Los hornos de inducción son capaces de alcanzar temperaturas extremadamente altas. La temperatura máxima exacta depende de factores como el diseño del horno, los materiales que se funden y el tipo de refractario utilizado.En general, los hornos de inducción pueden alcanzar temperaturas comprendidas entre 1.600 °C (2.900 °F) y 2.000 °C (3.632 °F) o más.Sin embargo, el límite superior práctico suele estar determinado por los materiales utilizados en la construcción del horno, como el revestimiento refractario, que puede degradarse a temperaturas muy elevadas.En condiciones al aire libre, la temperatura más alta que se suele alcanzar es de unos 3300 °F (1815 °C) para fundir platino.El acoplamiento inductivo entre la bobina y los materiales de carga también desempeña un papel fundamental en la determinación de la temperatura alcanzable.
Explicación de los puntos clave:
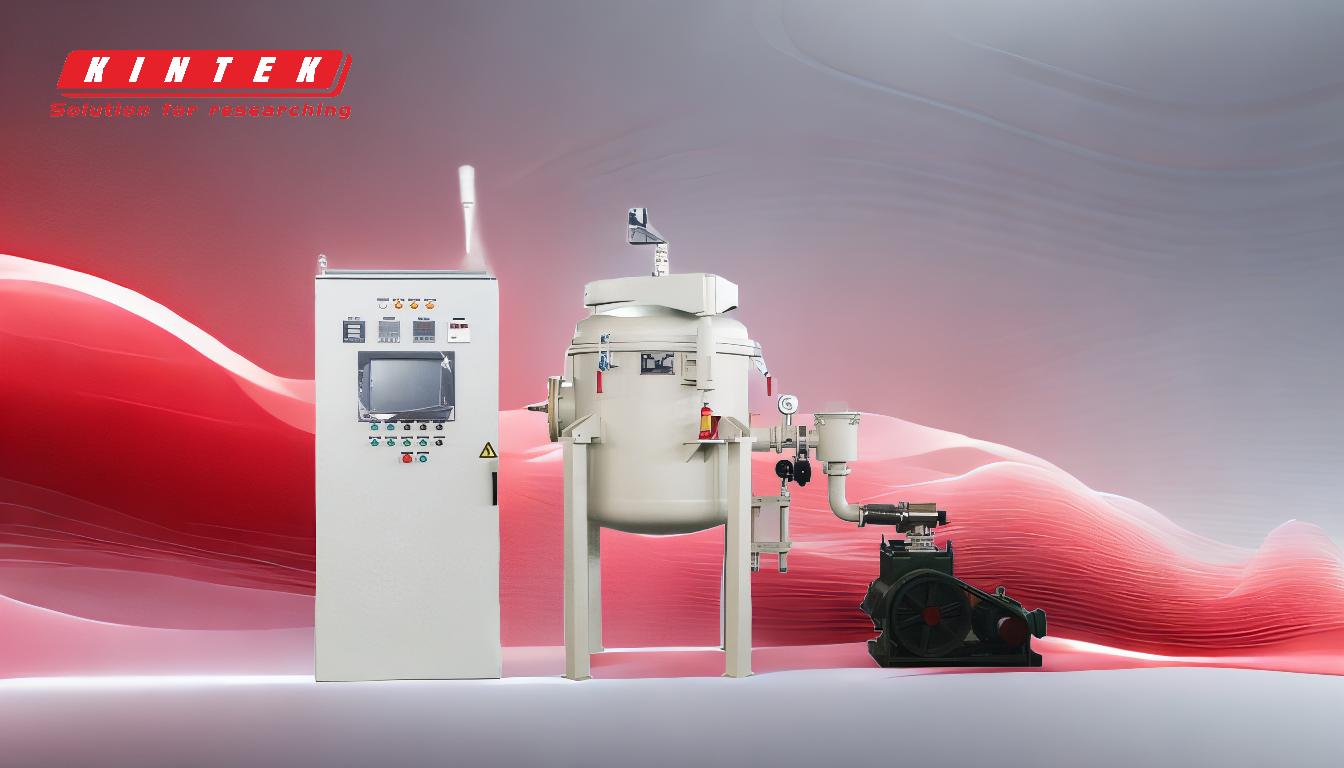
-
Gama de temperaturas de los hornos de inducción:
- Los hornos de inducción pueden alcanzar temperaturas entre 1600°C (2900°F) y 2000°C (3632°F) o superiores, según el diseño y la aplicación.
