La sinterización de materiales cerámicos es un proceso crítico que transforma la cerámica en polvo en una estructura densa y sólida mediante un tratamiento térmico por debajo del punto de fusión.Este proceso consta de varias etapas, como la preparación del polvo compacto, el calentamiento para eliminar los aglutinantes y la sinterización a alta temperatura para fusionar las partículas.Las variables clave que influyen en la sinterización son la temperatura, la atmósfera, la presión y el tamaño de las partículas, que determinan las propiedades finales del material, como la resistencia, la porosidad y la densidad.El proceso de sinterización puede optimizarse controlando estos parámetros para conseguir las características deseadas en el producto cerámico final.
Explicación de los puntos clave:
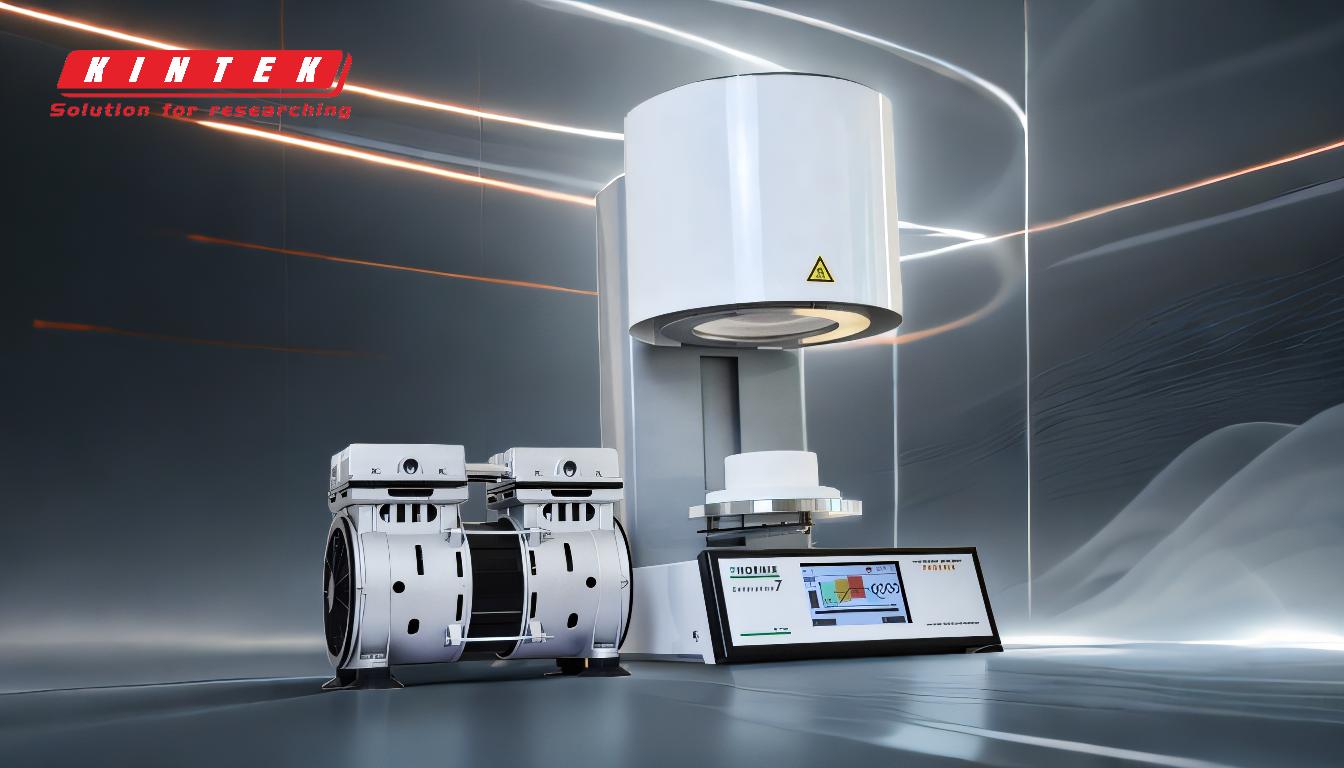
-
Preparación del Polvo Compacto:
- Mezclado y formación de la pasta: El proceso comienza mezclando polvo cerámico sin cocer con agua, aglutinantes y defloculantes para formar una lechada.A continuación, esta pasta se seca por pulverización para obtener un polvo fluido.
