El proceso de desaglomerado es un paso crítico en la fabricación de piezas mediante moldeo por inyección de polvo (PIM) o moldeo por inyección de metal (MIM). Implica la eliminación del aglutinante, un material temporal que se utiliza para mantener juntas las partículas de polvo durante la formación inicial de la pieza. El proceso de desaglomerado es esencial para garantizar que el producto final tenga las propiedades mecánicas y la precisión dimensional deseadas. Este proceso se puede lograr mediante varios métodos, incluida la desaglutinación térmica, la desaglutinación por solvente o la desaglutinación catalítica, cada uno con sus propias ventajas y limitaciones. La elección del método de desaglomerado depende del tipo de aglutinante utilizado, el material de la pieza y las propiedades deseadas del producto final.
Puntos clave explicados:
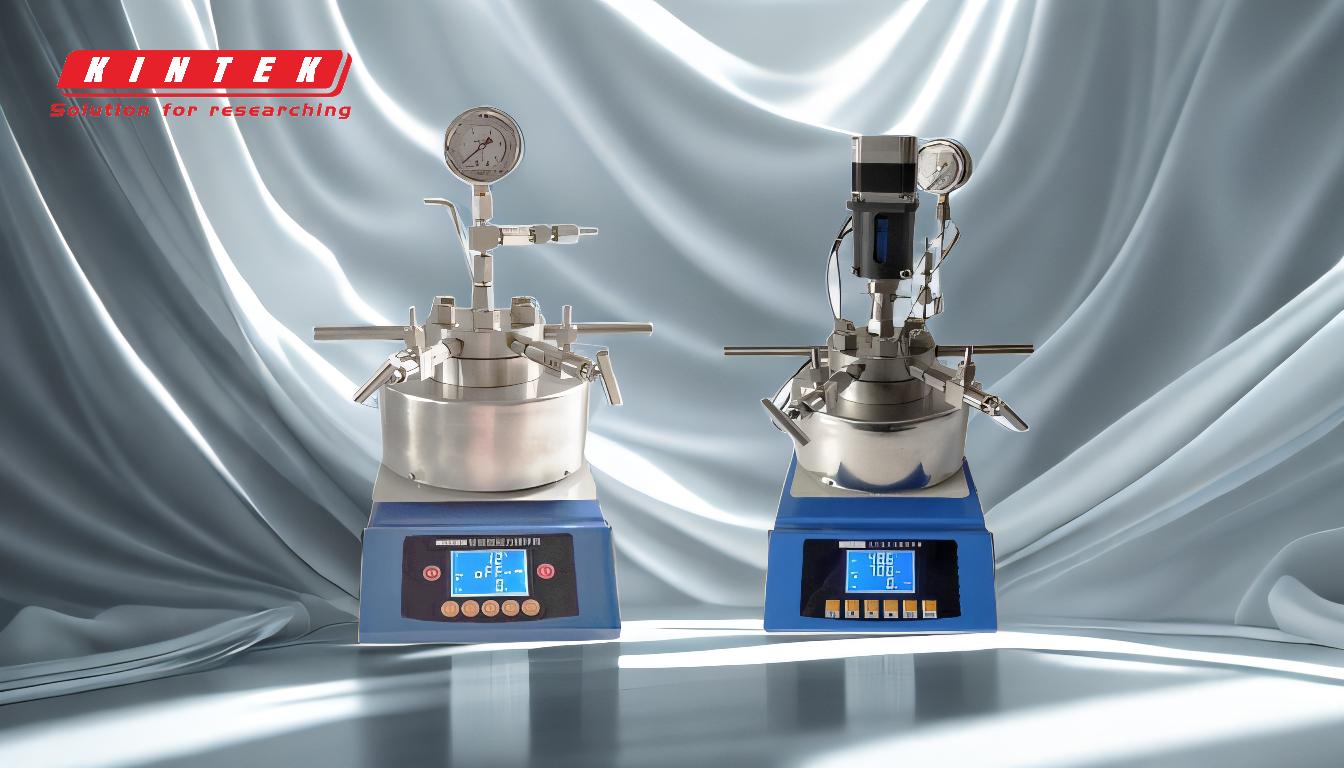
-
Definición de desasociación:
- El desaglomerado es el proceso de eliminar el material aglutinante de una pieza verde (una pieza que ha sido moldeada pero aún no sinterizada) en el moldeo por inyección de polvo. El aglutinante suele ser un polímero o cera que se mezcla con el polvo metálico o cerámico para facilitar el proceso de conformación. Una vez que se le da forma a la pieza, se debe quitar el aglutinante para permitir que las partículas de polvo se sintericen juntas durante el proceso de sinterización final.