- Estas temperaturas son suficientes para fundir una amplia gama de metales, como acero, hierro, cobre e incluso platino.
-
Factores que influyen en la temperatura máxima:
- Acoplamiento inductivo:La eficacia de la transferencia de calor entre la bobina de inducción y los materiales de carga afecta a la temperatura máxima alcanzable.Un mejor acoplamiento permite alcanzar temperaturas más elevadas.
- Materiales refractarios:El revestimiento refractario del horno tiene un límite de temperatura a partir del cual se degrada.Esto limita la temperatura superior práctica en muchos casos.
- Material que se funde:Los distintos materiales tienen diferentes puntos de fusión, y el horno debe ser capaz de alcanzar esas temperaturas.Por ejemplo, el platino requiere temperaturas de hasta 3300°F (1815°C) .
-
Limitaciones prácticas:
- Degradación refractaria:A temperaturas muy elevadas, el revestimiento refractario puede romperse, limitando la vida útil del horno.
- Condiciones al aire libre:En entornos al aire libre, la temperatura más alta que se suele alcanzar es de unos 3300°F (1815°C) para fundir platino, debido a la oxidación y otros factores ambientales.
-
Pequeños hornos de inducción:
- Los hornos de inducción más pequeños, utilizados a menudo para aplicaciones de laboratorio o a pequeña escala, suelen tener una temperatura máxima de calentamiento de 1600°C (2900°F) .Estos hornos están diseñados para la precisión y el control más que para aplicaciones extremas de alta temperatura.
-
Aplicaciones industriales:
- En entornos industriales, los hornos de inducción se utilizan para fundir metales como el acero, el hierro y el cobre, que requieren temperaturas en el rango de 1500°C a 2000°C .
- La capacidad de alcanzar temperaturas tan elevadas hace que los hornos de inducción sean ideales para aplicaciones que requieren un control preciso de la temperatura y un calentamiento rápido.
-
Ventajas de los hornos de inducción:
- Eficiencia:Los hornos de inducción son muy eficaces gracias al calentamiento directo del material de carga, lo que reduce el derroche de energía.
- Control:Ofrecen un control preciso de la temperatura, lo que es crucial para las aplicaciones que requieren propiedades específicas de los materiales.
- Limpieza:El calentamiento por inducción es un proceso limpio, con una contaminación mínima del material fundido.
-
Consideraciones para los compradores:
- Al elegir un horno de inducción, el comprador debe tener en cuenta la temperatura máxima requerida para su aplicación específica.
- El tipo de material refractario utilizado en el horno debe ser compatible con la temperatura de funcionamiento prevista para garantizar la durabilidad y el rendimiento.
- El tamaño y la potencia del horno deben ajustarse a la escala de la operación, ya sea para uso en laboratorios a pequeña escala o para producción industrial a gran escala.
En resumen, los hornos de inducción son versátiles y capaces de alcanzar temperaturas extremadamente altas, lo que los hace adecuados para una amplia gama de aplicaciones.Sin embargo, la temperatura máxima alcanzable depende de factores como el acoplamiento inductivo, los materiales refractarios y la aplicación específica.Los compradores deben considerar cuidadosamente estos factores al seleccionar un horno de inducción para asegurarse de que satisface sus necesidades.
Cuadro sinóptico:
Aspecto | Detalles |
---|---|
Temperatura | 1600°C (2900°F) a 2000°C (3632°F) o superior |
Factores clave que influyen | Acoplamiento inductivo, materiales refractarios y material fundido |
Limitaciones prácticas | Degradación del refractario, condiciones al aire libre (máx. ~3300°F para el platino) |
Hornos pequeños | Temperatura máxima1600°C (2900°F), ideal para precisión y control |
Aplicaciones industriales | Fundición de acero, hierro, cobre (1500°C a 2000°C) |
Ventajas | Alta eficiencia, control preciso y proceso de calentamiento limpio |
Consideraciones de compra | Adapte el tamaño, la potencia y los materiales refractarios del horno a las necesidades de la aplicación |
¿Está listo para encontrar el horno de inducción perfecto para sus necesidades? Póngase en contacto con nosotros para recibir asesoramiento experto.