La soldadura fuerte y la soldadura fuerte son procesos de unión de metales que implican fundir un metal de aportación para unir dos o más piezas de metal. Sin embargo, difieren significativamente en términos de temperatura, resistencia y aplicaciones. La soldadura suele realizarse a temperaturas más bajas (por debajo de 450 °C) y utiliza metales de aportación más blandos, como aleaciones de estaño, plomo o plata, lo que la hace adecuada para componentes eléctricos y electrónicos delicados. La soldadura fuerte, por otro lado, implica temperaturas más altas (por encima de 450 °C) y utiliza metales de aportación más fuertes como el latón o el bronce, lo que da como resultado uniones más robustas y adecuadas para aplicaciones de servicio pesado. La elección entre los dos depende de los materiales que se unen, la resistencia requerida de la unión y el entorno operativo.
Puntos clave explicados:
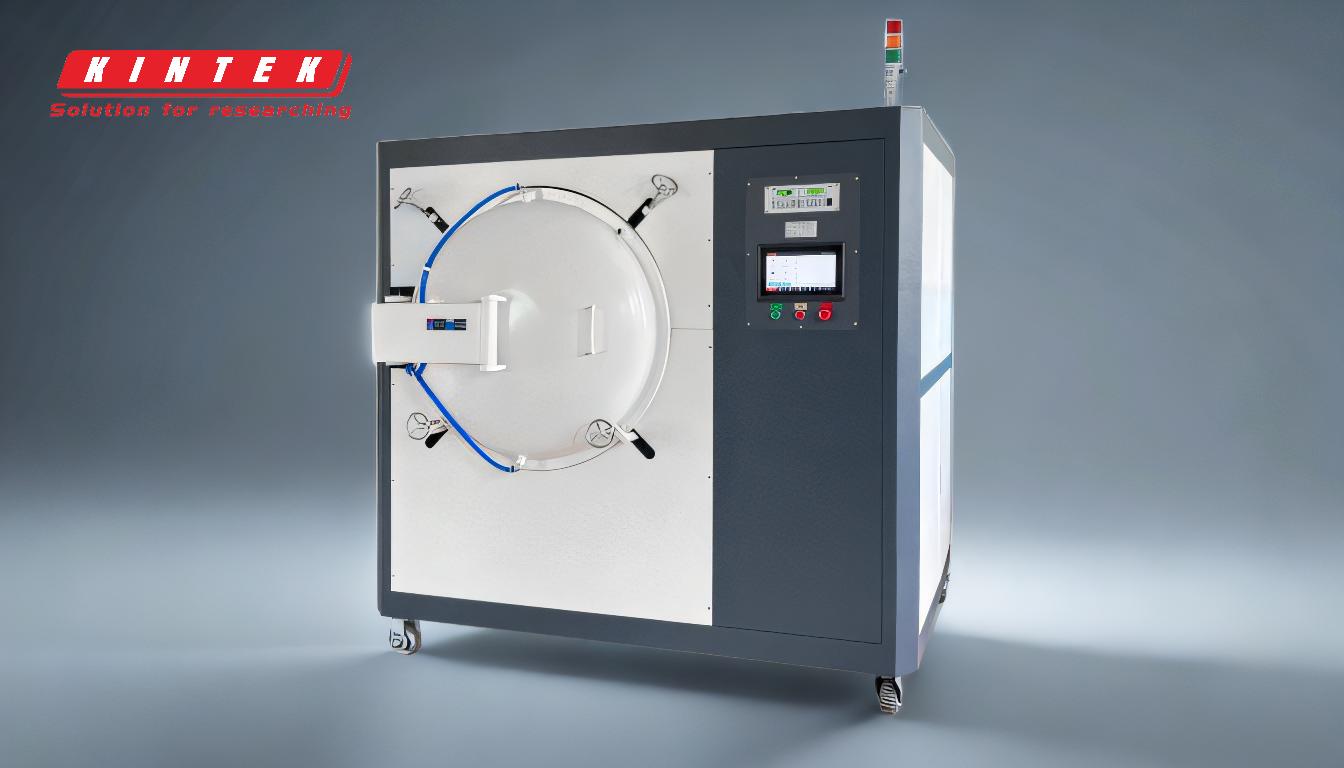
-
Rango de temperatura:
- Soldadura: Ocurre a temperaturas inferiores a 450°C. Esta temperatura más baja lo hace ideal para unir componentes delicados, como los que se encuentran en la electrónica, donde el calor elevado podría dañar las piezas.
