La sinterización es un proceso de fabricación crítico utilizado para transformar materiales en polvo en cuerpos densos y sólidos mediante la aplicación de calor y presión sin alcanzar el punto de fusión del material. Este proceso se utiliza ampliamente en industrias como la pulvimetalurgia y la cerámica. El proceso de sinterización suele constar de varias etapas, como la preparación del polvo, la compactación, el calentamiento y el enfriamiento. Durante el calentamiento, las partículas se densifican y se fusionan, formando una masa unificada con mejores propiedades mecánicas. El proceso puede mejorarse utilizando técnicas como la sinterización en fase líquida (LPS) o añadiendo aglutinantes y aditivos para rellenar los poros y mejorar la resistencia del material. La sinterización es especialmente útil para materiales con puntos de fusión elevados, como el tungsteno y el molibdeno, y es esencial para crear componentes duraderos y de alto rendimiento.
Explicación de los puntos clave:
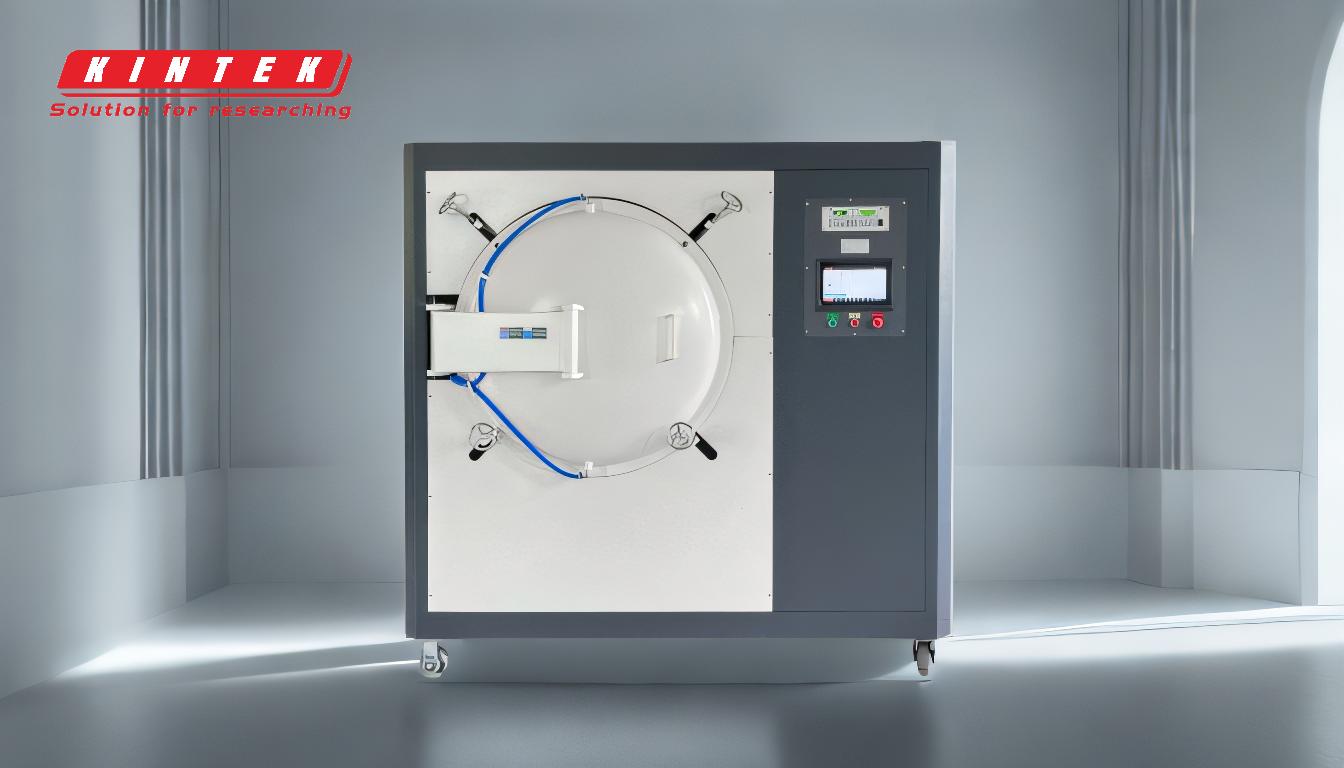
-
Definición y finalidad de la sinterización:
- La sinterización es un proceso que transforma materiales en polvo en cuerpos densos y sólidos aplicando calor y presión por debajo del punto de fusión del material.
- Se utiliza en industrias como la pulvimetalurgia y la cerámica para crear componentes duraderos y de alto rendimiento.
- El proceso es especialmente útil para materiales con puntos de fusión extremadamente altos, como el wolframio y el molibdeno.
