Los hornos de tratamiento térmico, aunque son esenciales para diversos procesos industriales, presentan varios inconvenientes que pueden afectar a su eficiencia, coste y eficacia operativa.Entre ellos se encuentran los problemas relacionados con el control de la temperatura, la intensidad de la mano de obra, el consumo de energía y las limitaciones operativas específicas según el tipo de horno.Comprender estos inconvenientes es crucial para tomar decisiones informadas a la hora de seleccionar y operar hornos de tratamiento térmico.
Explicación de los puntos clave:
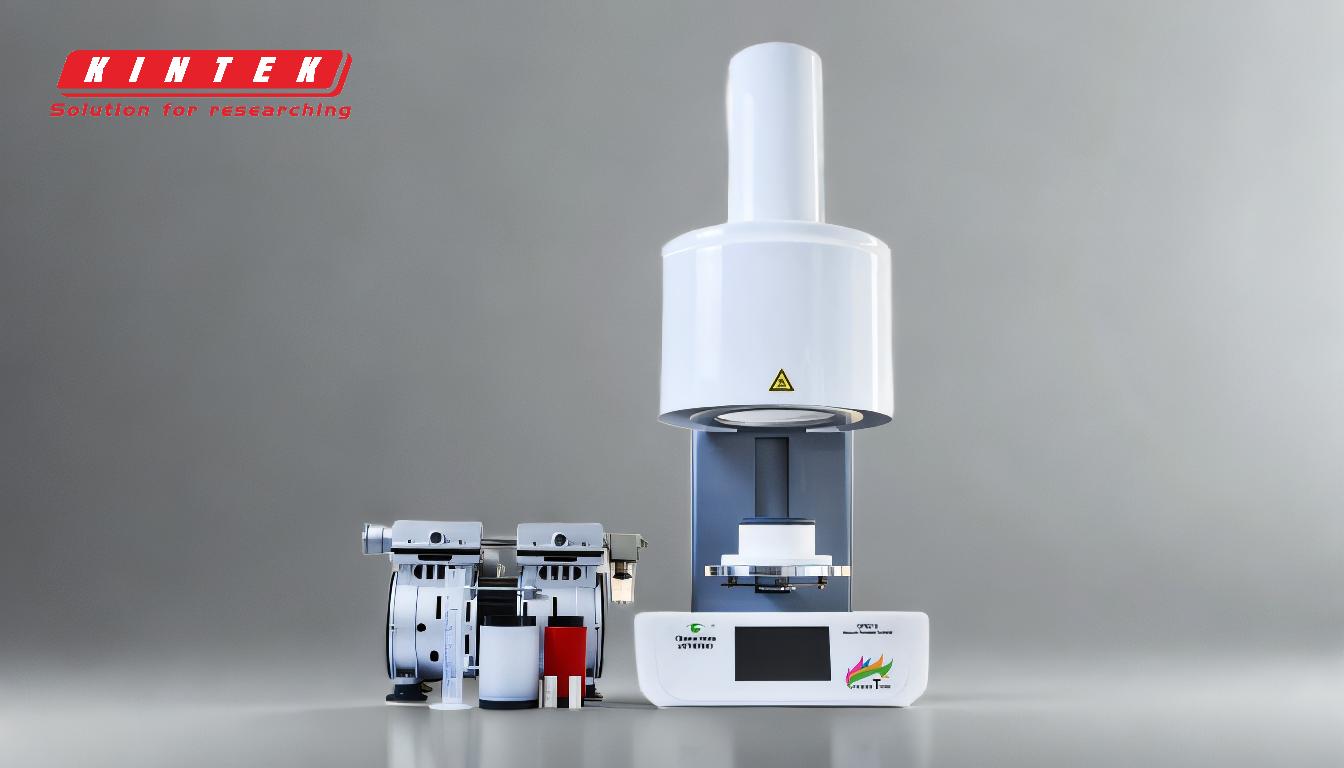
-
Control deficiente de la temperatura:
- Muchos hornos de tratamiento térmico, especialmente los que utilizan carbón o combustibles líquidos, tienen dificultades para mantener una distribución uniforme de la temperatura dentro de la cámara.Esto puede dar lugar a resultados de tratamiento térmico desiguales, lo que afecta a la calidad del producto final.Por ejemplo, los hornos de carbón suelen tener un control deficiente de la temperatura, lo que puede provocar un calentamiento desigual y posibles defectos en los materiales tratados.
