El revestimiento de un horno de inducción es un proceso crítico que garantiza la eficacia, seguridad y longevidad del horno.Implica el uso de materiales refractarios de alta calidad, como fibra de alúmina de gran pureza y materiales de fibra formados al vacío, para crear un revestimiento que pueda soportar altas temperaturas, ciclos rápidos de calentamiento y enfriamiento, y la naturaleza corrosiva de los metales fundidos.El procedimiento de revestimiento incluye varias etapas: selección del material, preparación y sinterización.El proceso de sinterización, que da forma al revestimiento en una estructura sólida, se divide en tres etapas: cocción, semisinterización y sinterización completa.El mantenimiento y la supervisión adecuados del revestimiento son esenciales para evitar su degradación y garantizar un rendimiento óptimo a lo largo del tiempo.
Explicación de los puntos clave:
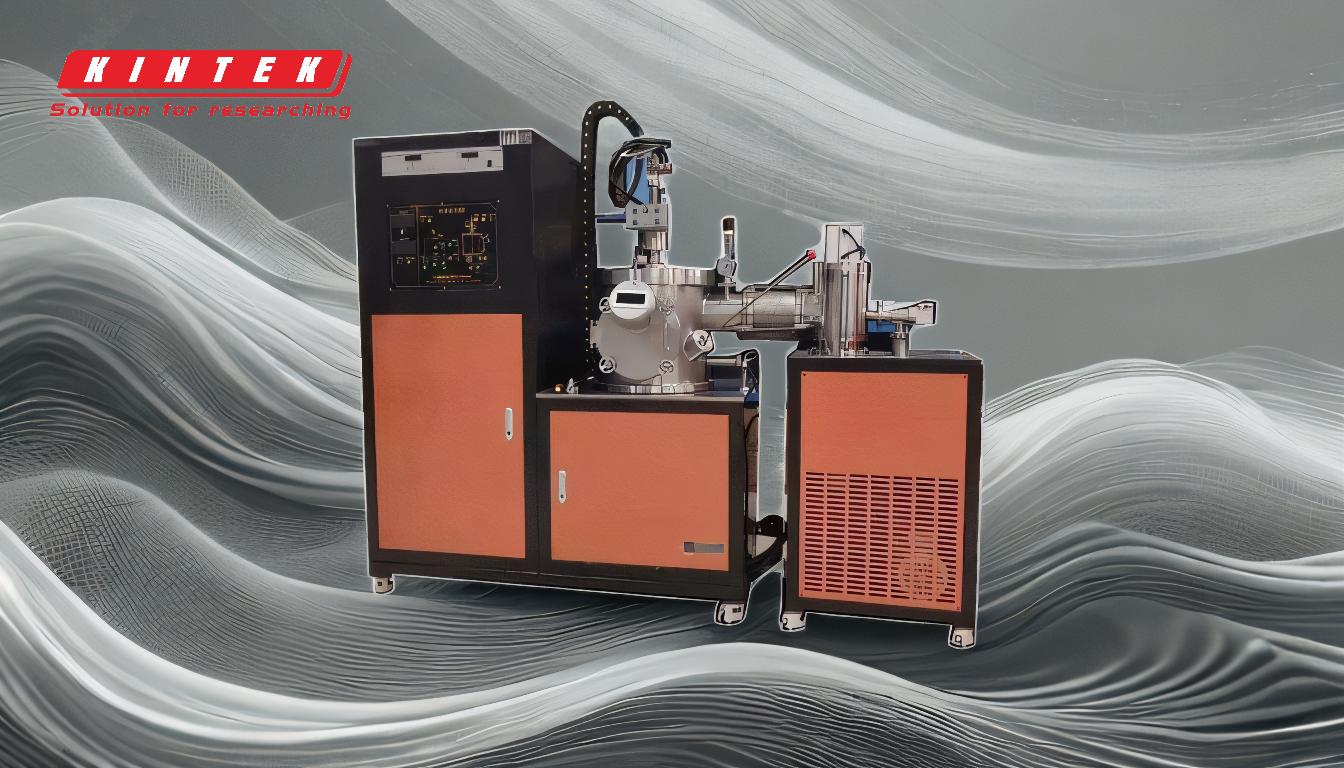
-
Finalidad del horno de inducción Revestimiento:
- El revestimiento sirve para contener el metal fundido, aislarlo de la estructura exterior del horno y proteger el cuerpo del horno durante su funcionamiento.
