Consideraciones generales para el sputtering de magnetrón
Mantenimiento del entorno de vacío
El sputtering por magnetrón requiere un entorno de vacío impecablemente mantenido para evitar los efectos perjudiciales de las impurezas transportadas por el aire sobre la calidad de la película. El entorno de vacío no es un mero telón de fondo, sino un componente crítico que garantiza la integridad y precisión del proceso de sputtering.
En los hornos de vacío, los componentes mecánicos, como juntas y uniones soldadas, se someten a un mantenimiento riguroso para mantener el vacío sin fugas. Este meticuloso mantenimiento es esencial porque incluso las fugas más pequeñas pueden comprometer los niveles de vacío, afectando así a la calidad del producto final. El proceso de identificación y rectificación de estas fugas requiere mucho tiempo y trabajo, lo que subraya la importancia del mantenimiento preventivo.
Además, la contaminación de los componentes internos del horno puede proceder de diversas fuentes, como gases residuales y partículas, que pueden infiltrarse en el sistema durante las actividades de mantenimiento. Dicha contaminación puede dar lugar a propiedades de la película incoherentes, lo que requiere una limpieza exhaustiva y protocolos de validación para garantizar que el entorno de vacío permanezca impoluto.
Aspecto del mantenimiento | Importancia |
---|---|
Integridad del sello | Garantiza un vacío sin fugas; fundamental para mantener los niveles de vacío operativos. |
Juntas de soldadura | Requieren inspección y mantenimiento periódicos para evitar fugas. |
Componentes internos del horno | Deben mantenerse libres de contaminación para mantener la calidad de la película. |
En resumen, el mantenimiento del entorno de vacío es una piedra angular del proceso de sputtering por magnetrón, que exige una atención meticulosa a los detalles y medidas preventivas rigurosas para garantizar la producción de películas de alta calidad.
Control de la velocidad de deposición
La velocidad de deposición es un parámetro crítico en el proceso de sputtering por magnetrón, que influye significativamente tanto en la calidad como en el espesor de la película. Esta velocidad determina la rapidez con la que el material del blanco se transfiere al sustrato, lo que afecta a la uniformidad, la densidad y las propiedades finales de la película depositada.
Para obtener resultados óptimos, la velocidad de deposición debe controlarse meticulosamente y ajustarse en función de las condiciones específicas. Factores como el tipo de material de destino, el espesor deseado de la película y las propiedades específicas requeridas para la aplicación influyen a la hora de determinar la velocidad de deposición adecuada. Por ejemplo, una velocidad de deposición más alta puede ser adecuada para aplicaciones que requieren películas más gruesas, pero también podría provocar problemas como una adhesión deficiente o falta de uniformidad si no se gestiona correctamente.
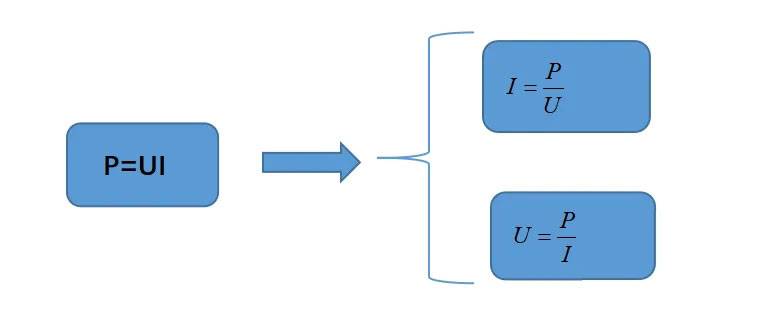
Factor | Impacto en la velocidad de deposición |
---|---|
Material objetivo | Los distintos materiales tienen diferentes rendimientos de sputtering, lo que afecta a la velocidad de deposición. |
Temperatura del sustrato | Las temperaturas más altas pueden mejorar la adherencia de la película, pero también pueden alterar la velocidad de deposición. |
Potencia del sputtering | El aumento de la potencia suele traducirse en una mayor velocidad de deposición, pero debe equilibrarse con otros parámetros. |
En resumen, el control preciso de la velocidad de deposición es esencial para producir películas de PZT de alta calidad. Este control garantiza que la película no sólo cumpla las especificaciones de espesor requeridas, sino que también presente las propiedades deseadas, como la conductividad eléctrica y la resistencia mecánica.
