La velocidad de deposición en la soldadura depende de varios factores, como el tipo de proceso de soldadura, los ajustes del equipo, las propiedades del material y los parámetros operativos.Por ejemplo, en el revestimiento por láser, la velocidad de deposición depende de la potencia del láser, la velocidad de avance y la velocidad transversal.En el sputtering, influyen factores como las propiedades del material objetivo, la corriente y la energía del haz.En la soldadura con electrodo de hilo, variables como el tamaño del hilo, el amperaje y la posición de soldadura influyen significativamente en la velocidad de deposición.Comprender estos factores ayuda a optimizar los procesos de soldadura para obtener eficacia y calidad.
Explicación de los puntos clave:
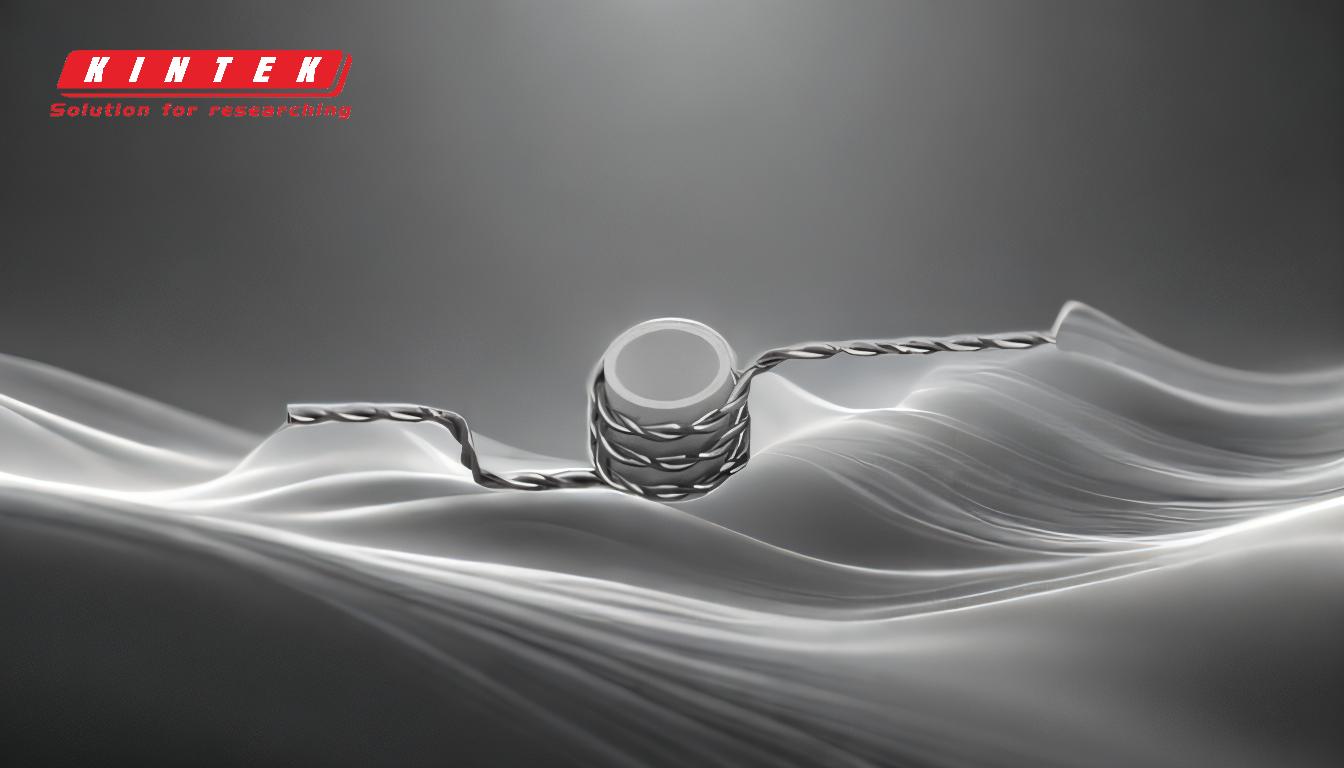
-
Potencia del láser en el revestimiento láser:
- La potencia del láser afecta directamente a la entrada de energía en el material, lo que influye en la velocidad de fusión y la eficacia de la deposición.
- Por lo general, una mayor potencia del láser aumenta la velocidad de deposición, pero debe equilibrarse para evitar defectos como el sobrecalentamiento o la deformación.