- Garantiza la seguridad, la eficacia y la calidad del producto final al evitar las fugas y mantener el aislamiento térmico.
-
Materiales utilizados en el revestimiento:
- Se suelen utilizar fibra de alúmina de gran pureza, material de fibra formado al vacío y placas huecas ligeras de óxido de aluminio.
- Estos materiales ofrecen altas temperaturas de servicio, pequeña capacidad de almacenamiento de calor, rápida resistencia al calor y al frío, y excelentes propiedades de aislamiento térmico.
-
Procedimiento de revestimiento:
- Preparación del material:Los materiales refractarios se preparan y moldean para adaptarse al interior del horno.
- Aplicación:Los materiales se aplican cuidadosamente para formar una capa de revestimiento uniforme, garantizando que no haya huecos ni puntos débiles.
-
Proceso de sinterización:
- Etapa de cocción:El revestimiento se calienta a 600°C para eliminar la humedad, lo que garantiza que el material esté seco y estable.
- Etapa de semisinterización:La temperatura se eleva a 900°C y después a 1200°C para sinterizar parcialmente el revestimiento, creando una estructura sólida.
- Etapa de sinterización completa:Se alcanza la temperatura final de sinterización, solidificando completamente el revestimiento y garantizando su durabilidad y rendimiento.
-
Importancia de una sinterización adecuada:
- Un proceso de sinterización bien ejecutado da como resultado un revestimiento con una buena microestructura, lo que mejora su resistencia al choque térmico, al agrietamiento y a la formación de escoria.
- La temperatura y la duración de la sinterización influyen significativamente en la vida útil del revestimiento y en la eficiencia global del horno.
-
Mantenimiento y supervisión:
- La inspección y el mantenimiento periódicos del revestimiento son cruciales para detectar y tratar cualquier signo de desgaste o degradación.
- La vida útil del revestimiento viene determinada por el número de ciclos térmicos que puede soportar antes de tener que ser reparado o sustituido.
-
Retos y consideraciones:
- Un mayor grosor del revestimiento puede provocar un mayor flujo de fuga, lo que reduce la potencia, el factor de potencia y la eficiencia eléctrica.
- La selección adecuada de los materiales refractarios y el cumplimiento del proceso de sinterización son esenciales para mitigar estos retos y garantizar la longevidad del revestimiento.
Siguiendo estos pasos y consideraciones, el revestimiento del horno de inducción puede instalarse y mantenerse eficazmente, garantizando un rendimiento y una seguridad óptimos en las operaciones de fusión de metales.
Tabla resumen:
Aspecto clave | Detalles |
---|---|
Finalidad | Contiene el metal fundido, aísla la estructura del horno, garantiza la seguridad y la calidad |
Materiales | Fibra de alúmina de gran pureza, fibra conformada al vacío, óxido de aluminio hueco ligero |
Procedimiento de revestimiento | Preparación del material, aplicación y sinterización |
Etapas de sinterización | Cocción (600°C), semi-sinterización (900°C-1200°C), sinterización completa |
Mantenimiento | Inspecciones periódicas para detectar el desgaste y garantizar un rendimiento óptimo |
Desafíos | El aumento del grosor del revestimiento reduce la potencia y la eficiencia eléctrica |
Optimice el revestimiento de su horno de inducción para obtener el máximo rendimiento. contacte hoy mismo con nuestros expertos ¡!