Control de la potencia y el tiempo de sputtering
La potencia y el tiempo de sputtering son parámetros críticos que influyen significativamente en la calidad de la película. Estos factores deben ajustarse meticulosamente para adaptarlos a las características y requisitos específicos del material que se va a procesar. El nivel de potencia durante el sputtering afecta a la energía impartida al material objetivo, que a su vez determina la velocidad a la que los átomos son expulsados y depositados sobre el sustrato. Los niveles de potencia más elevados suelen dar lugar a velocidades de deposición más rápidas, pero también pueden provocar un aumento del calor y de la tensión en el sustrato, lo que puede causar defectos o alterar las propiedades deseadas de la película.
Por el contrario, la duración del proceso de sputtering, o tiempo de sputtering, influye directamente en el grosor y la uniformidad de la película depositada. Los tiempos de sputtering prolongados pueden producir películas más gruesas, pero también aumentan el riesgo de contaminación y la probabilidad de obtener espesores no uniformes en todo el sustrato. Por lo tanto, es esencial equilibrar la potencia y el tiempo de sputtering para conseguir una calidad óptima de la película.
Para ilustrar la importancia de estos parámetros, considere la siguiente tabla:
Potencia de sputtering (W) | Tiempo de sputtering (min) | Espesor de la película (nm) | Calidad de la película (clasificación 1-10) |
---|---|---|---|
100 | 30 | 200 | 8 |
150 | 20 | 250 | 7 |
200 | 15 | 300 | 6 |
En este ejemplo, aunque una mayor potencia y unos tiempos más cortos dan lugar a películas más gruesas, la calidad de la película disminuye debido al aumento de la tensión y a los posibles defectos. Así pues, la selección de la potencia y el tiempo de sputtering adecuados es un proceso matizado que requiere una cuidadosa consideración tanto de las propiedades del material como de las características deseadas de la película.
Material objetivo y preparación de la superficie
Selección del material objetivo adecuado
La selección del material del cátodo es un paso crítico en el proceso de sputtering por magnetrón, ya que influye significativamente en la calidad y el rendimiento de la película resultante. La elección del material afecta directamente a la composición química, la integridad estructural y las propiedades funcionales de la película depositada. Por lo tanto, es esencial seleccionar un material objetivo que se ajuste a los requisitos específicos y a los resultados deseados de la película.
A la hora de elegir un material de destino, deben tenerse en cuenta varios factores:
-
Composición química: El material de destino debe coincidir con la composición química deseada de la película. Por ejemplo, en la preparación de películas de titanato de circonato de plomo (PZT), lo ideal es que el blanco consista en una mezcla homogénea de óxidos de plomo, circonio y titanio.
-
Pureza: Una elevada pureza del material objetivo es crucial para evitar la introducción de impurezas en la película, que pueden degradar sus propiedades. Cualquier contaminante puede provocar defectos, reducir la densidad de la película y afectar a su rendimiento general.
-
Propiedades físicas: Las propiedades físicas del cátodo, como su densidad y conductividad térmica, pueden influir en el proceso de sputtering y en las características de la película resultante. Por ejemplo, un cátodo más denso suele dar lugar a una tasa de deposición más uniforme.
-
Estado de la superficie: La superficie del material objetivo debe ser lisa y estar libre de defectos para garantizar un sputtering eficaz y uniforme. Pueden ser necesarios tratamientos superficiales para conseguir la planitud y limpieza requeridas.
La tabla siguiente resume las consideraciones clave para seleccionar un material de cátodo adecuado:
Consideración | Importancia |
---|---|
Composición química | Garantiza las propiedades químicas deseadas de la película. |
Pureza | Evita la contaminación y mantiene la calidad de la película. |
Propiedades físicas | Influye en la eficacia del sputtering y en la uniformidad de la película. |
Estado de la superficie | Garantiza un sputtering eficaz y uniforme, evitando defectos en la película. |
En resumen, la selección del material del cátodo es una decisión polifacética que requiere una cuidadosa consideración de diversos factores para conseguir películas de alta calidad y alto rendimiento.
Garantizar la pureza y planitud de la superficie del cátodo
La pureza y planitud de la superficie del cátodo son factores críticos que influyen significativamente en el proceso de sputtering y en la calidad de la película resultante. Cualquier impureza o irregularidad en la superficie del cátodo puede provocar inconsistencias en la deposición de la película de PZT, afectando a su rendimiento y uniformidad generales.