-
Velocidades de avance en el revestimiento por láser:
- La velocidad a la que se introduce el material (por ejemplo, polvo o alambre) en la zona de soldadura influye en la velocidad de deposición.
- Unas velocidades de alimentación óptimas garantizan una adición constante de material sin sobrealimentación ni subalimentación, lo que puede provocar defectos.
-
Velocidad transversal en el revestimiento por láser:
- La velocidad transversal determina la rapidez con la que el láser se desplaza por la pieza.
- Las velocidades transversales más rápidas pueden reducir las tasas de deposición pero mejorar la productividad, mientras que las velocidades más lentas aumentan las tasas de deposición pero pueden provocar un aporte excesivo de calor.
-
Características del plasma en el depósito por plasma:
- La temperatura, la composición y la densidad del plasma influyen en la velocidad y la calidad de la deposición.
- El control de estos parámetros garantiza las propiedades deseadas del material y minimiza la contaminación.
-
Propiedades del material en el sputtering:
- Las propiedades físicas del material objetivo, como la densidad y el punto de fusión, afectan a la facilidad con la que se puede bombardear y depositar.
- Los materiales con puntos de fusión más bajos y rendimientos de sputtering más elevados suelen tener tasas de deposición más altas.
-
Corriente y energía del haz en el sputtering:
- Una corriente y una energía del haz más elevadas aumentan la velocidad de sputtering, lo que se traduce en mayores tasas de deposición.
- Sin embargo, una energía excesiva puede dañar el blanco o el sustrato, por lo que la optimización es crucial.
-
Tamaño del electrodo de alambre en soldadura:
- Los electrodos de hilo más grandes pueden depositar más material por unidad de tiempo, lo que aumenta la tasa de deposición.
- Por ejemplo, un electrodo de hilo de 1,4 mm a 250 amperios tiene una tasa de deposición de 3,5 kg/hora en posición plana u horizontal.
-
Amperaje en soldadura:
- Un mayor amperaje aumenta la entrada de calor y la velocidad de fusión, lo que conduce a mayores tasas de deposición.
- Una selección adecuada del amperaje garantiza una deposición eficaz sin comprometer la calidad de la soldadura.
-
Posición de soldadura:
- La posición (por ejemplo, plana, horizontal, vertical, por encima de la cabeza) afecta a la influencia de la gravedad en el baño de fusión, lo que repercute en la velocidad de deposición.
- Las posiciones planas y horizontales suelen permitir mayores velocidades de deposición que las posiciones verticales o por encima de la cabeza.
-
Composición del material y contaminación:
- Garantizar la composición elemental correcta en el proceso de soldadura es fundamental para conseguir las propiedades deseadas del material.
- La contaminación puede reducir las tasas de deposición y comprometer la integridad de la soldadura, por lo que la supervisión es esencial.
Al comprender y optimizar estos factores, los soldadores y los ingenieros pueden lograr mayores tasas de deposición manteniendo la calidad y la eficacia de la soldadura.
Tabla resumen:
Factor | Impacto en la tasa de deposición |
---|---|
Potencia del láser (revestimiento láser) | Una mayor potencia aumenta la velocidad de deposición, pero se corre el riesgo de sobrecalentamiento o deformación. |
Velocidades de alimentación (revestimiento láser) | Las velocidades óptimas garantizan una adición de material constante y sin defectos. |
Velocidad transversal (revestimiento láser) | Las velocidades más rápidas reducen las tasas de deposición pero mejoran la productividad. |
Características del plasma | La temperatura, la composición y la densidad influyen en la calidad de la deposición. |
Propiedades del material | Los puntos de fusión más bajos y los mayores rendimientos de sputtering aumentan las tasas de deposición. |
Corriente y energía del haz | Una mayor energía aumenta la velocidad de sputtering, pero debe optimizarse para evitar daños. |
Tamaño del electrodo de alambre | Los alambres más grandes depositan más material por unidad de tiempo, lo que aumenta la velocidad de deposición. |
Amperaje | Un mayor amperaje incrementa el aporte de calor y la velocidad de fusión, aumentando las tasas de deposición. |
Posición de soldadura | Las posiciones plana y horizontal permiten mayores tasas de deposición que las verticales o por encima de la cabeza. |
Composición del material | Una composición correcta garantiza las propiedades deseadas; la contaminación reduce las tasas de deposición. |
¿Está listo para optimizar su proceso de soldadura? Póngase en contacto con nuestros expertos para obtener soluciones a medida.