Un horno de inducción es un sistema de fusión de gran eficacia y precisión que se utiliza principalmente en procesos metalúrgicos.Su construcción gira en torno a tres componentes principales: una fuente de alimentación, una bobina de inducción y un crisol de materiales refractarios.La fuente de alimentación genera una corriente alterna de alta frecuencia que fluye a través de la bobina de inducción, creando un campo magnético que se invierte rápidamente.Este campo magnético induce corrientes de Foucault en la carga metálica colocada en el interior del crisol, generando calor por resistencia y fundiendo el metal.El crisol, fabricado con materiales no conductores y resistentes al calor, contiene la carga metálica, que actúa como el devanado secundario de un transformador.Todo el sistema está diseñado para garantizar que el calor se genere directamente dentro del metal, minimizando la pérdida de energía y proporcionando un control preciso del proceso de fusión.
Explicación de los puntos clave:
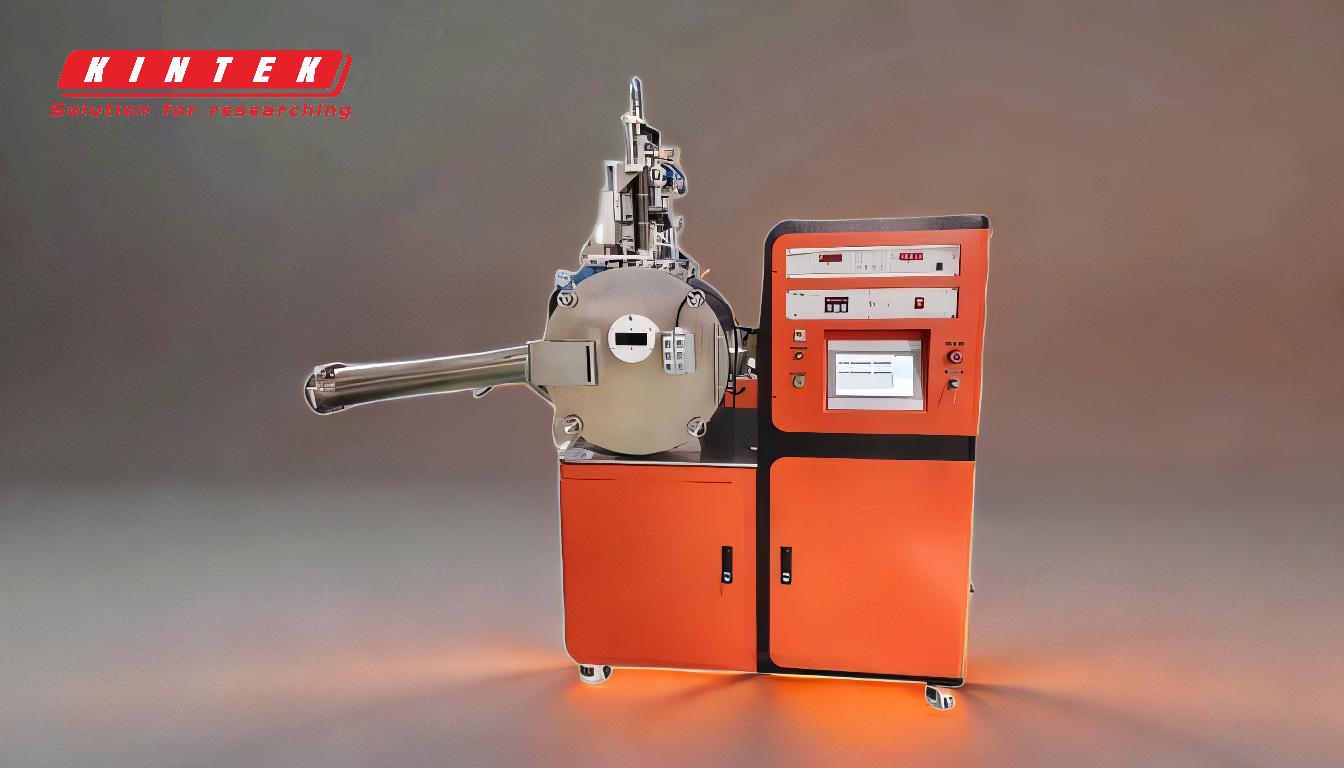
-
Fuente de alimentación:
- La fuente de alimentación es el corazón del horno de inducción, ya que suministra la corriente alterna (CA) necesaria para el proceso de inducción.
- Genera CA de alta frecuencia, esencial para crear el campo magnético de inversión rápida.
- La frecuencia de la corriente alterna puede variar en función de la aplicación: las frecuencias más altas suelen utilizarse en hornos pequeños y las más bajas en hornos grandes.
- La fuente de alimentación debe ser robusta y fiable para garantizar un rendimiento constante y hacer frente a las elevadas demandas de energía del proceso de fusión.