-
Etapas del proceso de sinterización:
-
Preparación del polvo:
- Consiste en mezclar materias primas, aglutinantes y aditivos para crear un polvo o una pasta uniforme.
- En el caso de la cerámica, esto puede incluir la mezcla de agua, defloculante, aglutinante y polvo cerámico sin cocer para formar una suspensión secada por pulverización.
-
Compactación del polvo:
- El polvo se densifica mecánicamente mediante técnicas de prensado en frío o en caliente para formar una "pieza verde" (una forma presinterizada).
- La compactación garantiza que las partículas de polvo se empaqueten estrechamente, reduciendo la porosidad.
-
Calefacción y consolidación:
- La parte verde se calienta justo por debajo del punto de fusión del material, lo que permite que las partículas se unan mediante difusión atómica.
- Esta etapa activa las microestructuras cristalinas martensíticas y densifica el material.
-
Enfriamiento y solidificación:
- El material se enfría y solidifica en una masa unificada con propiedades mecánicas mejoradas.
-
Preparación del polvo:
-
Mecanismos clave de la sinterización:
-
Difusión atómica:
- Los átomos se difunden a través de los límites de las partículas, fusionándolas para formar una pieza sólida.
-
Sinterización en fase líquida (LPS):
- Se introduce una fase líquida (por ejemplo, un aglutinante o aditivo) para acelerar la fusión de las partículas y rellenar los poros restantes.
-
Densificación de partículas:
- Las partículas se densifican y fusionan, reduciendo la porosidad y aumentando la resistencia del material.
-
Difusión atómica:
-
Factores que influyen en la sinterización:
-
Control de la temperatura:
- El control preciso de la temperatura de calentamiento es crucial para evitar la fusión y garantizar al mismo tiempo una unión adecuada de las partículas.
-
Aplicación de presión:
- Se aplica presión durante la compactación para garantizar un empaquetamiento uniforme de las partículas y reducir la porosidad.
-
Aditivos y aglutinantes:
- Elementos como el polvo de cobre o los carburos cementados, junto con los aglutinantes, potencian la sinterización al rellenar los poros y mejorar el flujo del material.
-
Control de la atmósfera:
- Una atmósfera controlada (por ejemplo, gas inerte) evita la oxidación y la contaminación durante la sinterización.
-
Control de la temperatura:
-
Aplicaciones del sinterizado:
-
Pulvimetalurgia:
- Se utiliza para fabricar componentes metálicos de formas complejas y gran resistencia, como engranajes, cojinetes y piezas de automoción.
-
Fabricación de cerámica:
- Se utiliza para crear componentes cerámicos como baldosas, aislantes y herramientas de corte.
-
Materiales con alto punto de fusión:
- Esencial para procesar materiales como el wolframio y el molibdeno, difíciles de fundir y moldear con métodos tradicionales.
-
Pulvimetalurgia:
-
Ventajas de la sinterización:
-
Propiedades mejoradas de los materiales:
- Los materiales sinterizados presentan mayor resistencia, dureza y durabilidad que los no sinterizados.
-
Relación coste-eficacia:
- El sinterizado permite fabricar piezas con una forma casi neta, lo que reduce la necesidad de un mecanizado exhaustivo y el desperdicio de material.
-
Versatilidad:
- El proceso puede adaptarse a una amplia gama de materiales y aplicaciones, desde metales hasta cerámica.
-
Propiedades mejoradas de los materiales:
-
Retos de la sinterización:
-
Control de la porosidad:
- Conseguir una baja porosidad manteniendo la resistencia del material puede ser un reto, especialmente en formas complejas.
-
Precisión dimensional:
- La contracción durante la sinterización puede afectar a la precisión dimensional, lo que exige un diseño y un control del proceso cuidadosos.
-
Limitaciones materiales:
- No todos los materiales son adecuados para la sinterización, en particular los que tienen malas propiedades de difusión o puntos de fusión bajos.
-
Control de la porosidad:
Al comprender estos puntos clave, los compradores de equipos y consumibles pueden tomar decisiones informadas sobre la selección de materiales de sinterización, aditivos y equipos para lograr las propiedades y el rendimiento deseados del material.
Cuadro recapitulativo:
Aspecto | Detalles |
---|---|
Definición | Transforma materiales pulverulentos en sólidos densos mediante calor y presión. |
Etapas clave | Preparación del polvo, compactación, calentamiento y enfriamiento. |
Mecanismos | Difusión atómica, sinterización en fase líquida (LPS) y densificación de partículas. |
Aplicaciones | Pulvimetalurgia, fabricación de cerámica, materiales de alto punto de fusión. |
Ventajas | Mayor resistencia, rentabilidad y versatilidad. |
Desafíos | Control de la porosidad, precisión dimensional y limitaciones de los materiales. |
Descubra cómo el sinterizado puede mejorar su proceso de fabricación- contacte con nosotros ¡para una orientación experta!