- Soldadura: Tiene lugar a temperaturas superiores a 450°C, llegando frecuentemente hasta 900°C. La temperatura más alta permite uniones más fuertes y es adecuada para unir materiales más pesados o robustos.
-
Metales de aporte:
- Soldadura: Utiliza metales de aportación más blandos, como aleaciones de estaño y plomo o soldaduras a base de plata. Estos materiales tienen puntos de fusión más bajos y es más fácil trabajar con ellos en aplicaciones de precisión.
- Soldadura: Emplea metales de aportación más fuertes como latón, bronce o aleaciones a base de níquel. Estos materiales proporcionan mayor resistencia y durabilidad a las juntas, lo que los hace adecuados para aplicaciones estructurales.
-
Fuerza conjunta:
- Soldadura: Produce uniones que generalmente son más débiles en comparación con las uniones soldadas. Esto es aceptable para aplicaciones donde la resistencia mecánica no es crítica, como en electrónica o plomería.
- Soldadura: Crea uniones más fuertes debido al mayor punto de fusión y a los metales de aportación más fuertes. Esto hace que la soldadura fuerte sea ideal para aplicaciones que requieren alta resistencia mecánica, como en componentes automotrices o aeroespaciales.
-
Aplicaciones:
- Soldadura: Se utiliza comúnmente en electrónica, plomería y joyería. Su proceso a baja temperatura es ventajoso para trabajos delicados y materiales que no soportan altas temperaturas.
- Soldadura: Preferido en industrias que requieren uniones fuertes y duraderas, como sistemas HVAC, fabricación de automóviles y maquinaria pesada. La temperatura más alta y los metales de aporte más resistentes lo hacen adecuado para entornos exigentes.
-
Técnicas de proceso:
- Soldadura: A menudo implica el uso de un soldador o un soplete. El fundente generalmente se aplica para limpiar las superficies y mejorar el flujo del metal de aportación.
- Soldadura: Requiere más calor, a menudo proporcionado por un soplete de gas o un horno. El fundente también se utiliza en soldadura fuerte para evitar la oxidación y garantizar una unión limpia.
-
Compatibilidad de materiales:
- Soldadura: Funciona bien con una amplia gama de metales, incluidos cobre, latón y oro. Es particularmente eficaz para unir metales diferentes.
- Soldadura: Adecuado para unir metales similares o diferentes, incluidos acero, acero inoxidable y hierro fundido. El proceso es versátil y se puede utilizar con una variedad de combinaciones de metales.
-
Costo y equipo:
- Soldadura: Generalmente es menos costoso y requiere equipo más simple, como un soldador o un soplete pequeño. Esto lo hace accesible tanto para aplicaciones profesionales como de bricolaje.
- Soldadura: Requiere equipos más especializados, como sopletes u hornos de alta temperatura, lo que puede aumentar el costo. Sin embargo, la inversión está justificada para aplicaciones que requieren uniones de alta resistencia.
En resumen, las principales diferencias entre la soldadura fuerte y la soldadura fuerte radican en la temperatura, los metales de aportación, la resistencia de las uniones y las aplicaciones. La soldadura es ideal para trabajos delicados y a baja temperatura, mientras que la soldadura fuerte es más adecuada para uniones duraderas y de alta resistencia en entornos más exigentes. La elección entre los dos depende de los requisitos específicos del proyecto, incluidos los materiales involucrados y la resistencia deseada de la junta.
Tabla resumen:
Aspecto | Soldadura | Soldadura |
---|---|---|
Rango de temperatura | Por debajo de 450°C | Por encima de 450°C (hasta 900°C) |
Metales de aporte | Metales más blandos como aleaciones de estaño-plomo o plata. | Metales más fuertes como latón, bronce o aleaciones a base de níquel. |
Fuerza conjunta | Uniones más débiles, adecuadas para aplicaciones delicadas | Uniones más fuertes, ideales para aplicaciones de servicio pesado |
Aplicaciones | Electrónica, fontanería, joyería. | Sistemas HVAC, fabricación de automóviles, maquinaria pesada. |
Equipo | Soldador o soplete pequeño | Antorcha u horno de alta temperatura |
Costo | Equipo más simple y de menor costo | Mayor costo, equipo especializado. |
¿Necesita ayuda para elegir entre soldar y soldar para su proyecto? ¡Póngase en contacto con nuestros expertos hoy!