-
Trabajo intensivo:
- Ciertos tipos de hornos, como los hornos discontinuos, requieren una importante mano de obra para cargar y descargar los materiales.Esto no sólo aumenta los costes operativos, sino que también reduce la productividad global.Los hornos discontinuos, por ejemplo, necesitan accesorios como cestas o bastidores para agrupar las piezas, y las piezas más cercanas a la fuente de calor se calientan más rápido, lo que provoca un calentamiento desigual de toda la carga.
-
Alto consumo de energía:
- La eficiencia energética de los hornos de tratamiento térmico puede ser un problema.Por ejemplo, los hornos discontinuos requieren calentar no sólo las piezas, sino también los carros o cestas utilizados para sostenerlas, lo que aumenta la carga térmica total y el consumo de energía.Del mismo modo, los hornos de mufla tardan más en alcanzar la temperatura deseada que los métodos de llama abierta, lo que los hace menos eficientes energéticamente para proyectos que requieren calentamientos rápidos.
-
Limitaciones operativas:
- Los distintos tipos de hornos plantean retos operativos específicos.Los hornos de inducción, por ejemplo, carecen de capacidad de refinado, por lo que requieren que los materiales de carga estén libres de óxidos y tengan una composición conocida.Algunos elementos de aleación pueden perderse debido a la oxidación, por lo que es necesario volver a añadirlos a la masa fundida.Los hornos de tratamiento térmico en atmósfera controlada tienen elevados requisitos de estanqueidad y necesitan componentes especializados, como ladrillos anticarburación y placas de resistencias de gran sección, lo que aumenta la complejidad y el coste de funcionamiento.
-
Costes de mantenimiento y equipamiento:
- Los costes de mantenimiento y equipamiento inicial de algunos hornos pueden ser prohibitivos.Los hornos de sinterización por prensado en caliente, por ejemplo, requieren un funcionamiento y un mantenimiento profesionales, y garantizar la uniformidad y la estabilidad de la presión durante el proceso es crucial para evitar defectos en el producto.Además, los elevados requisitos de sellado y los componentes especializados de los hornos de atmósfera controlada contribuyen a aumentar sus costes.
-
Almacenamiento y manipulación:
- El almacenamiento y la manipulación de los materiales utilizados en los hornos de tratamiento térmico pueden plantear problemas.Los hornos de carbón, por ejemplo, requieren carbón de la calidad adecuada para un uso eficaz, y su almacenamiento puede ser problemático debido a su volumen y a la posibilidad de que se produzcan humos.Los combustibles líquidos, por su parte, se espesan en invierno, lo que exige un calentamiento especial de las tuberías para garantizar su buen funcionamiento.
-
Limitaciones de diseño:
- El diseño de ciertos hornos puede limitar su accesibilidad y facilidad de uso.Los hornos de mufla, por ejemplo, tienen un diseño que dificulta el acceso al interior, lo que requiere una cuidadosa colocación del material durante su uso.Esto puede ralentizar el proceso y hacerlo menos ideal para proyectos que requieran un calentamiento rápido.
En resumen, aunque los hornos de tratamiento térmico son indispensables para diversas aplicaciones industriales, presentan varias desventajas que hay que tener muy en cuenta.Entre ellos figuran los relacionados con el control de la temperatura, la intensidad de la mano de obra, el consumo de energía, las limitaciones operativas, los costes de mantenimiento, el almacenamiento y la manipulación, y las limitaciones de diseño.Comprender estos inconvenientes puede ayudar a seleccionar el horno adecuado para aplicaciones específicas y a optimizar su funcionamiento para mitigar estos retos.
Cuadro sinóptico:
Desventaja | Descripción |
---|---|
Control deficiente de la temperatura | Calentamiento desigual y resultados inconsistentes, especialmente en hornos basados en carbón o combustible líquido. |
Trabajo intensivo | La carga y descarga manual en hornos discontinuos aumenta los costes y reduce la productividad. |
Elevado consumo de energía | Aumento de la carga térmica y del consumo de energía, especialmente en hornos discontinuos y de mufla. |
Restricciones operativas | Retos específicos como la capacidad de refinado, la oxidación y los requisitos de sellado. |
Costes de mantenimiento y equipamiento | Costes elevados de funcionamiento profesional, mantenimiento y componentes especializados. |
Problemas de almacenamiento y manipulación | Problemas de almacenamiento del carbón, espesamiento del combustible líquido y manipulación del material. |
Limitaciones de diseño | Accesibilidad limitada y procesos más lentos, especialmente en hornos de mufla. |
¿Necesita ayuda para seleccionar el horno de tratamiento térmico adecuado? Póngase en contacto con nuestros expertos para obtener soluciones a medida.