Para garantizar unos resultados óptimos, la superficie del cátodo debe someterse a rigurosos protocolos de tratamiento e inspección. Esto implica
-
Limpieza de la superficie: Eliminar cualquier contaminante, como polvo, aceites u óxidos, que pueda comprometer la pureza del blanco. Normalmente se emplean técnicas como la limpieza por ultrasonidos, el grabado químico y la limpieza por haz de iones.
-
Inspección de planitud: Utilización de herramientas de metrología avanzada, como perfilómetros e interferómetros, para medir la topografía de la superficie. Cualquier desviación de la planitud deseada debe corregirse mediante pulido u otras medidas correctoras.
Tratamiento de superficies | Finalidad | Técnicas comunes |
---|---|---|
Limpieza de superficies | Eliminar contaminantes | Limpieza ultrasónica, grabado químico, limpieza por haz de iones |
Inspección de planitud | Verificar la uniformidad de la superficie | Perfilómetros, interferómetros |
Siguiendo meticulosamente estos procedimientos, se puede garantizar la pureza y planitud de la superficie objetivo, mejorando así la calidad y consistencia de la película de PZT producida mediante pulverización catódica por magnetrón.
Control del sustrato y del entorno
Control de la temperatura del sustrato
La temperatura del sustrato desempeña un papel fundamental en la determinación de las propiedades finales de la película depositada, como la cristalinidad, la densidad y la rugosidad de la superficie. Estas propiedades son críticas para el rendimiento y la funcionalidad de la película, por lo que el control preciso de la temperatura es un aspecto esencial del proceso de sputtering por magnetrón.
Cuando la temperatura del sustrato es demasiado baja, la película puede presentar una cristalinidad deficiente y una densidad baja, lo que aumenta la rugosidad de la superficie. Por el contrario, si la temperatura es demasiado alta, puede provocar cambios de fase no deseados o incluso daños térmicos en el sustrato. Por lo tanto, la temperatura debe ajustarse meticulosamente en función de las características y requisitos específicos del material depositado.
Por ejemplo, en el caso de las películas de titanato de circonato de plomo (PZT), la temperatura óptima del sustrato puede variar significativamente en función de la estructura de fase y las propiedades ferroeléctricas deseadas. Normalmente, se utilizan temperaturas que oscilan entre 400 °C y 600 °C para conseguir la fase de perovskita deseada y una respuesta piezoeléctrica óptima.
Para garantizar un control preciso, los sistemas de sputtering modernos suelen incorporar mecanismos avanzados de supervisión y control de la temperatura, como termómetros de infrarrojos y controladores PID. Estas herramientas permiten realizar ajustes en tiempo real, garantizando que la temperatura del sustrato se mantenga dentro del rango óptimo durante todo el proceso de deposición.
Rango de temperatura | Propiedades de la película |
---|---|
< 400°C | Escasa cristalinidad, baja densidad, alta rugosidad |
400°C - 600°C | Fase perovskita deseada, respuesta piezoeléctrica óptima |
> 600°C | Posibles cambios de fase, daños térmicos |
En resumen, el control de la temperatura del sustrato es un parámetro crítico en el proceso de sputtering por magnetrón, que influye directamente en la calidad y el rendimiento de la película depositada. Una gestión adecuada de la temperatura garantiza que la película cumpla las especificaciones requeridas y mejora su funcionalidad general.
Control del vacío y la atmósfera
El proceso de sputtering para preparar capas de película de titanato de circonato de plomo (PZT) es muy sensible a las condiciones ambientales. Para obtener resultados óptimos, debe realizarse en un entorno de alto vacío meticulosamente controlado. Este estricto requisito no es negociable, ya que influye directamente en la integridad y el rendimiento de la película de PZT.
En un entorno de alto vacío, la ausencia de gases atmosféricos reduce significativamente el riesgo de contaminación. Las partículas suspendidas en el aire, la humedad y otras impurezas pueden introducir defectos en la película, comprometiendo sus propiedades estructurales y eléctricas. Al mantener el vacío, se eliminan eficazmente estos posibles contaminantes, garantizando una superficie de deposición prístina.
Además, el control de las condiciones atmosféricas va más allá del mero mantenimiento del vacío. También implica evitar la oxidación, que puede alterar la composición química de la película de PZT. La oxidación puede provocar variaciones en la estequiometría de la película, lo que afecta a sus propiedades ferroeléctricas y piezoeléctricas. Por lo tanto, mantener una atmósfera controlada es crucial para preservar las características químicas y físicas deseadas de la película de PZT.
