La velocidad de calentamiento de la alúmina depende de la aplicación específica y del tipo de horno que se utilice.En general, la velocidad de calentamiento recomendada para los tubos de alúmina es de 5-10°C/min, con preferencia por 5°C/min para evitar el choque térmico y garantizar una sinterización uniforme.Las velocidades de enfriamiento también deben controlarse, idealmente por debajo de 10°C/min, siendo 5°C/min la óptima.Los cambios rápidos de temperatura pueden causar estrés térmico y provocar roturas o una sinterización insuficiente.Para el calentamiento inicial, se aconseja un ritmo más lento de 150-300°C por hora para minimizar el choque térmico.Estas directrices garantizan la longevidad y el rendimiento de los componentes de alúmina en entornos de alta temperatura.
Explicación de los puntos clave:
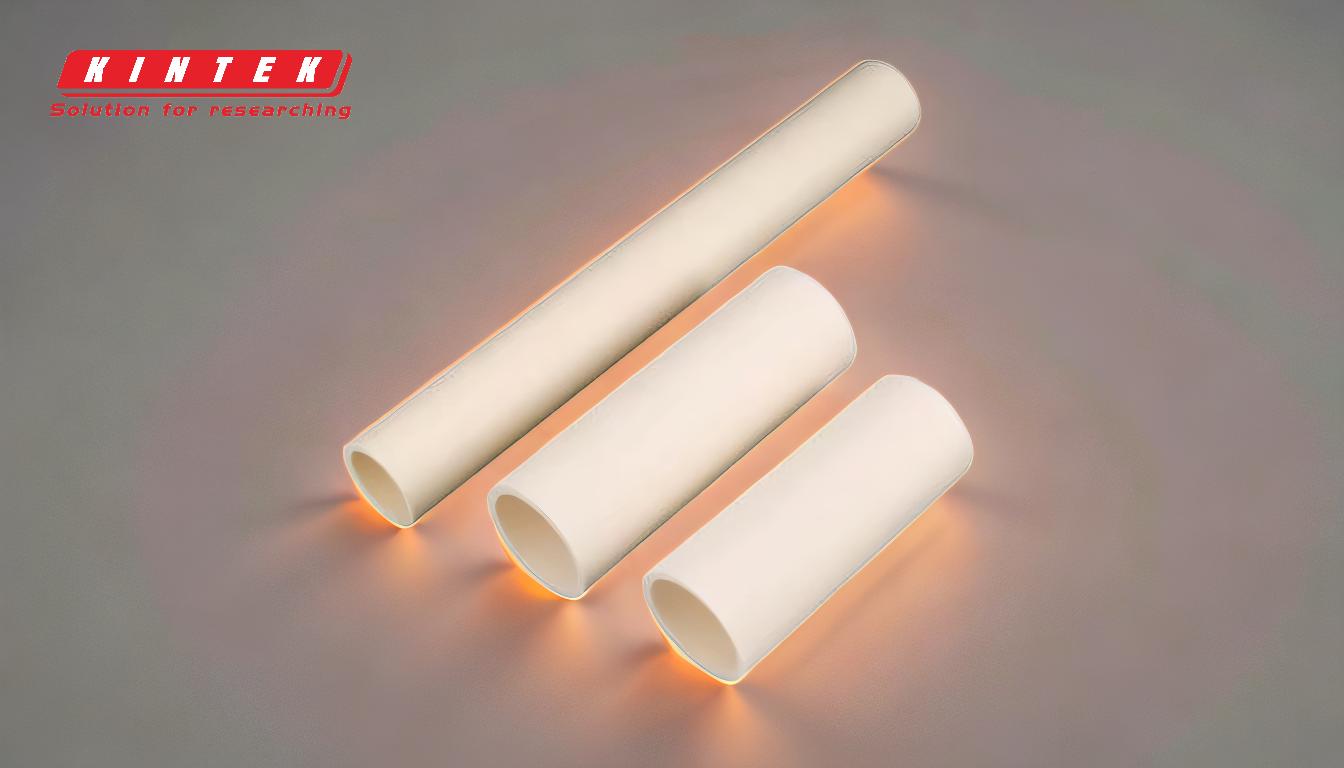
-
Velocidad de calentamiento recomendada para la alúmina:
- La velocidad de calentamiento estándar para tubos de horno de alúmina es de 5-10°C/min con 5°C/min siendo la velocidad preferida.Esto garantiza un calentamiento uniforme y minimiza el riesgo de choque térmico.
