno también evoluciona para minimizar su huella ecológica. Se están explorando innovaciones en el diseño de hornos que reduzcan la generación de residuos y mejoren las capacidades de reciclaje. Además, el desarrollo de hornos energéticamente eficientes que cumplan las normas internacionales de consumo de energía se está convirtiendo en una prioridad para los fabricantes.
Conclusión
El futuro de loshornos de vacío de molibdeno es brillante, con numerosas innovaciones en el horizonte que impulsarán mejoras en la eficiencia y ampliarán las aplicaciones. Al aprovechar los avances en la ciencia de los materiales, los sistemas de control y la sostenibilidad medioambiental, la industria está preparada para satisfacer la creciente demanda de materiales de alta calidad y de ingeniería de precisión. A medida que estas tecnologías sigan evolucionando, desempeñarán un papel crucial en la configuración del futuro de diversas industrias, desde la aeroespacial y la automovilística hasta la electrónica y la sanitaria.
CONTÁCTANOS PARA UNA CONSULTA GRATUITA
Los productos y servicios de KINTEK LAB SOLUTION han sido reconocidos por clientes de todo el mundo. Nuestro personal estará encantado de ayudarle con cualquier consulta que pueda tener. ¡Contáctenos para una consulta gratuita y hable con un especialista del producto para encontrar la solución más adecuada para sus necesidades de aplicación!