Para lograr y mantener este entorno de alto vacío, se emplean sistemas de vacío avanzados. Estos sistemas incluyen bombas de alta eficiencia, detectores de fugas y sensores de presión que trabajan conjuntamente para mantener el nivel de vacío requerido. La supervisión y calibración periódicas de estos sistemas son esenciales para garantizar un control del vacío continuo y fiable.
En resumen, garantizar el control del vacío y la atmósfera es un aspecto crítico del proceso de sputtering por magnetrón para la preparación de películas de PZT. No sólo protege contra la contaminación y la oxidación, sino que también garantiza la consistencia y la calidad de la película depositada. Este meticuloso control es la piedra angular de todo el proceso, y es la base del éxito en la fabricación de películas de PZT de alto rendimiento.
Control de la uniformidad
La uniformidad es una propiedad crítica de las películas finas, especialmente en el contexto de la preparación de películas de titanato de circonato de plomo (PZT) mediante pulverización catódica por magnetrón. Lograr una deposición uniforme de la película es esencial para garantizar un rendimiento y una fiabilidad constantes en todo el sustrato. Esta uniformidad se consigue principalmente mediante un control meticuloso del proceso de pulverización catódica, en el que intervienen varios parámetros y técnicas clave.
En primer lugar, la posición y orientación tanto de la fuente de sputtering como del sustrato desempeñan un papel fundamental para conseguir una deposición uniforme de la película. La fuente de pulverización catódica, normalmente un material objetivo, debe colocarse a una distancia óptima del sustrato para garantizar que los átomos o partículas expulsados del objetivo se distribuyan uniformemente por la superficie. Además, el ángulo con el que estas partículas se desplazan hasta el sustrato debe controlarse cuidadosamente para evitar cualquier sesgo direccional en el proceso de deposición.
En segundo lugar, el empleo de técnicas avanzadas como la rotación del sustrato puede mejorar significativamente la uniformidad. Al rotar el sustrato durante el proceso de sputtering, la deposición de la película se distribuye de forma más uniforme, mitigando los efectos de cualquier variación localizada en la salida de la fuente de sputtering. Este método garantiza que cada parte del sustrato reciba una cantidad constante de material, lo que da lugar a una película final más uniforme.
Parámetro de control | Impacto en la uniformidad |
---|---|
Posición de la fuente de sputtering | Garantiza una distribución uniforme de las partículas |
Ángulo del sustrato | Evita el sesgo direccional en la deposición |
Rotación del sustrato | Mejora la distribución uniforme del material |
En resumen, lograr la uniformidad en la deposición de películas finas requiere una combinación de control preciso sobre la fuente de sputtering y el sustrato, así como el uso estratégico de técnicas como la rotación del sustrato. Estas medidas contribuyen colectivamente a la producción de películas de PZT uniformes y de alta calidad, esenciales para las aplicaciones previstas.
Supervisión del proceso y tratamiento posterior
Control y ajuste de la potencia de sputtering
La potencia de sputtering es un parámetro crítico en el proceso de sputtering por magnetrón, que influye significativamente en el espesor y la composición de la película depositada. El nivel de potencia afecta directamente a la energía de los iones que bombardean el material objetivo, lo que a su vez determina la velocidad a la que el material es expulsado y depositado sobre el sustrato. Por ejemplo, una mayor potencia de pulverización catódica suele acelerar la velocidad de deposición, pero también puede aumentar la rugosidad y la falta de uniformidad de la película si no se controla adecuadamente.
Para garantizar una calidad óptima de la película, es esencial controlar y ajustar dinámicamente la potencia de sputtering. Esto implica el uso de sistemas de monitorización avanzados que puedan proporcionar datos en tiempo real sobre los niveles de potencia, las velocidades de deposición y las propiedades de la película. Mediante la correlación de estos parámetros, los operarios pueden ajustar la potencia de sputtering para conseguir las características deseadas de la película. Por ejemplo, si el grosor de la película se desvía del objetivo, la potencia de sputtering puede ajustarse para compensar, garantizando un grosor de capa uniforme en todo el sustrato.