- Una velocidad de calentamiento más lenta de 150-300°C por hora durante las primeras 1-1,5 horas para reducir el choque térmico, especialmente durante la fase inicial de calentamiento.
-
Importancia del calentamiento controlado:
- Una velocidad de calentamiento excesiva (superior a 10°C/min) puede provocar sinterización insuficiente y grados de sinterización desiguales en todo el material.Esto da lugar a picos de fusión a alta temperatura y a un aumento de la cristalinidad, lo que puede comprometer la integridad estructural de la alúmina.
- El calentamiento controlado garantiza una sinterización uniforme y evita tensiones internas que podrían provocar grietas o roturas.
-
Consideraciones sobre la velocidad de enfriamiento:
- La velocidad de enfriamiento debe ser inferior a 10°C/min con 5°C/min siendo lo ideal.El enfriamiento rápido puede causar choque térmico que conducen al fallo del material.
- El enfriamiento gradual es esencial para mantener la integridad estructural de la alúmina, especialmente después de tratamientos a alta temperatura.
-
Sensibilidad al choque térmico:
- La alúmina es muy sensible a los choques térmicos debido a su fragilidad.Los cambios rápidos de temperatura pueden provocar grietas o roturas.
- Se recomienda un ritmo de calentamiento y enfriamiento más lento (por ejemplo, 150-300°C por hora para el calentamiento y 75-150°C por hora para el enfriamiento) para mitigar este riesgo.
-
Recomendaciones específicas para cada aplicación:
- Para tubos para hornos de alúmina Las velocidades de calentamiento y enfriamiento deben ajustarse a los requisitos de diseño y funcionamiento del horno.Debe evitarse el enfriamiento natural tras el tratamiento térmico, ya que puede provocar rápidas caídas de temperatura y posibles daños.
- En hornos tubulares rotativos En el proceso de tratamiento térmico influyen factores como el ángulo de inclinación, la velocidad de rotación, la longitud del tubo y las propiedades de flujo del material.El ajuste de estos parámetros puede ayudar a mantener velocidades óptimas de calentamiento y enfriamiento.
-
Propiedades y durabilidad del material:
- La alúmina tiene una excelente resistencia al choque térmico, alta densidad y resistencia al ácido, álcali y erosión.Estas propiedades la hacen adecuada para aplicaciones de alta temperatura (hasta 1800°C).
- Unas tasas de calentamiento y enfriamiento adecuadas garantizan la durabilidad del material y prolongan su vida útil.
-
Consejos prácticos para usuarios de equipos:
- Establezca siempre una velocidad de enfriamiento controlada en el programa del horno; evite detener el programa bruscamente a altas temperaturas.
- Utilice cambios graduales de temperatura para evitar el estrés térmico y garantizar un rendimiento constante del material.
- Supervise de cerca el proceso de calentamiento y enfriamiento, especialmente durante las fases de calentamiento inicial y enfriamiento final.
Siguiendo estas directrices, los usuarios pueden optimizar el rendimiento y la longevidad de los componentes de alúmina en entornos de alta temperatura, garantizando resultados consistentes y minimizando el riesgo de fallo del material.
Tabla resumen:
Parámetro | Recomendación |
---|---|
Velocidad de calentamiento | 5-10°C/min (preferiblemente 5°C/min) |
Velocidad de calentamiento inicial | 150-300°C por hora durante las primeras 1-1,5 horas |
Velocidad de enfriamiento | Inferior a 10°C/min (idealmente 5°C/min) |
Sensibilidad al choque térmico | Evite los cambios bruscos de temperatura para evitar grietas y roturas |
Ventaja clave | Garantiza una sinterización uniforme, durabilidad y longevidad en entornos de alta temperatura |
¿Necesita ayuda para optimizar su proceso de tratamiento térmico de alúmina? Póngase en contacto con nuestros expertos para obtener soluciones a medida.