Los hornos de inducción se utilizan ampliamente en aplicaciones industriales para calentar y fundir metales debido a su eficacia, precisión y respeto por el medio ambiente.La potencia de un horno de inducción es un factor crítico que determina su rendimiento, capacidad e idoneidad para tareas específicas.La potencia nominal de los hornos de inducción suele oscilar entre 15 kW y 90 kW en los modelos compactos, pero puede variar en función de la aplicación, el tipo de material y los resultados deseados.El consumo energético de los hornos de inducción para acero, por ejemplo, es de unos 625 kWh/tonelada.Varios factores influyen en los requisitos de potencia, como el material que se procesa, el tiempo de calentamiento, la productividad, la temperatura y el peso de la pieza.Funciones avanzadas como la conversión de frecuencia IGBT, los sistemas de protección integral y la transmisión eficaz del calor mejoran aún más el rendimiento del horno, convirtiéndolo en una herramienta versátil y fiable para los procesos industriales.
Explicación de los puntos clave:
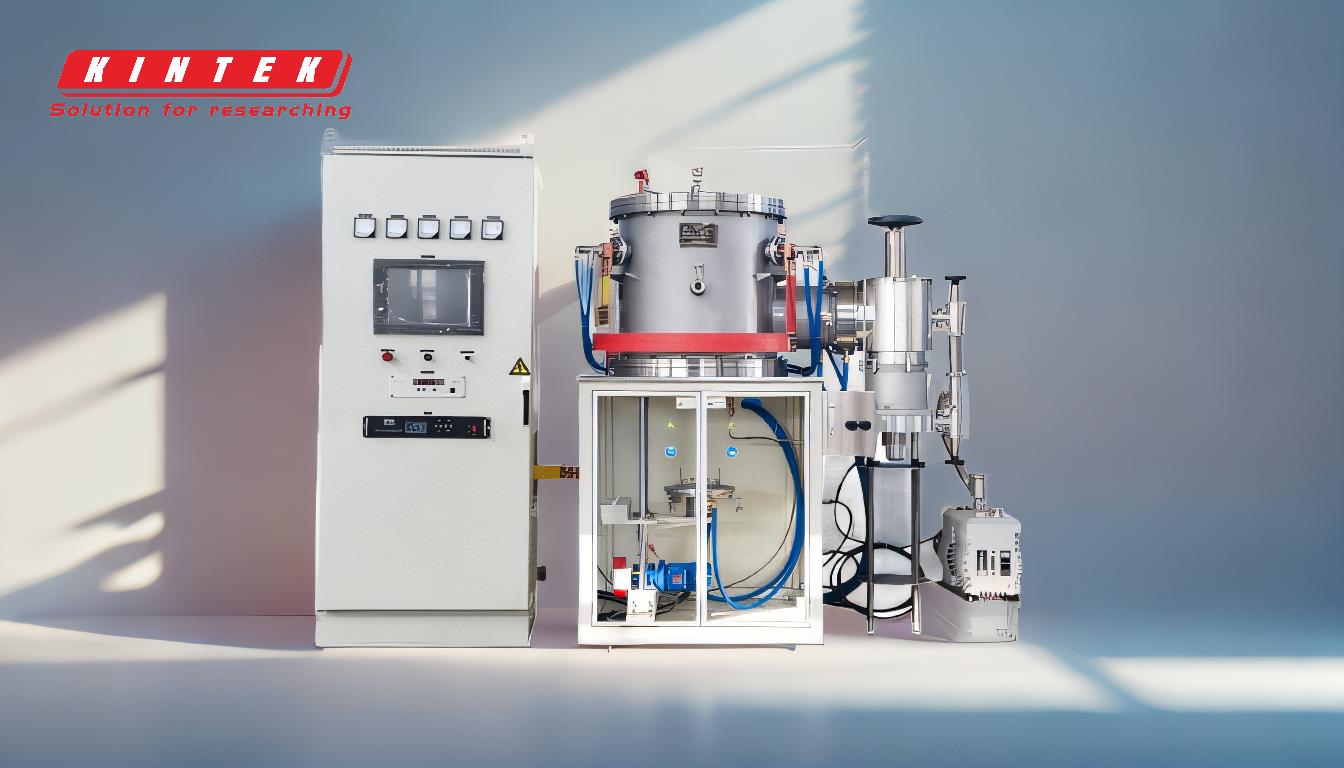
-
Gama de potencias de los hornos de inducción
- Los hornos de inducción suelen tener una potencia nominal que oscila entre 15 kW a 90 kW para los modelos compactos.Esta gama es adecuada para operaciones de pequeña y mediana envergadura, como fundir metales o calentar piezas.
- La potencia está directamente relacionada con la capacidad y el rendimiento del horno.Las potencias más elevadas permiten un calentamiento y una fusión más rápidos, por lo que son ideales para entornos de alta productividad.
-
Factores que influyen en el cálculo de la potencia
-
La potencia necesaria para un horno de inducción depende de varios factores:
- Tipo de material:Los distintos materiales tienen propiedades térmicas diferentes, que afectan a la energía necesaria para calentar o fundir.
- Tiempo de calentamiento:Un calentamiento más rápido requiere una mayor potencia de entrada.