Además, la potencia de sputtering puede influir en la composición de la película. Diferentes niveles de potencia pueden provocar distintos grados de pulverización catódica de diferentes elementos dentro de un blanco multicomponente, lo que provoca cambios en la estequiometría de la película. Por lo tanto, es necesario un control preciso de la potencia de pulverización catódica para mantener la composición química deseada de la película. Esto es especialmente importante en la preparación de películas de óxido complejas como la de titanato de circonato de plomo (PZT), en la que mantener la proporción correcta de plomo, circonio y titanio es crucial para conseguir las propiedades eléctricas y mecánicas deseadas.
En resumen, la supervisión y el ajuste de la potencia de sputtering no sólo consisten en controlar la velocidad de deposición, sino también en lograr el equilibrio adecuado de grosor, uniformidad y composición en la película. Este control dinámico garantiza que el producto final cumpla los estrictos requisitos de las aplicaciones en electrónica, óptica y otros campos de alta tecnología.
Tratamiento posterior de la película
Los procesos de postratamiento son pasos cruciales en la preparación de películas de titanato de circonato de plomo (PZT), destinados a mejorar sus propiedades y garantizar su estabilidad a largo plazo. Estos tratamientos suelen incluirrecocido yoxidaciónque están diseñados para refinar la microestructura de la película y mejorar sus características mecánicas y eléctricas.
Recocido
El recocido consiste en calentar la película a una temperatura determinada y, a continuación, enfriarla lentamente. Este proceso puede
- Aumentar la cristalinidad: Al favorecer el crecimiento de cristales más grandes y uniformes, el recocido puede mejorar significativamente la integridad estructural de la película.
- Reducir la tensión: Las tensiones internas de la película pueden aliviarse, lo que da lugar a un material más estable y duradero.
- Mejora de las propiedades eléctricas: La constante dieléctrica y las propiedades ferroeléctricas de la película pueden optimizarse mediante un recocido controlado.
Oxidación
Oxidar la película implica exponerla a un entorno rico en oxígeno, lo que puede:
- Estabilizar la capa de óxido: Garantizar que la capa de óxido de la superficie de la película sea uniforme y estable puede evitar problemas como la delaminación y la degradación con el paso del tiempo.
- Mejorar la resistencia química: Una superficie oxidada es menos susceptible a los ataques químicos, lo que hace que la película sea más robusta en diversos entornos.
- Control de la rugosidad de la superficie: La oxidación puede ayudar a suavizar las irregularidades de la superficie de la película, mejorando su calidad y rendimiento generales.
Tanto el recocido como la oxidación son fundamentales en el postratamiento, ya que no sólo abordan los problemas de calidad inmediatos, sino que también contribuyen al rendimiento y la fiabilidad de la película a largo plazo.
Control de calidad y pruebas
Las películas preparadas se someten a rigurosos controles de calidad y pruebas para garantizar que cumplen los estrictos requisitos necesarios para las aplicaciones previstas. Este proceso implica múltiples facetas, cada una de ellas evaluada meticulosamente para garantizar la integridad y el rendimiento de las películas.
Parámetros clave para el control de calidad
-
Morfología de la superficie: La superficie de la película se examina con microscopios de alta resolución para detectar defectos como grietas, agujeros o irregularidades. Este paso es crucial, ya que las imperfecciones de la superficie pueden afectar significativamente a la funcionalidad de la película.
-
Medición del espesor: El grosor de la película se mide con instrumentos de precisión como elipsómetros o perfilómetros. La consistencia del grosor es esencial para que las propiedades eléctricas y mecánicas de la película sean uniformes.
-
Análisis de la composición: La composición química de la película se analiza mediante técnicas como la difracción de rayos X (DRX) y la espectroscopia de rayos X de energía dispersiva (EDS). De este modo se garantiza que la composición de la película coincida con la estequiometría deseada, que es fundamental para el uso previsto.
-
Propiedades eléctricas: Las pruebas eléctricas, que incluyen mediciones de resistividad, capacitancia y constante dieléctrica, se realizan para evaluar el rendimiento de la película en aplicaciones eléctricas. Estas propiedades están directamente influenciadas por la estructura y la composición de la película.
Métodos e instrumentos de prueba
Parámetro | Método de prueba | Instrumento utilizado |
---|---|---|
Morfología de la superficie | Microscopía | Microscopio electrónico de barrido (SEM) |
Medición del espesor | Técnicas ópticas y mecánicas | Elipsómetro, Perfilómetro |
Análisis de composición | Técnicas espectroscópicas | Difracción de rayos X (DRX), EDS |
Propiedades eléctricas | Medidas eléctricas | Medidor LCR, analizador de impedancia |
Mediante la evaluación sistemática de estos parámetros, el proceso de control de calidad asegura que cada película cumple las normas predefinidas, garantizando así la fiabilidad y el rendimiento del producto final.
