Los hornos de resistencia, aunque son muy eficientes y versátiles, presentan varias desventajas que los usuarios deben tener en cuenta.Entre ellos, el elevado consumo de energía, el aumento de los costes relacionados con la distribución de energía y la electricidad, y los problemas de aislamiento a altas temperaturas.Además, la necesidad de una cuidadosa colocación del material y la posibilidad de que los materiales refractarios conduzcan la electricidad a temperaturas elevadas son inconvenientes notables.Estos factores pueden repercutir en el coste global y la eficacia del uso de hornos de resistencia en diversas aplicaciones industriales.
Explicación de los puntos clave:
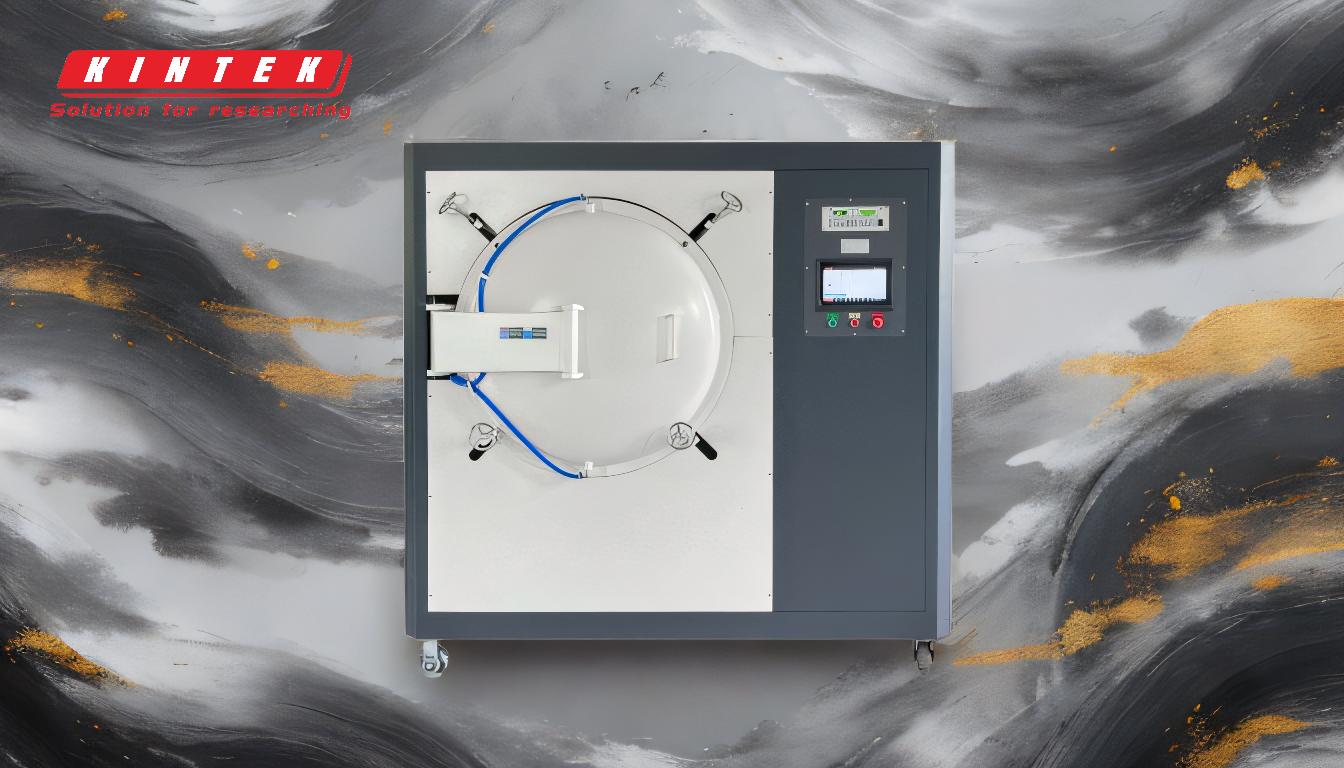
-
Alto consumo de energía:
- Los hornos de resistencia son conocidos por su elevado consumo de energía.Esto puede suponer un aumento de los costes operativos, especialmente en instalaciones en las que el horno se utiliza mucho.La elevada demanda de energía también puede requerir mejoras en los sistemas de distribución de energía existentes, lo que aumenta los costes iniciales de instalación.
-
Aumento de los costes:
- Equipos de distribución de energía:La necesidad de aumentar la capacidad de los equipos de distribución de energía para hacer frente a la elevada demanda de potencia de los hornos de resistencia puede incrementar significativamente los costes iniciales de instalación.
- Costes de electricidad:El coste continuo de la electricidad puede ser considerable, sobre todo en regiones donde los precios de la electricidad son elevados.Esto puede hacer que, a largo plazo, los hornos de resistencia resulten menos económicos que otros métodos de calefacción.
-
Problemas de aislamiento a altas temperaturas:
- Cuando la temperatura de calentamiento supera los 1000°C, los materiales refractarios utilizados en los hornos de resistencia pueden empezar a conducir la electricidad.Esto exige una atención especial al aislamiento para evitar riesgos de seguridad y garantizar un funcionamiento eficaz.La necesidad de materiales aislantes especializados puede incrementar aún más los costes.
-
Colocación y accesibilidad de los materiales:
- Al igual que los hornos de mufla, los hornos de resistencia pueden plantear problemas de colocación de materiales y accesibilidad.El diseño del horno puede dificultar el acceso al interior, lo que requiere una colocación cuidadosa de los materiales para garantizar un calentamiento uniforme y evitar daños.
-
Comparación con otros tipos de hornos:
- Hornos de mufla:Aunque los hornos de mufla también tienen su propio conjunto de desventajas, como tiempos de calentamiento más largos y problemas de accesibilidad, pueden ser más adecuados para ciertas aplicaciones en las que no se requieren calentamientos rápidos.
- Hornos de inducción:Por otra parte, los hornos de inducción carecen de capacidad de refinado y exigen que los materiales de carga estén exentos de óxidos y tengan una composición conocida.Esto puede limitar su uso en aplicaciones en las que es necesario el refinado.
En resumen, aunque los hornos de resistencia ofrecen un alto rendimiento térmico y buenas condiciones de trabajo, su elevado consumo de energía, el aumento de los costes y los problemas de aislamiento a altas temperaturas son desventajas significativas que deben tenerse muy en cuenta.Estos factores pueden influir en el coste global y la eficiencia del uso de hornos de resistencia en diversas aplicaciones industriales.
Cuadro sinóptico:
Desventaja | Detalles |
---|---|
Alto consumo de energía | Provoca un aumento de los costes operativos y puede requerir actualizaciones del sistema eléctrico. |
Mayores costes | Mayores costes de instalación y de electricidad. |
Retos del aislamiento | Los materiales refractarios pueden conducir la electricidad a temperaturas superiores a 1000°C. |
Colocación del material | Requiere una colocación cuidadosa para un calentamiento uniforme y accesibilidad. |
Comparación con otros hornos | Los hornos de mufla y de inducción tienen diferentes pros y contras. |
¿Necesita ayuda para elegir el horno adecuado a sus necesidades? Póngase en contacto con nuestros expertos para un asesoramiento personalizado.