- Prensado en un cuerpo verde: El polvo secado por pulverización se prensa en un molde para formar un "cuerpo verde", que es una pieza cerámica con forma pero sin cocer.Este paso es crucial para conseguir la forma deseada y la densidad inicial.
-
Eliminación del ligante:
- Calentamiento a baja temperatura: El cuerpo verde se calienta a baja temperatura para quemar el aglutinante.Este paso es esencial para evitar defectos en el producto final, ya que los aglutinantes residuales pueden causar porosidad o grietas durante la sinterización a alta temperatura.
-
Sinterización a alta temperatura:
- Calentamiento justo por debajo del punto de fusión: El cuerpo verde se calienta a una temperatura elevada, justo por debajo del punto de fusión del material cerámico.Este paso permite que las partículas se difundan y se unan, reduciendo la porosidad y aumentando la densidad.
- Fusión y densificación de partículas: Durante la sinterización, las partículas se densifican y se fusionan, lo que puede acelerarse utilizando técnicas como la sinterización en fase líquida (LPS).El proceso implica la difusión de material desde las superficies de las partículas hasta los puntos de contacto entre ellas, lo que conduce a la formación de cuellos y, finalmente, a la fusión.
-
Enfriamiento y solidificación:
- Enfriamiento controlado: Tras la sinterización, el material se enfría de forma controlada para solidificarse en una masa unificada.La velocidad de enfriamiento puede influir en la microestructura final y en las propiedades de la cerámica.
-
Factores que influyen en la sinterización
- Temperatura: Las temperaturas más altas suelen aumentar la velocidad de sinterización y mejorar las propiedades del material, como la resistencia a la tracción y la energía de impacto.Sin embargo, las temperaturas excesivas pueden provocar un crecimiento indeseado del grano.
- Atmósfera: La atmósfera de sinterización (por ejemplo, aire, vacío o gases inertes como argón o nitrógeno) puede afectar al estado de oxidación de la cerámica y a la velocidad de difusión de las partículas.
- La presión: La aplicación de presión durante la sinterización puede mejorar la reorganización de las partículas y reducir la porosidad, lo que da lugar a un producto final más denso.
- Tamaño y composición de las partículas: Las partículas más pequeñas y las composiciones homogéneas favorecen una mejor densificación y una sinterización más uniforme.La elección del proceso de sinterización y de los parámetros depende de las propiedades deseadas del producto cerámico final.
-
Optimización del proceso de sinterización:
- Control de los parámetros: El proceso de sinterización puede optimizarse controlando cuidadosamente parámetros como la temperatura de sinterización, la presión aplicada y la atmósfera gaseosa.Los polvos más finos y las temperaturas más altas pueden aumentar la compactación, pero la cantidad de fase líquida debe controlarse cuidadosamente para evitar defectos.
- Porosidad final: La porosidad final de la cerámica sinterizada depende de la porosidad inicial del compacto verde, así como de la temperatura y duración del proceso de sinterización.Las cerámicas de óxido puro, por ejemplo, requieren tiempos de sinterización más largos y temperaturas más altas debido a la difusión en estado sólido.
Comprendiendo y controlando estos aspectos clave, los fabricantes pueden producir materiales cerámicos de alta calidad con propiedades adaptadas a diversas aplicaciones.
Tabla resumen:
Etapa | Proceso clave | Finalidad |
---|---|---|
Preparación del polvo | Mezcla de polvo cerámico con aglutinantes, agua y defloculantes para formar una lechada. | Crea un polvo fluido para dar forma. |
Formación del cuerpo verde | Prensado del polvo en un molde para formar una pieza cerámica sin cocer. | Consigue la forma deseada y la densidad inicial. |
Eliminación de ligantes | Calentamiento a baja temperatura para quemar los aglutinantes. | Evita defectos como la porosidad o el agrietamiento durante la sinterización. |
Sinterización a alta temperatura | Calentamiento justo por debajo del punto de fusión para fundir partículas. | Reduce la porosidad y aumenta la densidad mediante la difusión de partículas. |
Enfriamiento | Enfriamiento controlado para solidificar el material. | Influye en la microestructura y las propiedades finales. |
Variables clave | Temperatura, atmósfera, presión y tamaño de las partículas. | Determina las propiedades finales del material, como la resistencia y la porosidad. |
Optimice su proceso de sinterización de cerámica para obtener resultados superiores. contacte hoy mismo con nuestros expertos ¡!