-
Importancia de la desaglutinación:
- El proceso de desaglomerado es crucial porque cualquier aglutinante residual que quede en la pieza puede provocar defectos como grietas, huecos o distorsiones durante el proceso de sinterización. Una eliminación adecuada del aglutinante garantiza que el producto final tenga las propiedades mecánicas, la precisión dimensional y el acabado superficial deseados. También ayuda a lograr una densidad uniforme en toda la pieza, lo cual es esencial para su desempeño en las aplicaciones.
-
Métodos de desaglutinación:
- Desvinculación térmica: Este es el método más común, donde la parte verde se calienta en un ambiente controlado para descomponer y evaporar el aglutinante. La temperatura se aumenta gradualmente para evitar una rápida evolución de gas, que podría provocar grietas o hinchazón. La desaglomeración térmica es adecuada para una amplia gama de materiales pero requiere un control cuidadoso de la temperatura y la atmósfera.
- Desaglutinación de solventes: En este método, la parte verde se sumerge en un disolvente que disuelve el aglutinante. El disolvente penetra en la pieza y disuelve el aglutinante, que luego se elimina por evaporación o extracción. La desaglutinación con solvente es más rápida que la desaglutinación térmica, pero se limita a aglutinantes que son solubles en el solvente elegido.
- Desunión catalítica: Este método implica el uso de un catalizador para descomponer el aglutinante en moléculas más pequeñas que puedan eliminarse fácilmente. La desaglomeración catalítica se utiliza normalmente para piezas fabricadas con aglutinantes específicos que son sensibles a la descomposición catalítica. Ofrece una tasa de desaglomerado más rápida y puede ser más eficiente energéticamente que el desaglomerado térmico.
-
Desafíos en la desvinculación:
- Uno de los principales desafíos en el proceso de desaglomerado es garantizar que el aglutinante se elimine uniformemente en toda la pieza. Una desaglomeración no uniforme puede provocar una contracción diferencial durante la sinterización, lo que puede provocar deformaciones o grietas. Otro desafío es controlar la tasa de eliminación del aglutinante para prevenir la formación de defectos. La eliminación rápida del aglutinante puede provocar que la pieza colapse o desarrolle grietas, mientras que la eliminación lenta puede prolongar el proceso de fabricación.
-
Consideraciones posteriores a la desvinculación:
- Después de desvincular, la pieza se encuentra en un estado frágil conocido como "parte marrón". Tiene una estructura porosa con las partículas de polvo unidas sin apretar. La parte marrón debe manipularse con cuidado para evitar daños antes de que pase por el proceso de sinterización final. La sinterización implica calentar la pieza a una temperatura por debajo de su punto de fusión, lo que hace que las partículas de polvo se unan y formen una pieza densa y sólida.
-
Aplicaciones de la desaglutinación:
- El proceso de desaglomerado se utiliza ampliamente en la producción de piezas de formas complejas para diversas industrias, incluidas la automotriz, aeroespacial, médica y electrónica. Las piezas producidas utilizando PIM o MIM a menudo requieren geometrías complejas y alta precisión, lo que hace que la eliminación de ligaduras sea un paso crítico para lograr las propiedades finales deseadas.
En resumen, el proceso de desaglomerado es un paso vital en el moldeo por inyección de polvo que garantiza la eliminación del material aglutinante de la parte verde. Desempeña un papel importante en la determinación de la calidad y el rendimiento del producto final. La elección del método de desaglomerado depende del material, el aglutinante y las propiedades deseadas, y un control cuidadoso del proceso es esencial para evitar defectos y lograr resultados óptimos.
Tabla resumen:
Aspecto | Detalles |
---|---|
Definición | Eliminación de material aglutinante de una pieza verde en moldeo por inyección de polvo. |
Importancia | Garantiza propiedades mecánicas, precisión dimensional y densidad uniforme. |
Métodos | Desaglomerado térmico, solvente y catalítico, cada uno con ventajas únicas. |
Desafíos | Eliminación uniforme de aglutinantes, control de dosis y prevención de defectos. |
Post-desvinculación | La pieza marrón frágil requiere un manejo cuidadoso antes de la sinterización. |
Aplicaciones | Industrias automotriz, aeroespacial, médica y electrónica. |
¿Necesita orientación experta sobre la desaglomeración de su proceso de moldeo por inyección de polvo? Contáctanos hoy para aprender más!