-
Bobina de inducción:
- La bobina de inducción, generalmente de tubo de cobre hueco, rodea el crisol y transporta la corriente alterna desde la fuente de alimentación.
- La bobina está diseñada para crear un campo magnético fuerte y uniforme que penetra en la carga metálica del crisol.
- El diseño hueco del tubo de cobre permite la refrigeración por agua, necesaria para evitar el sobrecalentamiento de la bobina debido a las altas corrientes que la atraviesan.
- El número de espiras y la geometría de la bobina se calculan cuidadosamente para optimizar el campo magnético y garantizar un calentamiento eficaz de la carga metálica.
-
Crisol:
- El crisol es un recipiente fabricado con materiales refractarios, como la cerámica o el grafito, que pueden soportar temperaturas extremadamente altas y no son conductores.
- Contiene la carga metálica, que es el material que se va a fundir, como acero, hierro, aluminio u otros metales.
- El crisol se coloca dentro de la bobina de inducción, y la carga metálica actúa como el devanado secundario de un transformador, donde se inducen las corrientes de Foucault.
- El diseño del crisol debe garantizar que pueda contener el metal fundido sin degradarse ni reaccionar con el metal, manteniendo la pureza de la masa fundida.
-
Carga metálica:
- La carga metálica es el material que se va a fundir dentro del crisol.
- Cuando el campo magnético alterno de la bobina de inducción penetra en la carga metálica, induce corrientes de Foucault en el metal.
- Estas corrientes de Foucault generan calor a través de la resistencia del metal, provocando su fusión.
- La carga metálica actúa como el devanado secundario de un transformador, mientras que la bobina de inducción es el devanado primario.
-
Sistema de refrigeración:
- La bobina de inducción, debido a las altas corrientes que la atraviesan, genera un calor importante y requiere refrigeración para evitar daños.
- Un sistema de refrigeración, normalmente con agua, circula por los tubos de cobre huecos de la bobina de inducción para disipar el calor.
- Una refrigeración adecuada es esencial para mantener la eficiencia y la longevidad del horno de inducción.
-
Sistema de control:
- Los hornos de inducción modernos están equipados con sofisticados sistemas de control que permiten regular con precisión el proceso de fusión.
- Estos sistemas supervisan y controlan parámetros como la temperatura, la potencia de entrada y la velocidad de enfriamiento, garantizando unos resultados uniformes y de alta calidad.
- El sistema de control también ofrece funciones de seguridad, como la protección contra sobretemperatura y la detección de fallos, para evitar accidentes y daños en el equipo.
-
Ventajas de los hornos de inducción:
- Eficiencia energética:Los hornos de inducción generan calor directamente dentro de la carga metálica, lo que minimiza la pérdida de energía y los hace muy eficientes.
- Precisión:La capacidad de controlar con precisión el proceso de fusión permite producir aleaciones con composiciones y propiedades exactas.
- Limpieza:Dado que el calor se genera dentro del metal, la contaminación procedente de fuentes externas es mínima, lo que da lugar a fusiones más limpias.
- Velocidad:Los hornos de inducción pueden fundir metales muy rápidamente, reduciendo los tiempos de producción y aumentando el rendimiento.
En resumen, la construcción de un horno de inducción es una sofisticada integración de componentes eléctricos y mecánicos diseñados para fundir metales con eficacia y precisión.La fuente de alimentación, la bobina de inducción y el crisol trabajan en armonía para crear un entorno controlado en el que el calor se genera directamente dentro de la carga metálica, lo que garantiza una gran eficacia, precisión y limpieza en el proceso de fusión.La inclusión de un sistema de refrigeración y de mecanismos de control avanzados mejora aún más el rendimiento y la seguridad del horno, convirtiéndolo en una herramienta esencial en las aplicaciones metalúrgicas modernas.
Tabla resumen:
Componente | Función |
---|---|
Fuente de alimentación | Genera corriente alterna de alta frecuencia para crear un campo magnético para el calentamiento por inducción. |
Bobina de inducción | Transporta corriente alterna, crea un campo magnético e induce corrientes de Foucault en el metal. |
Crisol | Contiene la carga metálica y soporta altas temperaturas sin degradarse. |
Carga metálica | Actúa como el devanado secundario de un transformador, generando calor al fundirse. |
Sistema de refrigeración | Evita el sobrecalentamiento de la bobina de inducción mediante refrigeración por agua. |
Sistema de control | Regula la temperatura, la potencia y la refrigeración para un funcionamiento preciso y seguro. |
Ventajas | Eficiencia energética, precisión, limpieza y capacidad de fusión rápida. |
¿Está preparado para optimizar su proceso de fusión de metales? Póngase en contacto con nosotros para saber más sobre los hornos de inducción