Mejora continua y consideraciones medioambientales
Mejora continua y optimización
La preparación de películas finas es un proceso iterativo que exige un escrutinio y un perfeccionamiento continuos para lograr resultados óptimos. El proceso de preparación, desde la configuración inicial hasta el producto final, requiere un análisis y una mejora meticulosos para aumentar tanto la calidad como la eficacia de la película. Este perfeccionamiento continuo implica varios aspectos clave:
-
Supervisión de los parámetros del proceso: Es esencial controlar y ajustar periódicamente parámetros críticos como la potencia de sputtering, la velocidad de deposición y la temperatura del sustrato. Estos parámetros influyen significativamente en las propiedades de la película, como su grosor, uniformidad y calidad general.
-
Actualizaciones tecnológicas: La incorporación de tecnologías y metodologías avanzadas puede dar lugar a mejoras sustanciales. Por ejemplo, el uso de sistemas automatizados de supervisión y control en tiempo real puede reducir los errores humanos y mejorar la coherencia del proceso.
-
Control de calidad: Es indispensable aplicar medidas rigurosas de control de calidad. Esto incluye pruebas exhaustivas de la morfología de la superficie, el grosor, la composición y las propiedades eléctricas de la película para garantizar que cumple las normas exigidas.
-
Bucles de retroalimentación: Establecer circuitos de retroalimentación eficaces permite identificar y corregir rápidamente cualquier desviación de los resultados deseados. Este enfoque iterativo garantiza que cada ciclo de preparación de la película sea mejor que el anterior.
-
Consideraciones medioambientales: Al tiempo que se mejora la calidad de la película, también es crucial tener en cuenta el impacto medioambiental del proceso de preparación. Adoptar métodos energéticamente eficientes y minimizar los residuos puede contribuir a un ciclo de producción más sostenible.
Analizando y perfeccionando continuamente estos aspectos, se puede optimizar el proceso de preparación para obtener películas de alta calidad con mayor eficacia y menor huella medioambiental.
Protección del medio ambiente y consumo de energía
En la búsqueda de prácticas sostenibles dentro del proceso de sputtering por magnetrón, debe hacerse especial hincapié en la protección del medio ambiente y el consumo de energía. Los métodos tradicionales de sputtering, aunque eficaces, suelen presentar importantes inconvenientes medioambientales y energéticos. Para mitigarlos, la adopción de técnicas de preparación más respetuosas con el medio ambiente y eficientes desde el punto de vista energético no es sólo una recomendación, sino una necesidad.
Una forma de conseguirlo es optimizar los parámetros de sputtering. Ajustando factores como la potencia del sputtering, la velocidad de deposición y la temperatura del sustrato, es posible reducir la huella energética global del proceso. Por ejemplo, se pueden emplear potencias de sputtering más bajas sin comprometer la calidad de la película, con lo que se ahorra energía. Además, el uso de tecnologías de vacío avanzadas puede contribuir a mantener un medio ambiente más limpio al minimizar la emisión de gases y partículas nocivos a la atmósfera.
Por otra parte, la selección de materiales desempeña un papel crucial en la sostenibilidad medioambiental. Optar por materiales que sean menos tóxicos y tengan un menor impacto medioambiental puede mejorar significativamente el respeto por el medio ambiente del proceso. De este modo, no sólo se protege el medio ambiente, sino que también se garantiza el cumplimiento de una normativa medioambiental cada vez más estricta.
En resumen, aunque el principal objetivo del sputtering magnetrónico es la calidad y el rendimiento de la película de PZT, la integración de consideraciones medioambientales y energéticas en el proceso de preparación es igualmente importante. Este enfoque holístico garantiza que los avances en la tecnología de películas estén en consonancia con los objetivos más amplios de protección del medio ambiente y sostenibilidad.
CONTÁCTANOS PARA UNA CONSULTA GRATUITA
Los productos y servicios de KINTEK LAB SOLUTION han sido reconocidos por clientes de todo el mundo. Nuestro personal estará encantado de ayudarle con cualquier consulta que pueda tener. ¡Contáctenos para una consulta gratuita y hable con un especialista del producto para encontrar la solución más adecuada para sus necesidades de aplicación!