- Productividad:Las operaciones de alto rendimiento exigen más potencia para mantener una producción constante.
- Temperatura de calentamiento:Las temperaturas más elevadas, como 1800°C para la fusión, requieren más potencia.
- Peso de la pieza:Las piezas más grandes o pesadas necesitan más energía para alcanzar la temperatura deseada.
- Estos factores se basan en años de experiencia industrial para garantizar unos cálculos de potencia precisos y un rendimiento óptimo del horno.
-
La potencia necesaria para un horno de inducción depende de varios factores:
-
Consumo de energía estándar
- Para los hornos de inducción de acero, el consumo de energía estándar es de 625 kWh/tonelada .Esta métrica proporciona un punto de referencia para la eficiencia energética y ayuda a estimar los costes operativos.
- Las funciones de ahorro de energía, como la conversión de frecuencia IGBT y los sistemas de control de circuito de potencia constante, contribuyen a reducir el consumo de energía al tiempo que mantienen la uniformidad de la fundición y el calentamiento.
-
Funciones avanzadas que mejoran la eficiencia energética
- Conversión de frecuencia IGBT:Los hornos de inducción modernos utilizan tecnología IGBT de estado sólido para una regulación de potencia y una conversión de frecuencia eficientes.Esto garantiza un funcionamiento estable y reduce el derroche de energía.
- Sistemas de protección integral:Funciones como la protección contra sobrecorriente, falta de agua, sobrecalentamiento, sobretensión, cortocircuito y pérdida de fase mejoran la seguridad y la fiabilidad.
- Transmisión y uniformidad del calor:El horno garantiza una buena transmisión del calor y una distribución uniforme de la temperatura, minimizando la pérdida de energía y mejorando la eficacia del proceso.
- Agitación magnética:El campo magnético de frecuencia media proporciona agitación magnética, lo que mejora la uniformidad de la composición y la eliminación de la espuma, aumentando aún más la eficiencia.
-
Eficiencia y flexibilidad operativas
- Los hornos de inducción están diseñados para fundición continua las 24 horas del día lo que las hace adecuadas para aplicaciones industriales de alta demanda.
- Son ligeras, móviles y compactas y ocupan menos de un metro cuadrado, lo que facilita su integración en las instalaciones existentes.
- Los cuerpos de los hornos pueden sustituirse fácilmente para adaptarse a distintos pesos, materiales y métodos de arranque, lo que proporciona flexibilidad para diversas aplicaciones.
-
Capacidades de temperatura
- Los hornos de inducción pueden alcanzar temperaturas de 1800°C o más dependiendo del acoplamiento inductivo de la bobina con los materiales de carga.Esto las hace adecuadas para fundir una amplia gama de metales, incluidos los que tienen puntos de fusión elevados.
- La temperatura de calentamiento de la forja puede alcanzar 1250°C mientras que la temperatura de fusión puede alcanzar 1650°C garantizando la versatilidad para diferentes procesos industriales.
-
Eficiencia energética y ventajas medioambientales
- Los hornos de inducción son ahorran energía y respetan el medio ambiente reduciendo los costes operativos y minimizando el impacto medioambiental.
- Características como los sistemas de control del circuito de potencia constante y la exploración automática de frecuencias garantizan un funcionamiento suave y estable, mejorando aún más la eficiencia energética.
-
Ventajas de diseño y mantenimiento
- El diseño de circuito integrado de alta simplifica la depuración y el funcionamiento, haciendo que el horno sea fácil de usar.
- Los componentes del armario de alimentación, como los contactores de CA, los rectificadores controlados por silicio y las tarjetas de inversor, están bien coordinados, lo que garantiza un mantenimiento sencillo y una fiabilidad a largo plazo.
-
Consideraciones específicas de la aplicación
- El velocidad de fusión y la configuración de potencia de la fuente de alimentación de media frecuencia son fundamentales para lograr los resultados deseados.
- El uso de una carga limpia y una longitud adecuada del bloque del horno mejoran la eficiencia, mientras que los materiales refractarios adecuados, como los crisoles de cuarzo, reducen el consumo de transferencia de calor.
En conclusión, la potencia de un horno de inducción es un factor determinante de su rendimiento, eficacia e idoneidad para aplicaciones industriales específicas.Comprendiendo los factores que influyen en los requisitos de potencia y aprovechando las funciones avanzadas, los usuarios pueden optimizar el funcionamiento del horno, reducir costes y conseguir resultados uniformes y de alta calidad.
Tabla resumen:
Aspecto clave | Detalles |
---|---|
Gama de potencia | De 15 kW a 90 kW para los modelos compactos |
Consumo de energía (acero) | 625 kWh/tonelada |
Capacidades de temperatura | Hasta 1800°C para fusión, 1250°C para forja |
Características avanzadas | Conversión de frecuencia IGBT, agitación magnética, amplios sistemas de protección |
Eficiencia operativa | Fundición continua las 24 horas, peso ligero y diseño compacto |
Eficiencia energética | Ahorro de energía, respeto del medio ambiente y reducción de los costes operativos |
¿Está listo para optimizar su proceso de calentamiento industrial? Póngase en contacto con nosotros para encontrar el horno de inducción perfecto para sus necesidades.